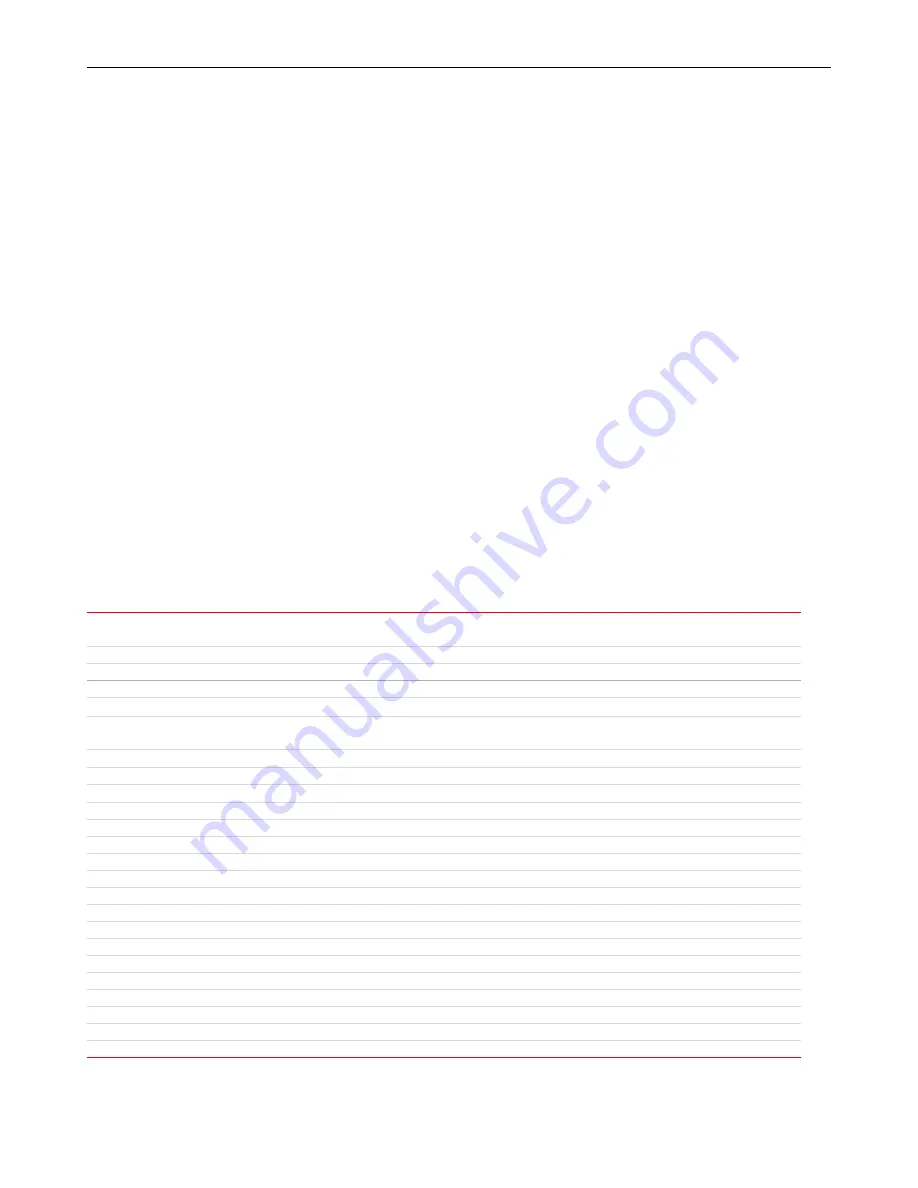
13.0 Technical Specifications
Specifications
180 Multiprocess
Part No.
BOC180MULTI
Input voltage
Single phase 240 V ±15 %
Frequency
50/60 Hz
MIG
TIG
MMA
Maximum rated input current (
I
1max
)
31.2 A
24 A
31.1 A
Maximum effective supply current (
I
1eff
)
14 A
12 A
13.9 A
No-load voltage
63 V
Output current
32 – 180 A
10 – 180 A
10 – 160 A
Duty cycle
20 %
180 A
–
160 A
25 %
–
180 A
–
Wire feeder
Internal or optional spool gun (sold separately)
Internal wire feeder speed
3 to 11 m/min
Post flow time
3 Seconds
Welding wire diameter
0.8/1.0 mm
Remote control
No
Efficiency
80 %
Power factor
0.73
Insulation grade
H
Housing shielding grade
IP21S
EMG grade
B
Welding thickness
>0.8 mm
Dimensions (L × W × H )
420 × 220 × 439 mm
Weight
12.8 kg
Standards
AS/NZS 60974-1, IEC/EN 60974-10
51
BOC Smootharc 180 Multiprocess operating manual
Содержание 180 Multiprocess
Страница 1: ...180 Multiprocess Operating manual 6PRRWKDUF GYDQF GYDQF ...
Страница 45: ...45 BOC Smootharc 180 Multiprocess operating manual ...
Страница 53: ......
Страница 54: ......
Страница 55: ......