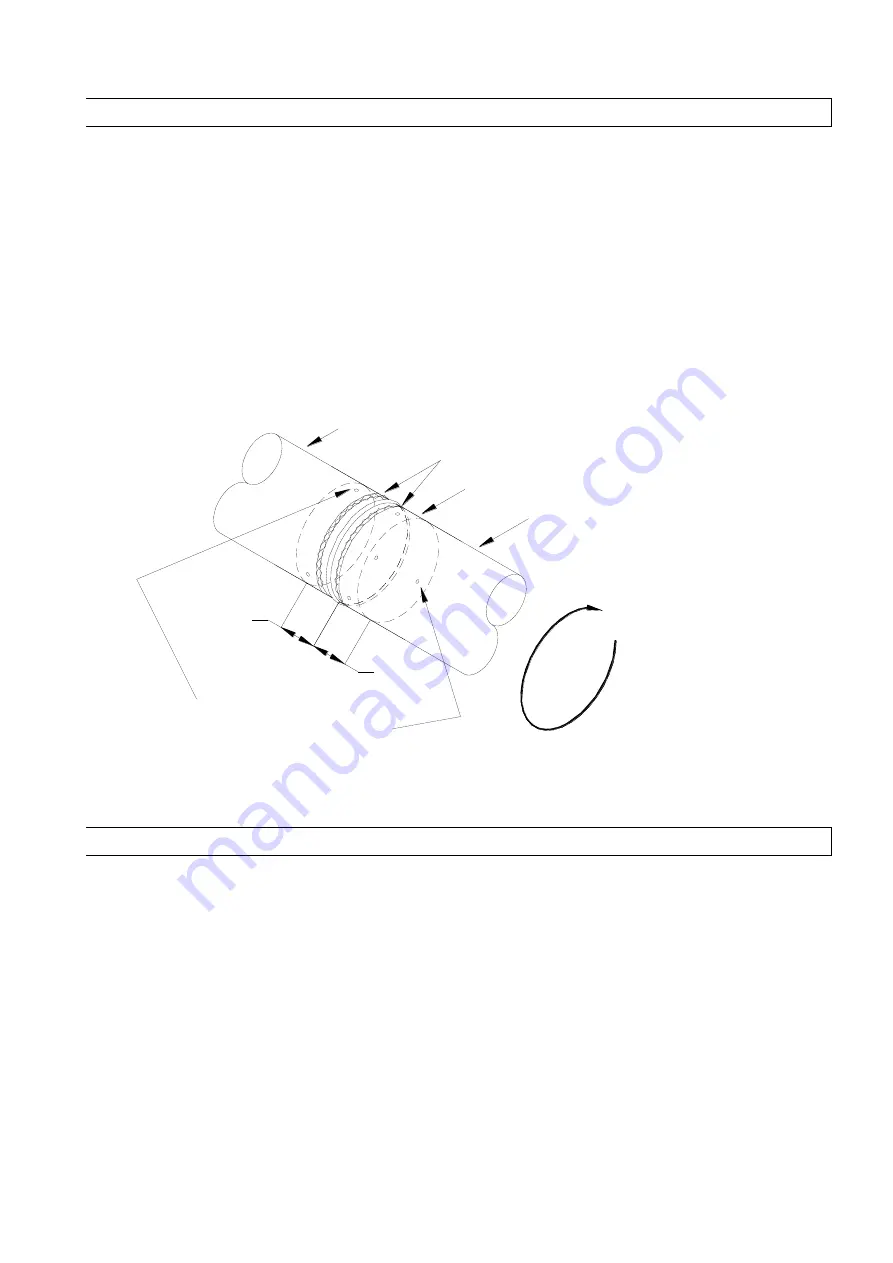
Form 44201129
Oct 2019 rev A
11
9.0)
SYSTEM EXHAUST MANIFOLD
1. All exhaust manifold tube is manufactured to a standard diameter. All joint connections, on all sizes of
fittings, push fit into the relative tube and should be sealed using high temperature silicone sealant. No
locking bands are required.
2. Tube joints should be made as follows:-
Cut tube to length required, remove all burrs and wipe off any oil or grease with a clean rag. Apply a bead
(3mm) of high temperature silicone sealant around both the outer end of the fitting and the inner end of the
tube. Insert the fitting into the tube up to the raised bead around the fitting. (50mm) using a slight rotary
action to spread the sealant (Fig. 11).
NOTE: The sealant remains workable for approximately 5 minutes after application.
3. Finally, secure the joint by drilling 3 equally spaced holes (Ø5.5mm) through both the tube and fittings (one
hole to be at 12 o’clock to prevent possible leakage of condensate) and rivet the tube to the fittings Ø5 x 6
pop rivets.
Fig. 11
10.0)
COMMISSIONING
Inspect the installation and ensure that the appliance, exhaust manifold and any combustion air ducting has
been assembled and installed in accordance with the relevant section of these Installation, Service and
Operating Instructions.
It is essential that all new pipework installations are purged and tested for soundness with a suitable leak
detection fluid prior to attempting to ignite any appliance. This work should be carried out in accordance with
National or Local regulations.
N.B. DO NOT TEST FOR SOUNDNESS BY USE OF NAKED FLAMES.
Spiral wound manifold
push fit fittings with raised bead
3mm bead of high temp. silicone sealant
Spiral wound manifold
3No. equally spaced holes Ø5.5mm
for Ø5mm pop rivets.
(one hole to be at 12 o'clock
to prevent condensate leakage)
50mm
50mm
Insert fitting using
slight rotary action
to spread sealant
Содержание ADL25-HB
Страница 17: ...Form 44201129 Oct 2019 rev A NOTES...