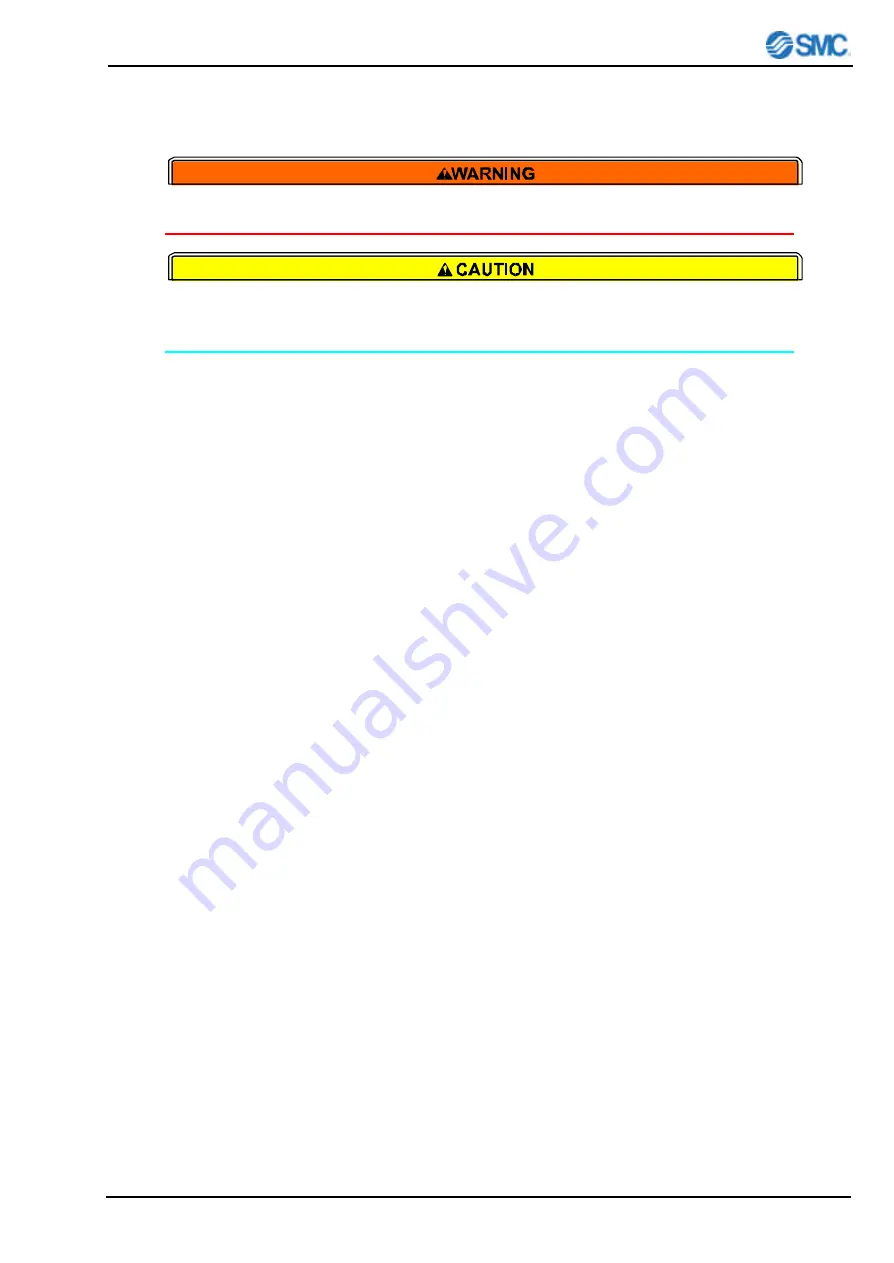
Caution on Installation
06/18/04
3-1
3 Caution on Installation
Pay special attention to keep safety of human body during installation
and transportation of the unit.
Only the trained person with knowledge and experience can perform the
possibly dangerous work associated with installation, transportation and
maintenance.
3.1 Environment
The Thermo-con shall be installed on the following environments.
1) The place without exposure to water, oil or any chemical spills, and particles are few.
2) The place, which allows the Thermo-con to become stable horizontally.
3) The place, which doesn’t interfere the suction and discharge port, required for forced air-cooled
refrigerant via fan.
4) The place without exposure to corrosive or flammable gas. (The unit is not explosion proof.)
5) The place with ambient temp. range of 10 to 40deg.C and humidity range of 10 to 80% and without
large temp. change. No dew condensation is allowed on the unit. The detail of due condensation is
shown on “10.2 Calculation of Dew Point”.
6) The place without effect from noise source (such as discharging equipment, large relay and thyristor).
7) The place with enough space between power supply cable or communication cable of the Thermo-con
and power line of other equipments.
8) The place without strong electrical or magnetic emission.
9) The place, which allows power supply, ground to be made properly.
10) The place free from the material such as silicone, which may generate harmful gas.
11) Though this unit corresponds to CISPR11(EMI), the switching power supply might malfunction when
used under the environment which undertakes the electric field, the magnetic field, and the electric
wave and it break down.