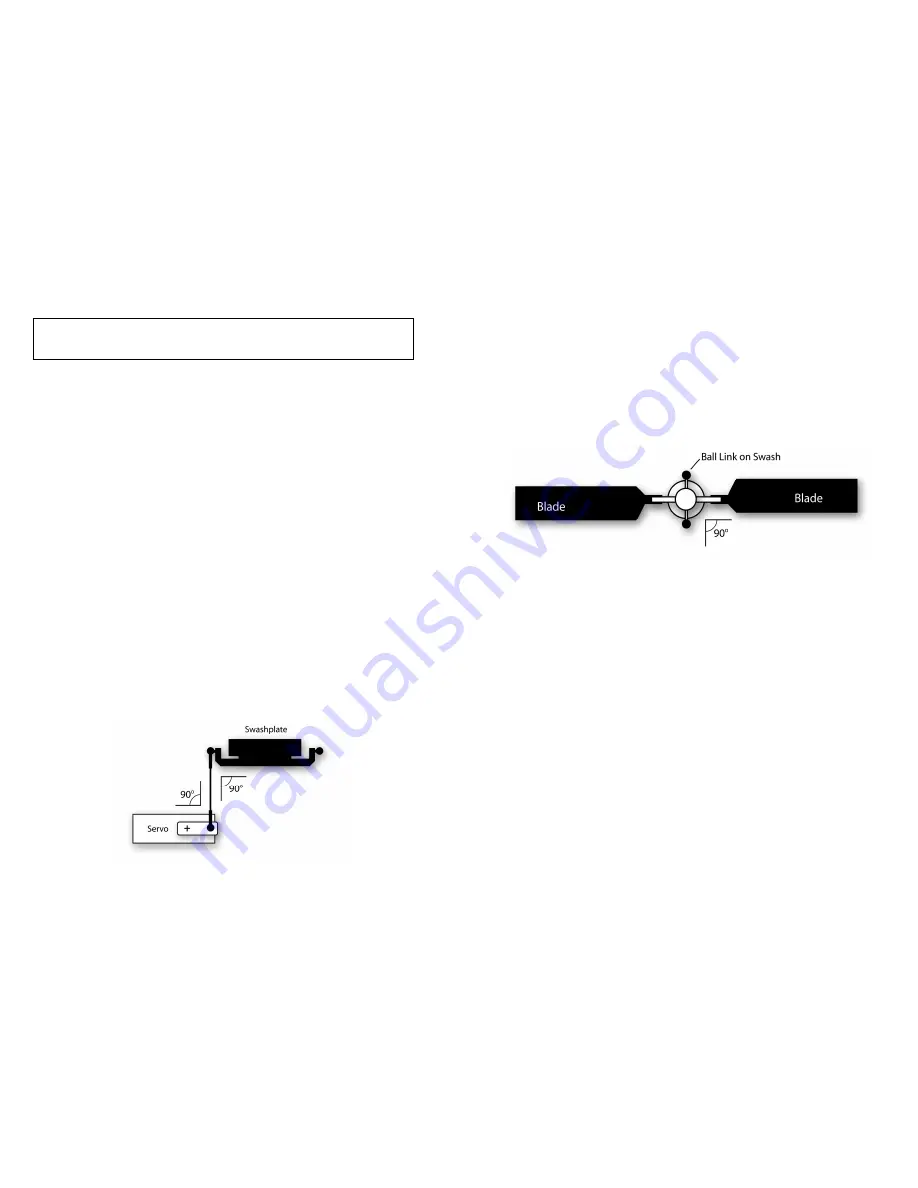
©2010 Skookum Robotics, Ltd
11
7
Helicopter Airframe Setup
WARNING:
Good mechanical setup is critical to the gyro performing
correctly. Please read this section fully.
CAUTION: The gyro should not be used in addition to a flybar as the results
could be unpredictable. It is intended for use where the swashplate alone
drives blade pitch.
CAUTION: Do not connect the swashplate or tail servos to the gyro until
after the SK720 has been configured for your servos. Your servos could be
damaged by an incorrect configuration. See Section 10 of this manual for
information about how to configure the SK720.
Main Rotor Blades:
Normal symmetrical rotor blades are recommended.
Flat-bottomed rotor blades
may be used but they have a nose-down moment about their pitch axis and so
require powerful swash plate servos. The ideal rotor blades will be torsionally
stiff but a bit flexible spanwise. Rotor blades must also be balanced both
spanwise and chordwise. Heavier blades will make it easier to tune the helicopter.
Servos:
The best performance will be achieved if the servo’s full normal range of
movement is used. You will need fast (and ideally digital) servos for good “3D”
performance. Stronger, faster servos will let you use higher damping gains (see
Section 19.1) which is important for maneuvers such as piro-flips and tic-tocks.
Be aware that the current draw on your cyclic servos will be higher than
with a flybar.
Try to have 90-degree angles between the servo arms, linkages, swashplate and
blade grip arms at zero degrees pitch ('mid stick') to ensure even movement. The
gyro’s USB setup interface will allow fine-tuning of servo centers to achieve this.
©2010 Skookum Robotics, Ltd
12
Rotorhead:
Removing the flybar while retaining normal servo arm length will likely give too
much blade pitch action when setting up a rotorhead mechanism originally
designed for helicopters with a flybar. Either servo travel or servo arm length will
also need to be reduced to allow normal gains and good performance. (See
Section 12 of this manual for a detailed description of how to check for correct
cyclic and collective pitch setup.)
Some kind of anti-rotation or “follower” mechanism will be needed to keep the
top of the swashplate from rotating relative to the blade grips. If the swashplate is
not held so the linkage to the blade grips is at 90 degrees to the blades (for 2-
bladed rotors), the phase angle will need to be adjusted. See the diagram below:
For initial flights, the phase angle should be adjusted so that when the blades are
lined up with the helicopter’s tail boom, they do not move with elevator input but
do move with aileron input (for 2-bladed rotors). This can be set either
mechanically or through the setup software.
It is important that the linkages and swash have minimal backlash and the lowest
friction possible. The stiffness of the rubber rotorhead dampers also affects
SK720 gyro tuning and flight performance. Performance will be better with the
teeter damping stiffer than normal, but excessive stiffness can cause vibration
that is hard on the airframe, gyros and servos.
Tail:
It is important that you minimize tail rotor vibration. Tail rotor vibrations affect
the helicopter’s elevator control because the axis of rotation of the tail rotor disk
is aligned with the elevator axis. Also, if you have a belt-driven tail, be sure that
your tail boom is electrically grounded to the heli’s frame or motor case to
prevent static electricity buildup.
Balance:
The gyro will perform best when the helicopter’s centre of gravity (CG) is
located directly under the mainshaft or very slightly forward (i.e. very slightly
nose heavy). This is especially important for maneuvers that use fast collective
pitch changes combined with yaw (i.e. piros).