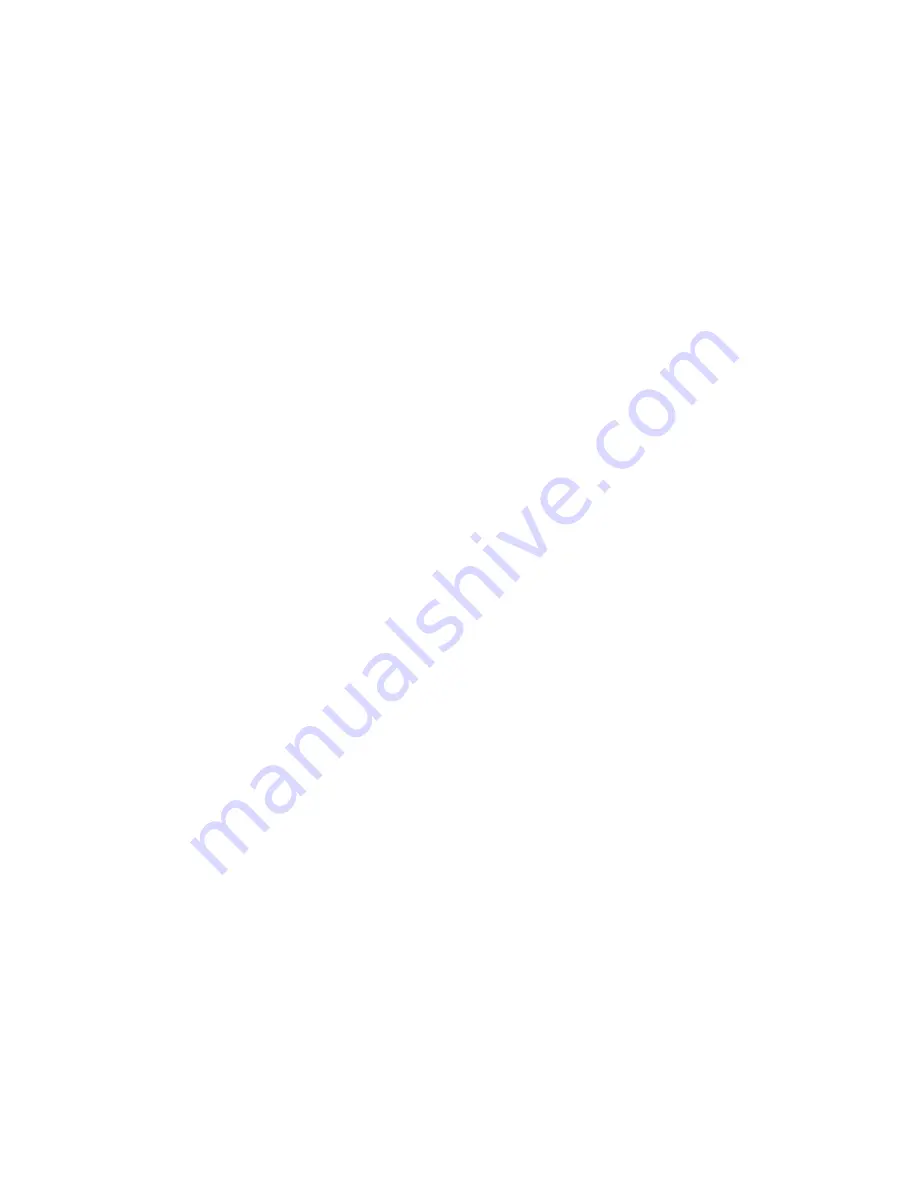
32
indicated in the end-of-driving graphs, or the impact
energy of the hammer is too high and the penetration
of the pile stops abruptly, for example, when the pile
encounters a big stone. There, it is recommended to
decrease the impact force of the hammer. The end-
of-driving instructions present the smallest pile size
recommended to be installed with each hammer.
If a hammer is used to install piles smaller than the
recommended pile size, impact force must be limited
below the maximum.
When installing raking piles, it should be noted that
the impact energy transmitted to the pile may be
considerably lower than with vertical piles.
