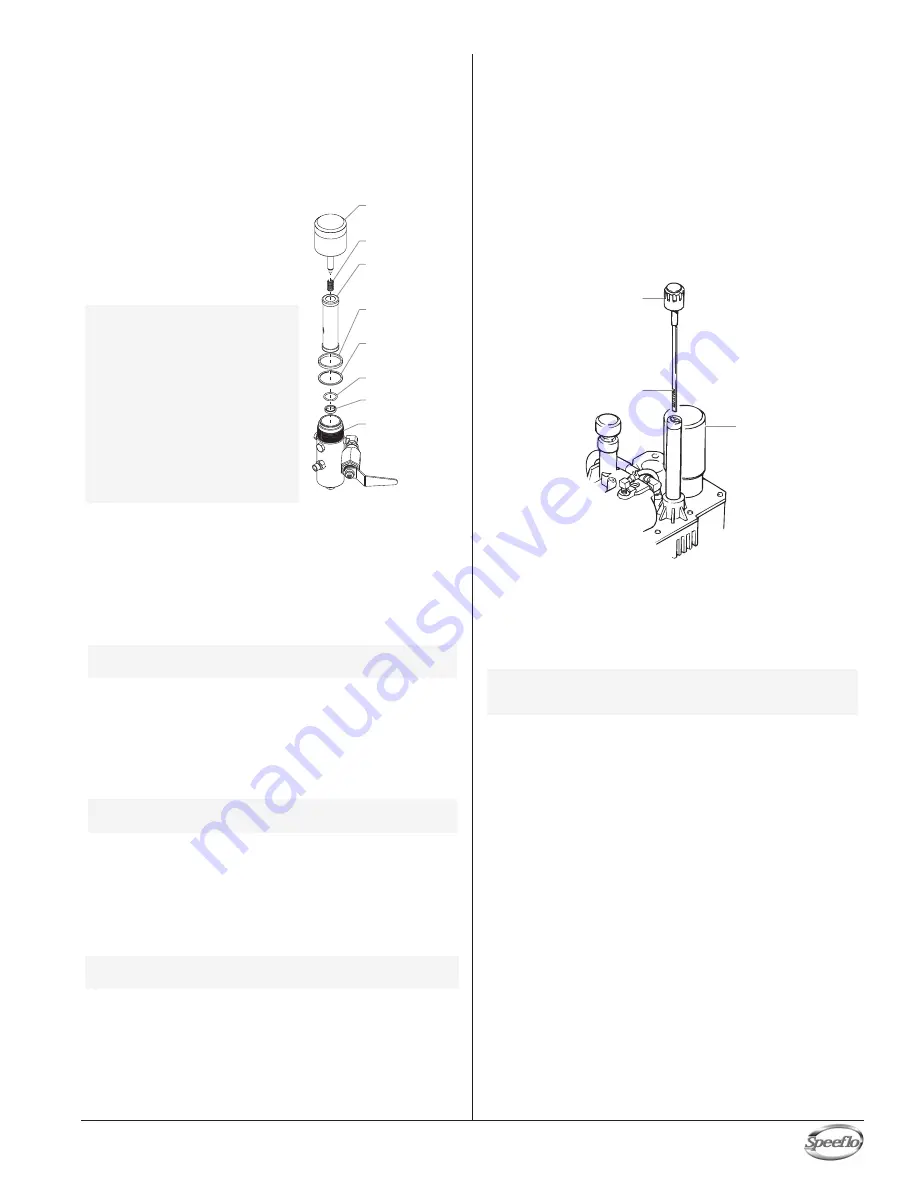
Maintaining the Filter Assembly
Clean the filter regularly. Dirty or clogged filters can greatly
reduce filtering ability and cause a number of system problems
including poor spray patterns, clogged spray tips, etc.
Cleaning
To clean the filter, perform the following procedure.
1. Follow the “Pressure Relief Procedure” found in the
Operation section of this manual.
2. Remove the filter cap assembly
and spring.
3. Pull the filter element with ball
straight out of the filter body.
4. Clean inside the filter body,
filter element with ball, and filter
cap assembly using the
appropriate solvent.
Inspection
Inspect all parts of the filter assembly before reassembly.
