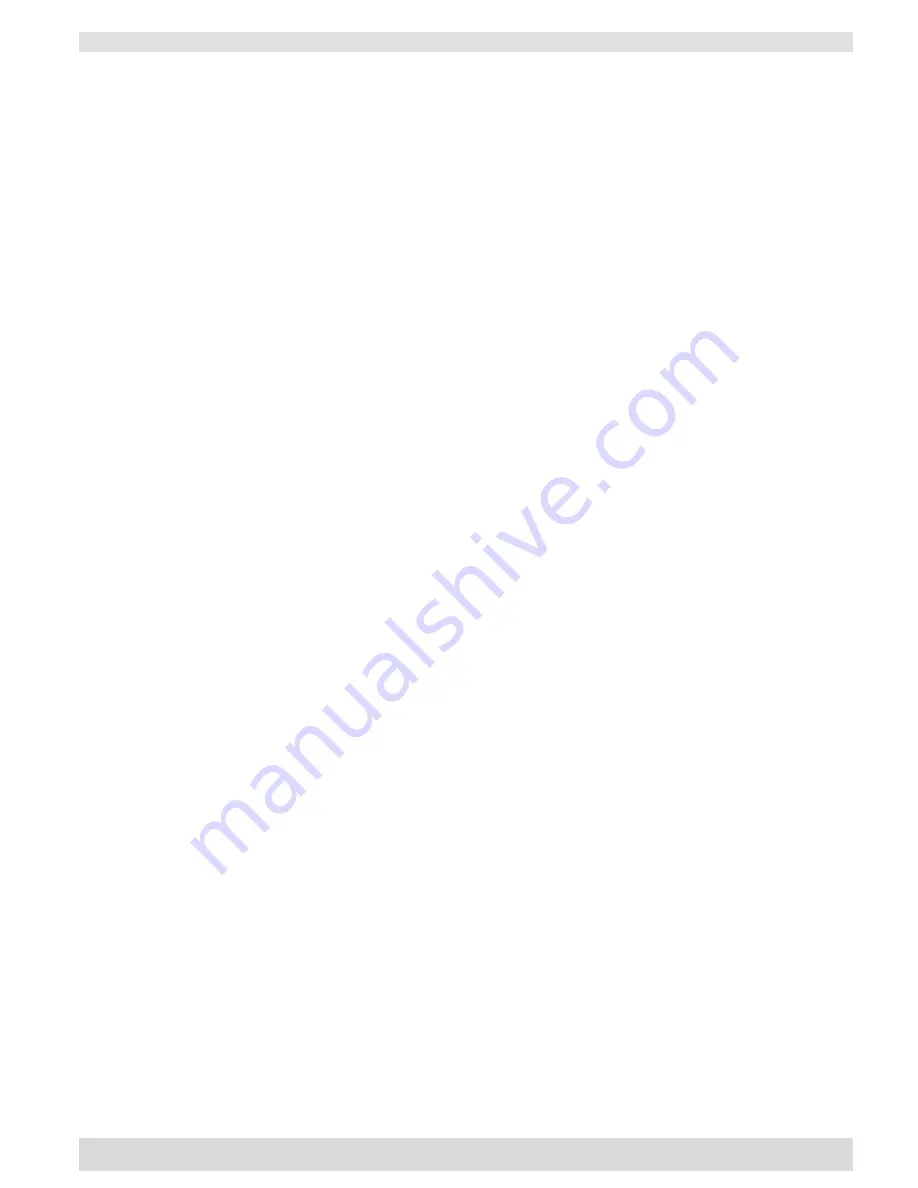
T
HERMO
C
UBE
200/300/400
T
HERMOELECTRIC
C
HILLER
M
ANUAL
52-11300-1
S
OLID
S
TATE
C
OOLING
S
YSTEMS
,
167
M
YERS
C
ORNERS
R
OAD
,
W
APPINGERS
F
ALLS
,
NY
12590
16
T
ELEPHONE
:
(845)
296-1300
F
AX
:
(845)
296-1303
WEB
:
WWW
.
SSCOOLING
.
COM
V
ERSION
M28
The following keystrokes initiate the auto-tune function:
1)
Press and hold the Enter key until the Status Menu changes to the
Temperature Input menu.
2)
Press and hold the Enter key again until the Temperature Input
menu changes to the Parameter Input menu.
3)
Press the Enter key three times. The display should read
AUTOTUNE off.
4)
Press the Up key to change off to on.
5)
Press and hold the Enter key until the parameter input menu
returns to the Status Display.
6)
Press the Start key once. The left most display character will
show the letter A until the auto tune is complete. The
ThermoCube will then begin controlling at the set point
temperature.
5.5
M
ANUAL
T
UNING
For users well versed in PID theory, Solid State Cooling Systems
recommends the closed-loop “Ziegler Nichols” method for manually
tuning the controller. The method consists of three steps:
1)
Turn off both the integral and derivative terms for heating and
cooling by setting I1, I2, D1, and D2 to zero.
2)
Set proportional band to 50 °C. Begin controlling the process at
the desired set-point temperature. Look for a small-sustained
oscillation in the coolant temperature. Observe the status menu
operating mode character and note if system is heating (+) or
cooling (-). If no oscillation occurs, lower the proportional band
in 50% increments until a small oscillation occurs. Write down
this proportional band setting (P)
3)
Measure the “Natural Frequency” (t) of the system in seconds.
This is the time required for the temperature oscillation to cycle
from one maximum temperature to the next maximum
temperature.
Now set the controller input parameters as follows:
P1 HEAT = 2*P if system was heating in step 2.
P1 HEAT = 4*P if system was cooling in step 2.
I1 HEAT = 1.2*t
D1 HEAT = t/8
P2 COOL = P if system was heating in step 2.
P2 COOL = 2*P if system was cooling in step 2.
I2 COOL = 1.2*t
D2 COOL = t/8