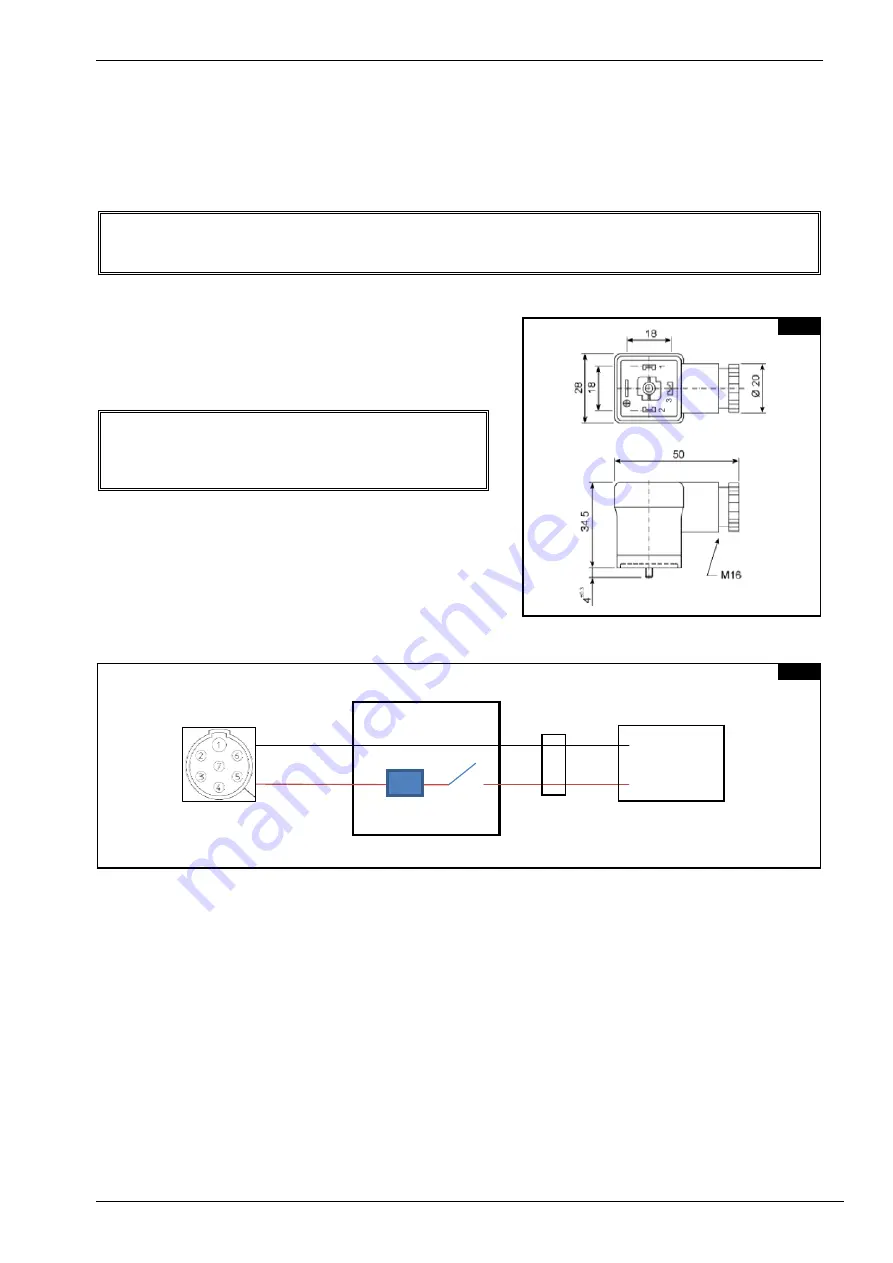
39
The LED light will be damaged if the connections
of the cables at the terminals of the connector are
accidentally reversed (see diagram Fig.5.5)
5.3.1
FUSE AND ELECTRICAL DIAGRAM
The fuse is located on one side of the control box and can be accessed by unscrewing the protective cap.
Before replacing the fuse, check with expert personnel that there are no short circuit contacts in
the electrical circuit in Figure 5.5.
The cable for the solenoid valve has a connector with an
LED light that turns on when current is passing through
(Fig.5.4).
If the LED light on the solenoid connector does not turn on:
1) check that there is power at the tractor plug.
2) check that the fuse is good
3) the LED light is damaged
5.4
5.5
PIN 1 GND
PIN 7 POWER SUPPLY
FUSE 5A
SWITCH
PIN 1 DIN CONNECTOR
PIN 2 DIN CONNECTOR
TRACTOR PLUG
CONTROL BOX
PLUG
VALVE CONNECTOR
Содержание QRX 12
Страница 1: ...ASSEMBLY USE AND MAINTENANCE QRX 12 14 201600 ...
Страница 2: ......