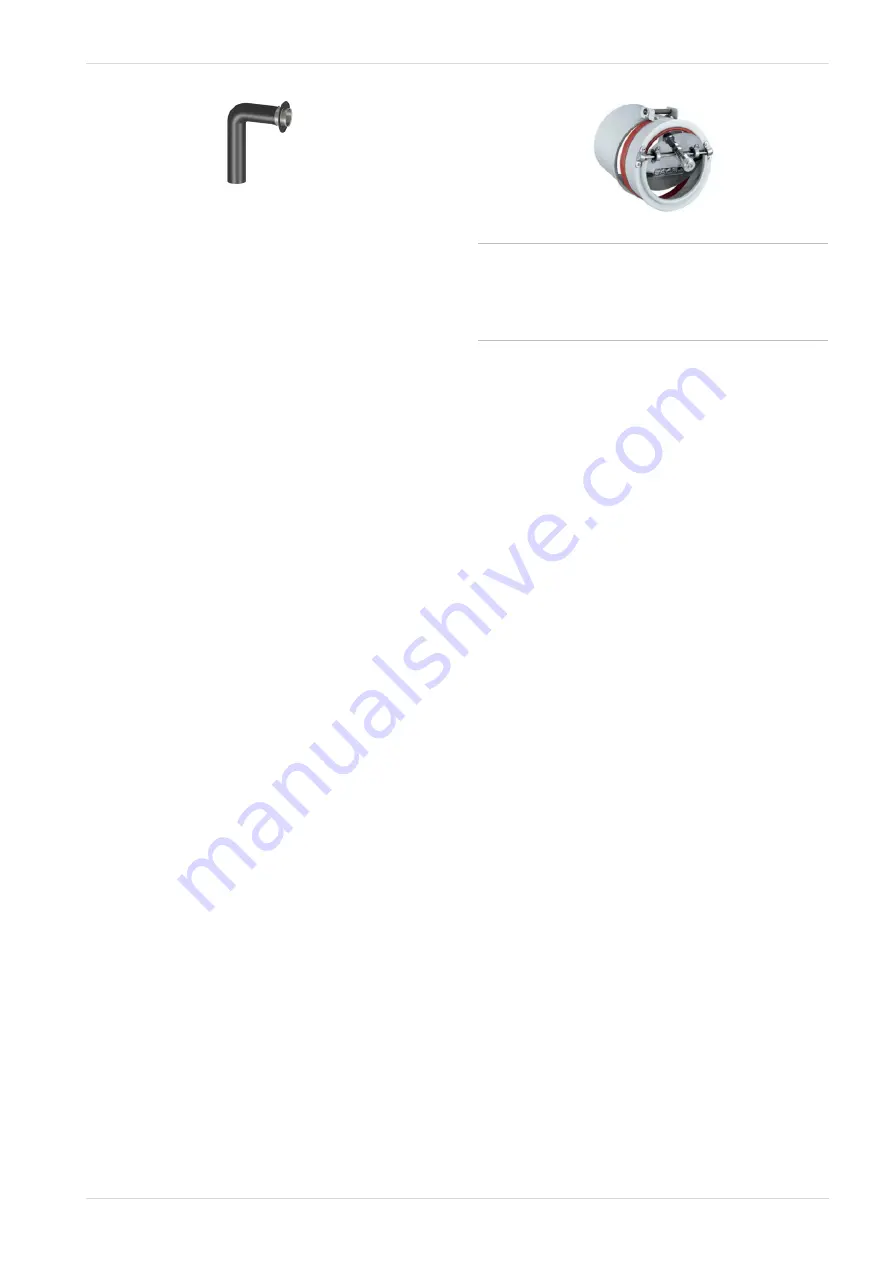
5 Prior to assembly
Execution of the flue gas pipe
–
Run the flue gas pipe towards the chimney in
a short and rising direction, with as few chan-
ges of direction as possible.
–
Change direction in the form of aerodynamically
favourable arcs, do not build kinks.
–
The diameter of the flue gas pipe to the chimney
may be enlarged if required, but may not be redu-
ced.
–
Place the inlet of the flue gas pipe in the chimney
just below the ceiling.
–
The flue gas pipe must be tight. Seal seal-less flue
gas pipes on site with heat-resistant silicone.
Insulate flue gas pipe
–
Insulate the flue gas pipe continuously from the boi-
ler to the chimney.
–
Recommended insulation thickness: 50 mm rock-
wool.
–
Serves to prevent temperature loss and prevents
the consequential formation of condensation.
Cleaning opening in the flue gas pipe
–
To clean the flue gas pipe (e.g. removal of accu-
mulated fly ash) there must be an easily acces-
sible cleaning opening.
–
Recommendation: Coordinate the number and pla-
cement of the cleaning openings with the chimney
sweep.
Opening for emissions measurement in the flue
gas pipe
Make an opening (hole) in the flue gas pipe to perform
the prescribed emission measurement
Minimum draught requirement for boiler: 5 Pa
A draught stabiliser must be fitted if the specified
draught of 15 Pa is exceeded.
►
Establish the chimney connection
Recommended chimney diameter
For all
maxi
mus
Boilers (150 to 300 kW output), a chim-
ney diameter of 25 cm is recommended.
Install explosion damper
Fig. 2-10: Explosion damper integrated into draught limiter
i
Before longer horizontal pipe sections
(L>20xD) and at the high point before dropping
down the flue gas pipe, an explosion damper
must be installed, independent of the boiler out-
put.
From 100 kW boiler output, an explosion damper is
required in the flue gas pipe. This avoids damage to
the boiler or the flue gas system even when defla-
grations occur.
Operation manual
maximus
15