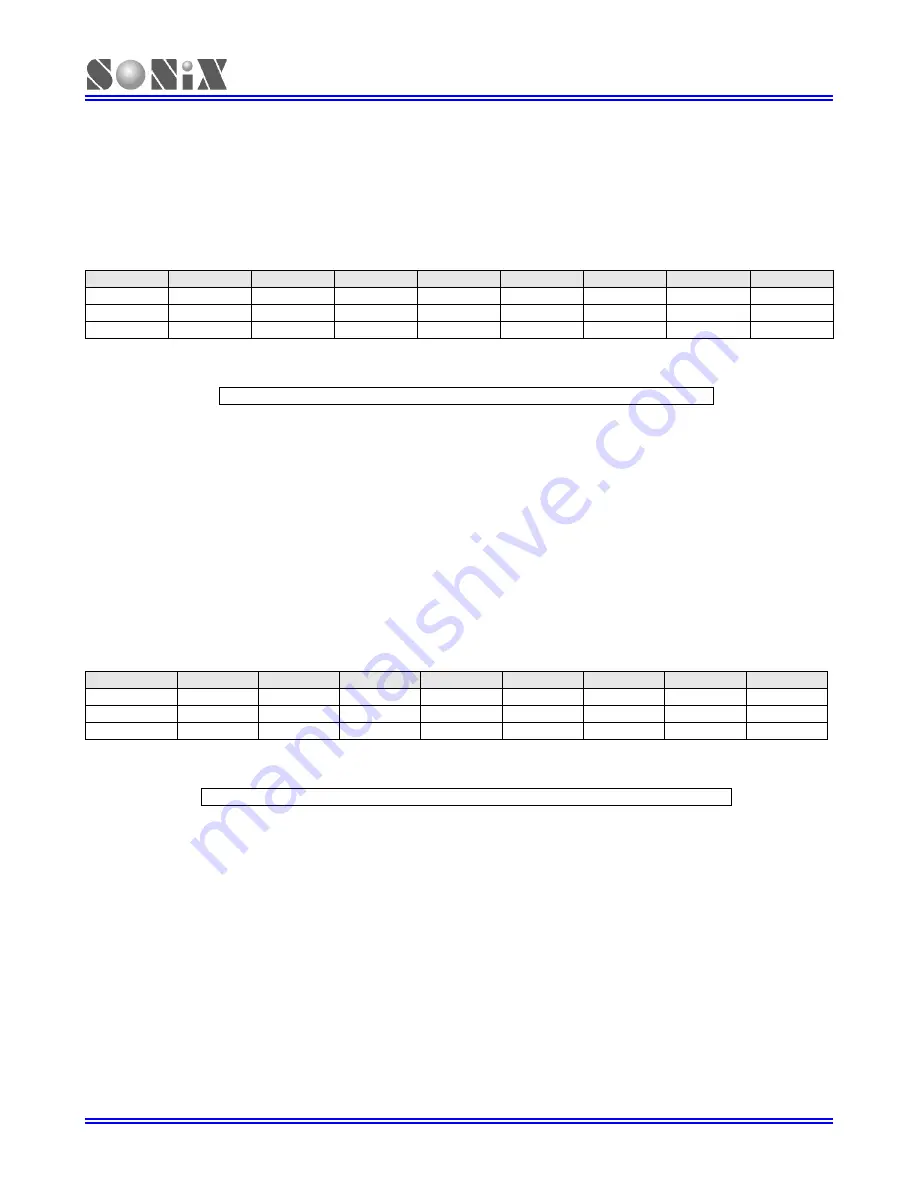
SN8P2318 Series
C-type LCD, RFC 8-Bit Micro-Controller
SONiX TECHNOLOGY CO., LTD
Page 85
Version 1.5
8.3.5 TC0R AUTO-RELOAD REGISTER
TC0 timer builds in auto-reload function, and TC0R register stores reload data. When TC0C overflow occurs, TC0C
register is loaded data from TC0R register automatically. Under TC0 timer counting status, to modify TC0 interval time
is to modify TC0R register, not TC0C register. New TC0C data of TC0 interval time will be updated after TC0 timer
overflow occurrence, TC0R loads new value to TC0C register. But at the first time to setup TC0M, TC0C and TC0R
must be set the same value before enabling TC0 timer. TC0 is double buffer design. If new TC0R value is set by
program, the new value is stored in 1
st
buffer. Until TC0 overflow occurs, the new value moves to real TC0R buffer.
This way can avoid any transitional condition to effect the correctness of TC0 interval time and PWM output signal.
0CDH
Bit 7
Bit 6
Bit 5
Bit 4
Bit 3
Bit 2
Bit 1
Bit 0
TC0R
TC0R7
TC0R6
TC0R5
TC0R4
TC0R3
TC0R2
TC0R1
TC0R0
Read/Write
W
W
W
W
W
W
W
W
After reset
0
0
0
0
0
0
0
0
The equation of TC0R initial value is as following.
TC0R initial value = 256 - (TC0 interrupt interval time * TC0 clock rate)
Example: To calculation TC0C and TC0R value to obtain 10ms TC0 interval time. TC0 clock source is
Fcpu = 16MHz/16 = 1MHz. Select TC0RATE=000 (Fcpu/128).
TC0 interval time = 10ms. TC0 clock rate = 16MHz/16/128
TC0C/TC0R initial value = 256 - (TC0 interval time * input clock)
= 256 - (10ms * 16MHz / 16 / 128)
= 256 - (10
-2
* 16 * 10
6
/ 16 / 128)
= B2H
8.3.6 TC0D PWM DUTY REGISTER
TC0D register
’s purpose is to decide PWM duty. In PWM mode, TC0R controls PWM’s cycle, and TC0D controls the
duty of PWM. The operation is base on timer counter value. When TC0C = TC0D, the PWM high duty finished and
exchange to low level. It is easy to configure TC0D to choose the right PWM
’s duty for application.
0E8H
Bit 7
Bit 6
Bit 5
Bit 4
Bit 3
Bit 2
Bit 1
Bit 0
TC0D
TC0D7
TC0D6
TC0D5
TC0D4
TC0D3
TC0D2
TC0D1
TC0D0
Read/Write
R/W
R/W
R/W
R/W
R/W
R/W
R/W
R/W
After Reset
0
0
0
0
0
0
0
0
The equation of TC0D initial value is as following.
TC0D initial value = TC0R + (PWM high pulse width period / TC0 clock rate)
Example: To calculate TC0D value to obtain 1/3 duty PWM signal. The TC0 clock source is Fcpu =
16MHz/16= 1MHz. Select TC0RATE=000 (Fcpu/128).
TC0R = B2H. TC0 interval time = 10ms. So the PWM cycle is 100Hz. In 1/3 duty condition, the high pulse width is
about 3.33ms.
TC0D initial value = B2H + (PWM high pulse width period / TC0 clock rate)
= B2H + (3.33ms * 16MHz / 16 / 128)
= B2H + 1AH
= CCH