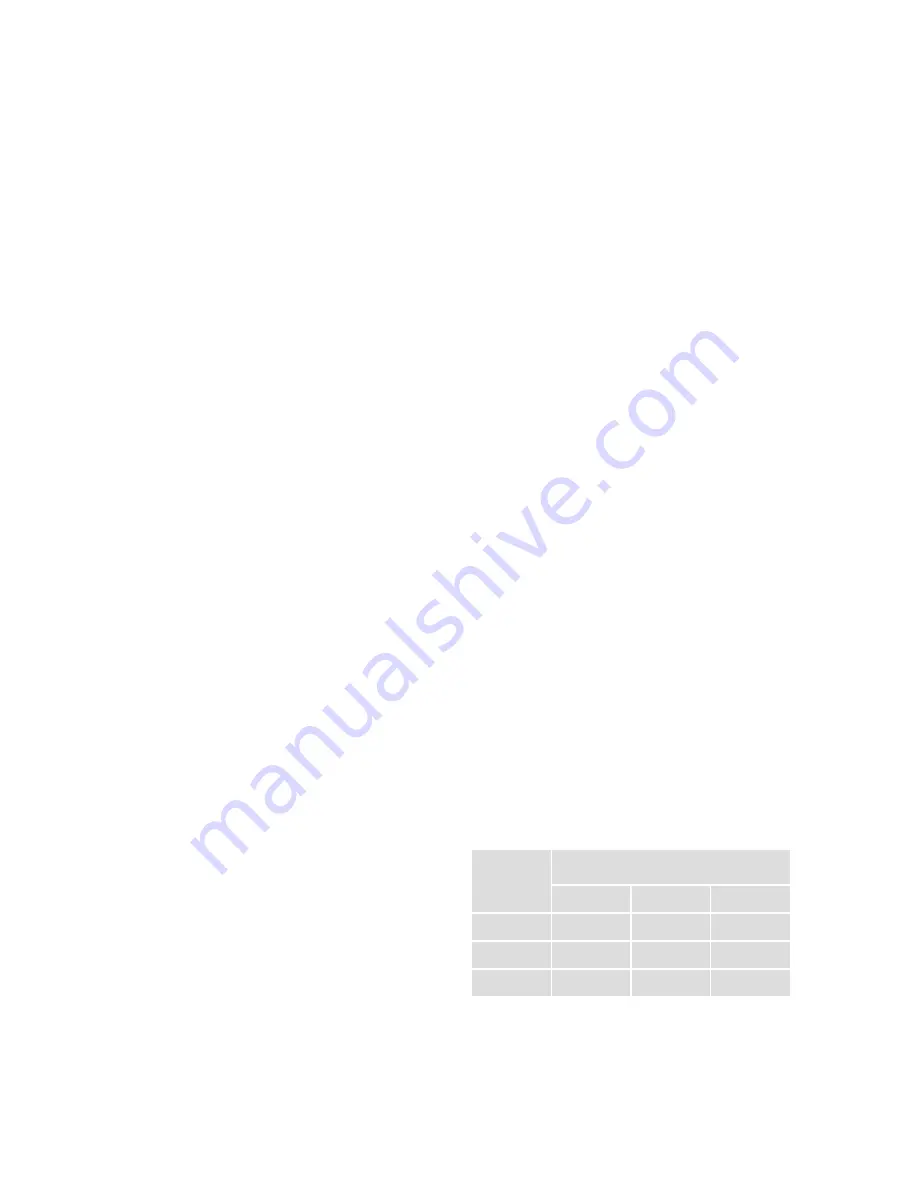
38
During the manufacture of longitudinally welded pipes,
burr forms on their interior surface. Removal of the burr
is generally unnecessary when using the most common
drill bits, but the burr should be considered when choosing
the pilot bit. The internal burr can be removed by special
order during the manufacture of a pipe pile.
Protection of threads
Care must be taken not to damage the threads while
raising a pile section upright. Light pile sections may
be raised upright without mechanical protection of the
ends. It is recommended to protect heavier sections, for
instance, by a protective cap or sleeve of plastic or metal.
The protection may be of the screw-on type or one that is
locked mechanically onto the section.
Cleaning and lubrication
Before screwing the sleeve into place, it must be ensured
that the end of the pile section and the threads in the
sleeve are clean and undamaged. The threads are to
be cleaned with a brush, water or compressed air, if
necessary. If surface rust has formed in the threads during
storage, it is recommended to remove the rust before
installation, for example, by a steel brush.
To ensure proper tightening of the threaded sleeve, the
cleaned threads of the pile section and/or threaded
sleeve should be lubricated, for instance, with a
biodegradable lubricant before installing the sleeve. Use
of viscous lubricating grease may, especially under cold
conditions, make tightening of the splice more difficult.
Tightening
When installing the splice, proper engagement of the
threads must be ensured. The sleeve is screwed manually
onto the pile section and is then pre-tightened by chain
tongs or the rotary unit of the piling equipment. Then
the upper pile section is installed and final tightening
to at least the required tightening torque is performed.
The minimum values of required tightening torques
are presented in Table 27. Use of the minimum values
requires that threads are clean and there are no
mechanical damages to the threads.
During final tightening care must be taken not to squeeze
the splice which prevents its tightening. The lower and
upper pile elements should be gripped when tightening,
not the sleeve, especially when tightening is done by
piling equipment.
The threaded sleeve splice is dimensioned so as to meet
the set requirements at the minimum tightening torque
values presented in Table 27 even if the heads of the
pile elements are not in contact. Bringing the heads into
contact normally requires a higher than recommended
tightening torque.
7.5 Splicing of steel pipe piles by welding
All steels used in SSAB's steel piles are highly weldable.
7.5.1 Welding Plan
A detailed welding plan is drawn up as part of the piling
plan. The welding plan is to include the following:
• steel grade
• weld quality level
• welding procedure
• welding consumables
• possible preheating
• welding conditions
• types of joint preparation
• welding positions
• a welding procedure specification (WPS)
• welding procedure tests, when required
• production weld test, when required
• welder qualifications
• after-treatment of welds, if required
• weld inspection instructions
7.5.2 Welding quality requirements
The welding, inspection, testing, and related functions
are to meet at least the requirements of Standard EN ISO
3834-4.
Welded joints are usually sufficiently strong and ductile
provided that the welding procedure has been carried
out carefully. In exacting applications, the mechanical
properties of welded joints may also be ensured through
welding procedure tests and/or production weld tests.
Unless otherwise specified in the designs, the weld quality
levels required for pile splices according to standard EN ISO
5817 are determined as indicated in Table 28.
Table 28. Weld quality levels required of steel pile splices
(EN ISO 5817)
Piling
class
Consequence class
CC1
CC2
CC3
PTL3
C
C
B
PTL2
C
C
C
PTL1
D
-
-
If a RR or RD pile only acts as a casing (not a load-bearing
structural member), weld quality class is D.
If the weld quality level requirement of Table 28 is
not observed, the weld quality level is to be selected
considering static and dynamic loads on the structure,