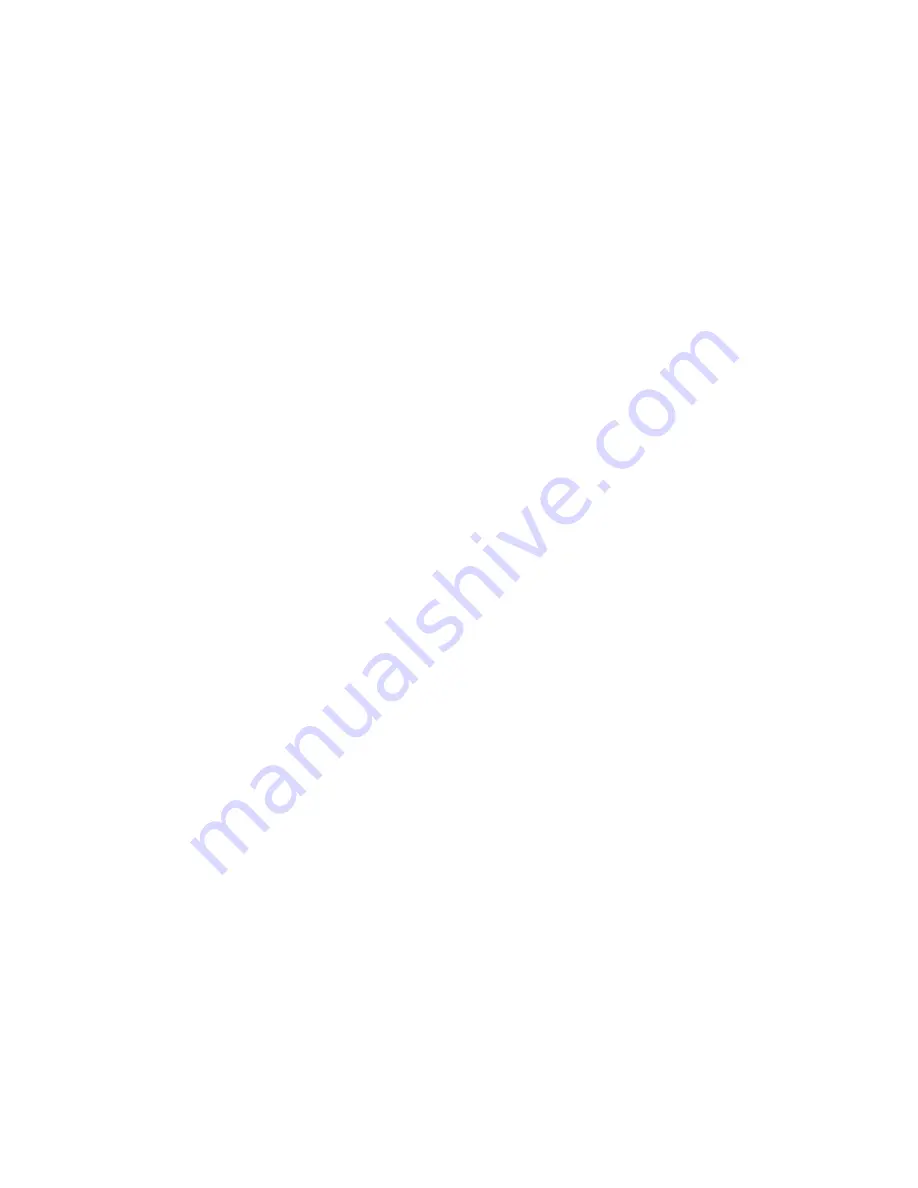
35
A guide sleeve attaches the drill rods inside the RD pile
to the DTH hammer, which, again, is attached to the drill
bit by the shank adapter of the guide device above the
pilot bit. Blows are transmitted via the guide device to
the casing shoe, whereby the RD pile is “pulled” into the
ground. The rotary unit above the head of the pile rotates
the drill rods.
DTH hammer-based drilling equipment can drill large
diameter piles up to RD1200 pile size. Pile length affects
drilling capacity and installation speed minimally at
practicable pile lengths.