1. Inspect the ball inside the filter element. If the ball has
pressure cuts or scratches, replace the filter element.
a. If the ball is cut, remove the Teflon o-ring using an o-
ring pick and remove the carbide seat.
b. Check the seat for nicks or grooves. If the seat is
damaged, replace.
2. Remove the spring from the spring guide on the filter cap.
a. Measure the length of the spring uncompressed. If it
measures less the 3/4” from end to end, replace.
b. Push the spring back onto the spring guide until it
“snaps” back into position.
3. Inspect the two Teflon gaskets and the Teflon o-ring for
deformity, nicks, or cuts. Replace, if needed.
Reassembly
After cleaning and inspecting all parts, reassemble the filter.
1. Place the carbide seat into the filter body. Make sure the
beveled side of the seat is facing up.
2. Place the Teflon o-ring into the groove on the outer
diameter of the carbide seat.
3. Place the filter element with ball into the filter body.
4. Push the spring back onto the spring guide of the filter cap
until it “snaps” back into position, if not already done.
5. Place the thin Teflon gasket onto the step at the top of the
filter body.
6. Place the thick Teflon gasket onto the top of the thin
gasket.
7. Tighten the filter cap assembly onto the filter body.
NOTE: The top and bottom of the filter element with
ball are identical.
NOTE: The Teflon gaskets, Teflon o-ring, and spring
are packaged in Filter Service Kit P/N 930-050.
NOTE: Removal of the Teflon o-ring will damage the
o-ring and require replacement.
NOTE: Use care in handling
parts as dirt, debris,
scratches, or nicks
may prevent o-rings or
gaskets from sealing.
This filter element
filters from the inside
out. Be sure to clean
the filter element
thoroughly on the
inside. Soak in
solvent to loosen
hardened paint or
replace.
Filter Cap
Assembly
Filter
Element
w/Ball
Teflon Gasket
(thick)
Teflon Gasket
(thin)
Teflon O-ring
Carbide Seat
Filter Body
Spring
Maintaining the Hydraulic System
IMPORTANT: Use of Speeflo's Coolflo™ Hydraulic Fluid is
mandatory in the PowrTwin hydraulic system. Do not use
any other hydraulic fluid. Use of any other hydraulic fluid
may seriously damage the hydraulic system and will void
the warranty.
1. Check the hydraulic fluid daily. It should be at the “Full”
mark on the dipstick. If it is low, add only Speeflo
Coolflo™ Hydraulic Fluid (P/N 430-361). Never add or
change hydraulic fluid except in a clean, dust-free area.
Contamination of the hydraulic fluid will shorten hydraulic
pump life and may void warranty.
2. Change the hydraulic fluid every twelve months. Drain the
old fluid from the tank and fill with 4 quarts of Speeflo
Coolflo™ Hydraulic Fluid. Start the sprayer at just enough
pressure to operate the fluid section. Run the sprayer at
this low pressure for at least 5 minutes. This removes air
from the system. Check the fluid level after this
procedure. Do not over-fill.
3. The hydraulic system has an external, replaceable
hydraulic filter. Change the filter every twelve months.
4. The hydraulic pump should not be serviced in the field. If
service on the hydraulic pump is required, it must be
returned to Speeflo.
Maintaining the Fluid Section
If the sprayer is going to be out of service for an extended
period of time, it is recommended that following cleanup a
mineral spirits and oil mixture be introduced as a preservative.
Packings may tend to dry out from lack of use. This is
particularly true of the upper packing set for which upper
packing lubricant Piston Lube (P/N 314-480) is recommended
in normal usage.
If the sprayer has been out of service for an extended period
of time, it may be necessary to prime the pump with solvent. It
is extremely important that the threads on the siphon
tube/hose coupling are properly sealed. Any air leakage will
produce erratic operation of the sprayer and may damage the
system. The up and the down strokes should be approximately
equal in time (one should not be faster than the other). A fast
up or down stroke may indicate air in the system or
malfunctioning valve or seats (see the Troubleshooting
section).
NOTE: When replacing the hydraulic filter during a
fluid change, it may be necessary to add up to
one additional quart of hydraulic fluid.
"Full" Mark
Hydraulic Fluid
Cap/Dipstick
Hydraulic
Filter
© Titan Tool Inc. All rights reserved.
11