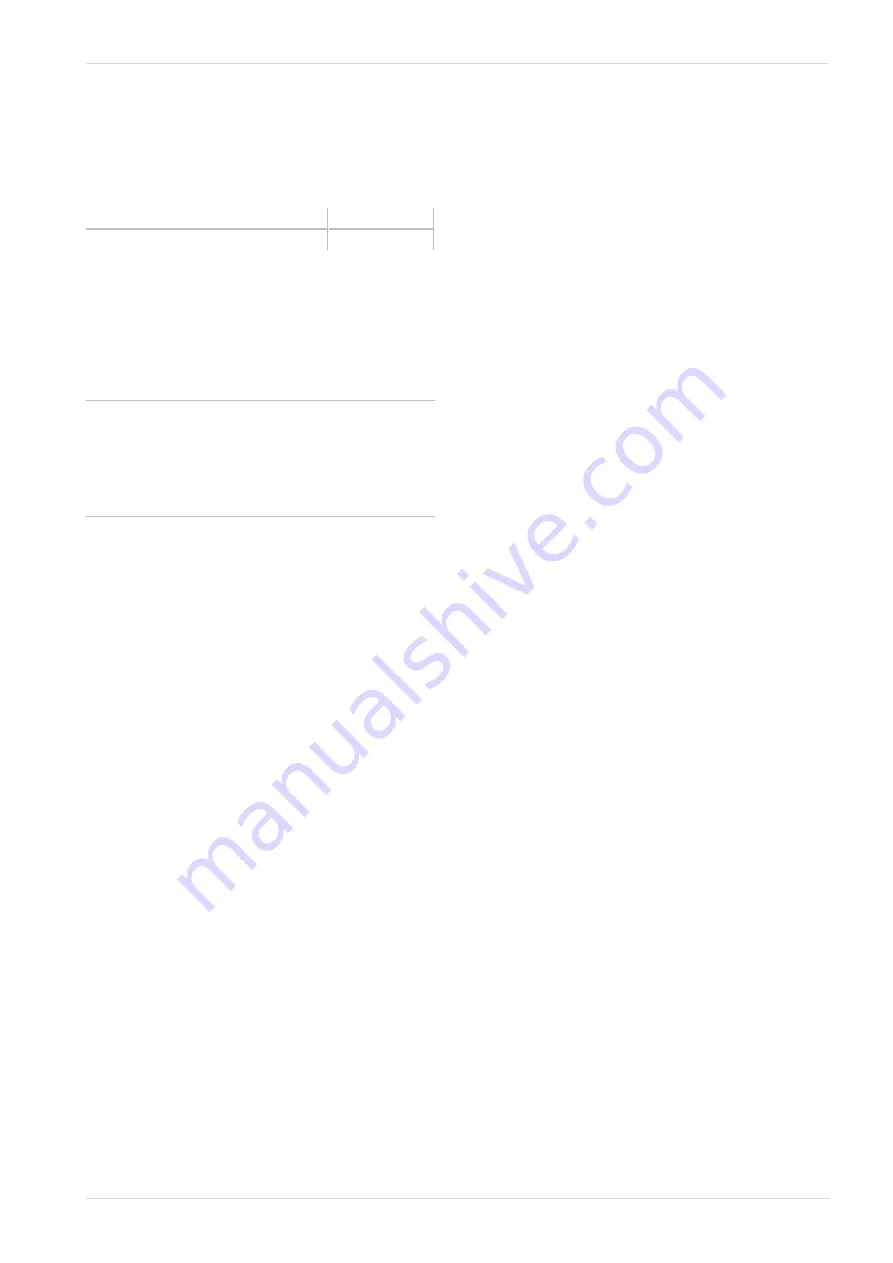
3 Technical requirements
Electrical conductivity
The probability of corrosion usually decreases with
decreasing electrical conductivity of the heating
water.
Low salt operation - filling with demineralised
water
, see VDI 2035 sheet 2.