Experience tells us that RD piles installed with a DTH
hammer are generally somewhat straighter than RD piles
installed with a top hammer.
7.4.1.3 The eccentric drilling method
The eccentric drilling method uses a pilot bit and an
integrated eccentric reamer bit. The method is usable
with both DTH hammer- and top hammer-based drilling
equipment.
During drilling, an eccentric reamer bit enlarges the hole
made by the pilot bit slightly bigger than the outside
diameter of the RD pile. The RD pile is pulled into the
ground with the drill bit and the casing shoe welded to the
casing.
The flushing agent transfers part of the soil to be removed
to the surrounding soil. Part of the soil is flushed up along
the outer surface of the RD pile to surface while part of it
exits through the RD pile.
When the target depth is reached, the drill rods are
rotated in the opposite direction to drilling whereby the
drill bit’s reamer portion closes and the drill bit, drill rods
and any possible hammer drill can be removed from inside
the RD pile. Drilling may be continued as rock drilling
either using a separate rock bit or, in certain cases, with
the same bit.
When using the eccentric drilling method and traditional
single reamer bit equipment (ODEX or equivalent), the
lower end of an RD pile installed in rock always ends up
resting on a “shelf” whose dimensions are determined
by the used drill bit. The impact of the rock shelf on the
geotechnical resistance of a pile must be considered in
pile design and inspection.
7.4.1.4 The concentric drilling method
In the concentric drilling method, three types of reamer bits
are used. Reamer bit can be made of fixed or unattached
ring bit. During drilling, the ring bit is locked onto the pilot
bit. After drilling, the pilot bit is detached from the ring bit
and extracted. Reamer bit can also be made of several
concentric reamer wings. At the beginning of drilling, reamer
wings are opened. After drilling, the drill rods are rotated in
the opposite direction to drilling whereby the reamer wings
close and whole drill bit can be removed from inside the RD
pile. With reamer wings the casing shoe is not necessary part
of load bearing structure of the RD pile.
Especially when using wing bits, but also when using ring bits,
the compatibility of the tolerances of the pilot bit, the casing
shoe and the pile pipe must be paid attention to. Particularly
should be checked, if the tolerance between the head of
the pilot bit and the casing shoe is suitable for the out of
roundness tolerance of the pile pipe size in question.
When drilled piles are long or soil conditions are
demanding with boulders or stony soils, casing shoe
model has an effect on installation reliability. In such
cases it has been found out that only surface hardened
flat steel ring attached to inner surface of pile pipe is
susceptible to deformations and also damaging during
installation.
If necessary, drilling may be continued as rock drilling.
There are also drill bit systems on the market that allow
continuing rock drilling with the same pilot bit, so-called
drill-through systems.
The method can be used with both DTH hammer- and
top hammer-based drilling equipment. Experience tells
us that the concentric drilling method generally produces
straighter RD piles than eccentric methods based on a
single reamer bit. In demanding conditions (boulders,
stony soil) a concentric drilling with ring reamer is usually
more reliable and faster than eccentric drilling or several
concentric reamer wings.
7.4.2 Start of installation
The pile is placed exactly in the planned position and its
verticality or inclination is checked, for example, by a
bubble level. At sites where tight positional and inclination
tolerances have been set for RD piles, special attention
must be paid to measurements. In the initial phase of
installation, when the tip of the pile has penetrated some
distance into the ground, the inclination and position of
the pile are checked. In case the positional deviation is
estimated or measured to be too big, the pile is extracted
and repositioned. Straightening of a pile deviating slightly
from the planned inclination may be attempted by changing
the inclination of the mast slightly in the early phase.
7.4.3 Drilling of RD piles
The instructions and recommendations of the hammer
and drill bit manufacturer are followed in drilling RD piles.
The casing shoe or integrated casing shoe/ring bit is
generally welded to the RD pile pipe as per instructions
of the manufacturer. The ring bit used with concentric
drilling methods are attached to the casing shoe as per
instructions of the manufacturer. The casing shoe and