With large diameter piles and pile driving equipment/pile
combinations that have not been analysed earlier, driving
stresses may be evaluated by simulations based on the
stress wave theory.
The magnitude of driving stresses and the centricity of
the blow can be best determined by dynamic load tests.
If the cutting level of the pile is below ground or water level,
a follower aligned with the longitudinal axis of the pile can
be installed between the pile driver helmet and pile head.
The follower pile should have about the same impedance
as the actual pile, in other words, the follower should be
a steel pipe of a steel cross section equal or almost equal
(+/- 20 %) to that of the actual pile. The follower must be
guided well and sit tightly on the end of the pile.
7.3.4 Additional installation instructions and splicing
of RR75 to RR220 piles
The driving of RR75 to RR220 piles is usually started with
an unspliced pile section, for example, a piece cut-off
earlier. Before installation a shoe (bottom plate or rock
shoe) is attached to the bottom of the pile, for example, by
using a sledge-hammer. The hardened dowel of the rock
shoe must not be hit due to the risk of chipping. The shoe
has a machined groove and the dowel is positioned so that
the groove coincides with the internal burr of the pile pipe.
A friction shoe must be attached tightly enough to the pile
pipe so that it cannot be loosened by tensile stress during
the impact. The final “tightening” of the shoe occurs during
the end-of-driving. It must be ensured that the shoe is
aligned with the pile pipe during attachment.
If the piles have inadequate lateral support, the risk of
buckling during installation is taken into account, for
example, by selecting suitable installation equipment and
section length for the pile.
The external splice sleeve of an RR pile can be either at
the top or bottom of the pile. Driving a pile with a splice
sleeve at the top requires an adapter that transmits the
blow past the splice sleeve to the pile pipe.
The external splice sleeve of a pile must not be hit.
When an internal splice is used, the splice is installed to the
bottom pile section so that the relief groove in the splice
piece coincides with the longitudinal weld of the pile. The
splice piece is pressed or driven carefully for some distance
so that a gap remains between the pile and the splice
piece. The next pile section is installed correspondingly
on the splice so that the relief groove coincides with the
longitudinal weld.
Before pile splicing, the condition of the upper end of
the pile is inspected and a damaged part is repaired or
removed.
7.3.5 Additional instructions for the installation of
RR270 to RR1200 piles
The pile must be supported at the beginning of driving so that it
stays in the designed position and inclination. While the driving
is under way, the pile support system must guide the pile so that
it is continuously supported at the cutting level. If adequate
support to the upper end of the pile is unreasonably hard to
provide, the position and inclination of the upper end must be
monitored during piling. If the pile is found to deviate from the
designed position or inclination, an effort must be made to
correct them. If the pile tip encounters a stone or boulder in the
subsoil and consequently tends to change direction, it must be
possible to relax the guidance so that the pile can circumvent
obstacles without curving. If guidance needs to be relaxed more
than the tolerances set for pile position and inclination allow,
the structural dimensioning of the pile foundation must be
revised.
RR270 to RR1200 piles are spliced by welding according to Sec.
7.5. Before splicing, the condition of the upper end of the pile is
inspected and a damaged part is repaired or removed.
When large diameter piles with a closed shoe are installed in
a water body or below ground water level, they are subject
to a buoyancy force, which may exceed the weight of the pile
and the resistance due to skin friction during an interruption
in driving in cohesion soils or loose friction soils. Then, the
buoyancy force may make the pile rise or hinder its penetration.
A simple solution to that problem is to fill the piles partly or fully
with water to achieve sufficient counterweight. The magnitude
of the buoyancy force increases with increasing pile diameter
(and decreasing wall thickness), and it is recommended that the
buoyancy be taken into account already at the design stage
starting from about pile size RR800.
When specifying pile order lengths, it should be taken into
account that a “length” of 2·
d
at the upper end of the pile
must be reserved for PDA measurement.
7.3.6 Additional instructions for rock shoes with
hollow dowel
When using large diameter piles with hollow dowel rock shoes,
the hole in dowel must be filled with concrete before installation
to prevent the hole from contracting. After installation, the hole
is drilled open for example to install an anchor bar.