Low salt
Electrical conductivity at 25°C
< 100 µS/cm
In the case of low-salt operation, feeding with non-
demineralised water can have a significant effect on
the pH value and push it into a critical range.
►
Check the pH value regularly.
3.7 Intermediate storage
i
If installation of the heating system is not star-
ted immediately after taking delivery of the
components, make sure that the components
are stored safely in a dry area with protection
against dust, contamination and mechanical
damage.
3.8 Information about the hydraulic
connection
Return flow boosting (RFB)
–
Functioning: If cold heating water (temperature <
55°C) flows from the heating circuit or the buffer
tank into the hot boiler, the steam contained in the
flue gas condenses on the "cool" boiler heat
exchanger surfaces. In the long term this leads to
corrosion and damage in the boiler. To avoid this,
hot water from the boiler flow is added to the
boiler return.
–
Return booster modules with a motor-controlled
mixer perform this task more accurately and
reliably than thermally controlled modules.
–
In addition, they allow the use of residual heat: If
the boiler temperature rises again after the burner
has stopped, then the charging pump starts, the
mixer opens, and the residual heat from the boiler
is transferred to the buffer tank.
Provide shut-off options in the lines
–
Position shut-off valves for each section (in buffer
tank, etc.) in order to minimise the quantity of
water that needs to be replaced in the event of
repairs or system extensions (see: preventing the
ingress of oxygen, heating system's fill-up/make-
up water
).
Pressure equalisation through expansion tank
–
The expansion tank prevents air from being
drawn in when the system cools down (issue: oxy-
gen input, heating system's fill-up water
–
Dimension the expansion tank with a capacity of
12% of the total hydraulic system volume.
–
Secure the expansion tank against shut-off. To do
this, either use the shut-off options on the way to
the expansion tank as cap valves, or unscrew the
hand lever (handwheel) and attach it to the expan-
sion tank with the wire in a clearly visible position.
–
Installation of an expansion tank or a pressure
maintenance system is essential. Use of open
expansion tanks is not permitted.
–
The pressure in the heating system (can be
viewed on pressure gauge) and the set pre-pres-
sure in the expansion tank must be checked regu-
larly.
Caution with (older) diffusion-open plastic pipes,
e.g. existing underfloor heating
–
In the case of older underfloor heating, the dif-
fusion-open plastic pipes can result in increased
oxygen input in the heating system. This has a cor-
rosion-inducing effect on the heating system com-
ponents (see: Avoiding water-side corrosion
).
–
In this case, the system must be separated
(through installation of a heat exchanger).
–
Newer plastic pipes (since around the mid 1980s)
are diffusion resistant in line with DIN 4726.
Buffer tank: Use, dimensioning
Advantages of using a buffer tank:
–
The boiler can always be operated in the optimum
load range. This results in a longer boiler service
life and reduces emissions.
–
Avoids unnecessary boiler start phases, the hig-
her fuel consumption during the start phases is
significantly reduced.
–
Continuously heated water is available in the buf-
fer tank for the heating circuit. The heating circuits
can therefore always be quickly supplied with
heat at all times.
If the heating system is operated without a buffer
tank, a hydraulic switch
must be installed.
Dimensioning the buffer tank:
–
For pellet boilers, a buffer tank volume of at 30
litres per kW heating output is recommended.
–
For wood chip boilers, a buffer tank volume of at
35 litres per kW heating output is recommended.
Installation manual
maximus L
9
Содержание maximus L 150
Страница 16: ...Front Abb 2 10 Side view Abb 2 11 3 Technical requirements 16 Installation manual maximus L ...
Страница 44: ...11 Annex 11 1 Mounting boiler covers overview Abb 2 72 Abb 2 73 11 Annex 44 Installation manual maximus L ...
Страница 50: ...11 Annex 50 Installation manual maximus L ...
Страница 51: ...11 Annex Installation manual maximus L 51 ...