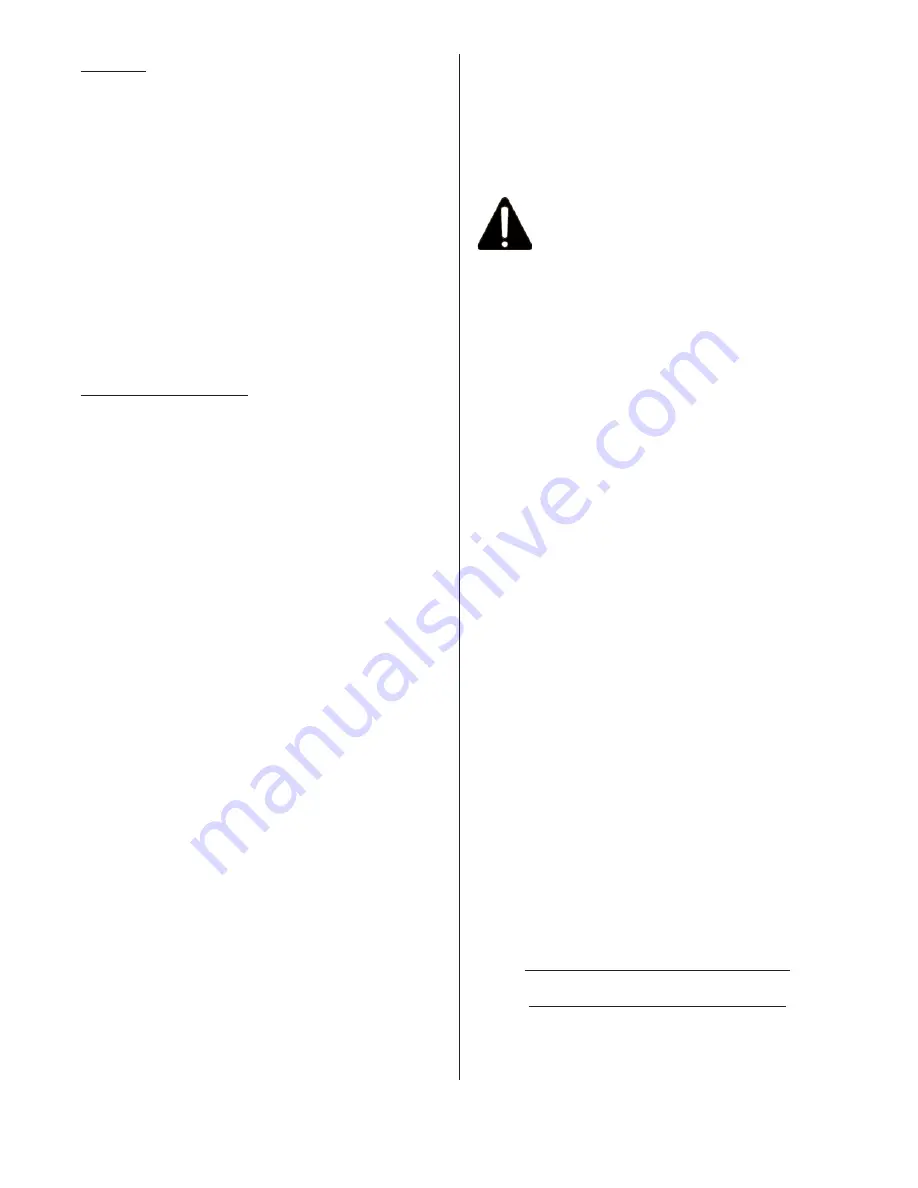
17
In the event of the failure of any
part of this equipment, contact
your Snap-On Tools representative
for replacement parts and service.
When ordering parts from Snap-On
Tools Corporation, order numbers
should be preceded by "CKS".
WARNING
•
DO NOT lift the unit when a gas
cylinder is installed or at-
tached.
•
DO NOT weld on any item that has
a common electrical ground.
•
DO NOT operate the unit with the
side panels removed. Overheat-
ing will occur.
•
DO NOT weld upon the case of the
welding machine.
•
ONLY a qualified electrician
should perform work inside the
welding machine.
•
ALWAYS wear protective cloth-
ing, leather gloves and a full
cover welding hood while weld-
ing.
•
DO NOT weld in a closed in area.
Proper ventilation is a neces-
sity, or a fresh air supplied
hood should be worn.
•
WHEN welding near combustibles,
a helper or "watcher" should
stand by with a fire extin-
guisher or other fire protective
device.
•
NEVER weld on a closed vessel or
one that has contained com-
bustibles.
IF IN DOUBT - DON’T DO IT!
BE SAFE - DON’T BE SORRY!
WEEKLY
1. Remove dirt and dust from the
wire feed compartment. Use low
pressure dry compressed air.
2. Remove dirt and metal deposits
from the grooves in the feed
roll. If the grooves are badly
worn, the feed roll should be
replaced. If the pressure roll
does not turn freely, it should
be replaced.
3. Check all gas fittings for
leaks. Tighten or repair as
required.
EVERY SIX MONTHS
1. Disconnect the welder from its
main power supply.
2. Remove the machine’s side pan-
els.
3. Using low pressure dry com-
pressed air, remove dust and
dirt from all components.
4. Check for loose or frayed wir-
ing. Particularly check welding
current wire connections.
5. Replace torch liner if neces-
sary.
RECOMMENDED
CUSTOMER SPARE PARTS
The Snap-on Tools MM350XL is a
machine of proven design and relia-
bility. Following is a list of
consumable items recommended as
spare parts for this unit.
contact tips ....... M3-T30, etc.
gas nozzles .............. M6-C62
nozzle insulators .......... M6-B
gas diffusers .............. M6-D
steel liner(.020-.030) .. M123L-B
steel liner(.035-.045) .. M124L-N
steel liner(.062) ....... M126L-G
drive roll (.020-.035) .. 20-35DR
drive roll (.045-5/64) . 45-564DR