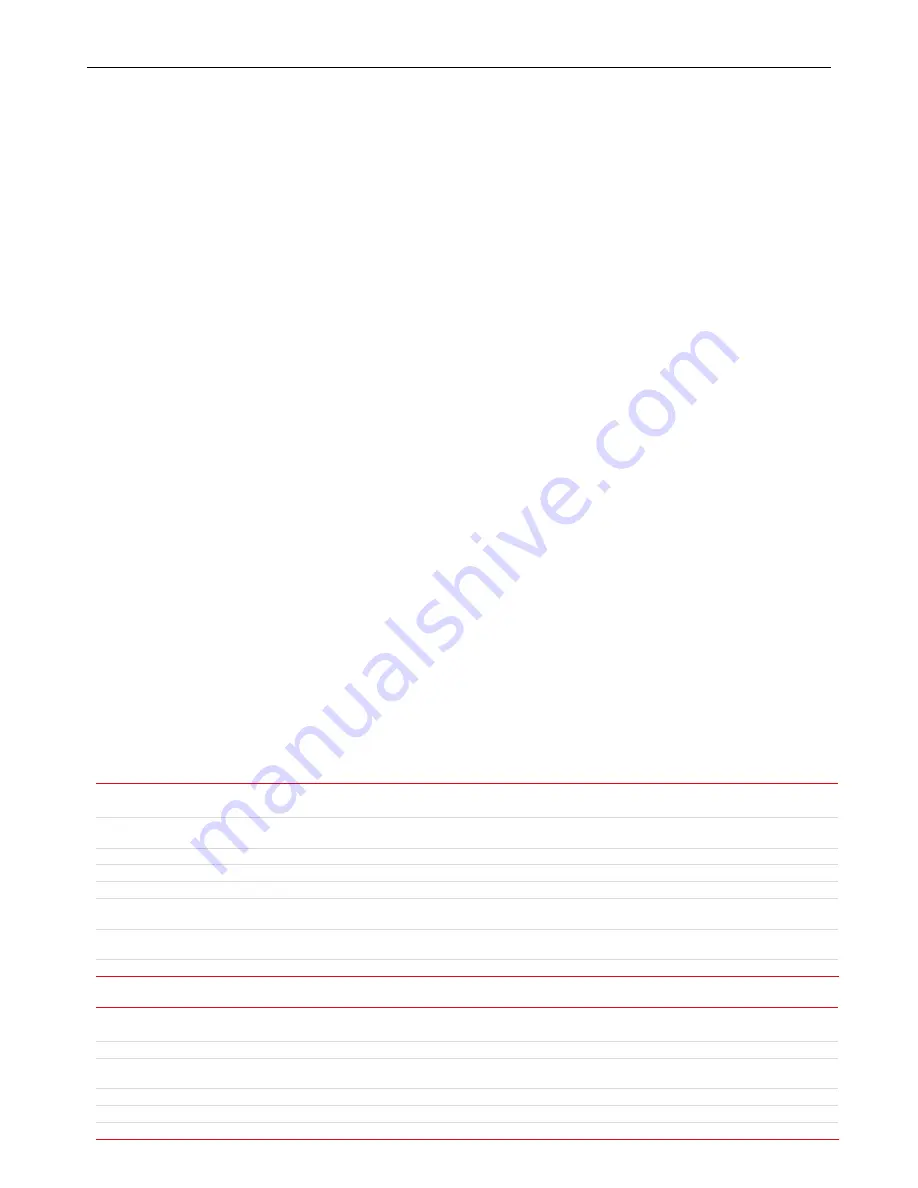
Porosity in Weld Deposit
Cause
Solution
Entrapped impurities, hydrogen, air, nitrogen, water
vapour
Do not weld on wet material.
Defective gas hose or loose connection
Check hoses and connections for leaks
Filler material is damp (particularly aluminium)
Dry filler metal in oven prior to welding
Filler material is oily or dusty
Replace filler metal
Alloy impurities in the base metal such as sulphur,
phosphorous, lead and zinc
Change to a different alloy composition which is weldable. These impurities can cause a
tendency to crack when hot
Excessive travel speed with rapid freezing of weld trapping
gases before they escape
Lower travel speed
Contaminated shield gas
Replace the shielding gas
Inadequate shielding
Cause
Solution
Gas flow blockage or leak in hoses or torch
Locate and eliminate the blockage or leak
Excessive travel speed exposes molten weld to
atmospheric contamination
Use slower travel speed or carefully increase the flow rate to a safe level without creating
excessive turbulence. Use a trailing shield cup
Wind or drafts
Set up screens around the weld area
Excessive electrode stickout
Reduce electrode stickout. Use a larger size nozzle
Excessive turbulence in gas stream
Change to gas saver parts or gas lens, lower flow rate if possible
49
BOC Smootharc 180 Multiprocess operating manual
Содержание 180 Multiprocess
Страница 1: ...180 Multiprocess Operating manual 6PRRWKDUF GYDQF GYDQF ...
Страница 45: ...45 BOC Smootharc 180 Multiprocess operating manual ...
Страница 53: ......
Страница 54: ......
Страница 55: ......