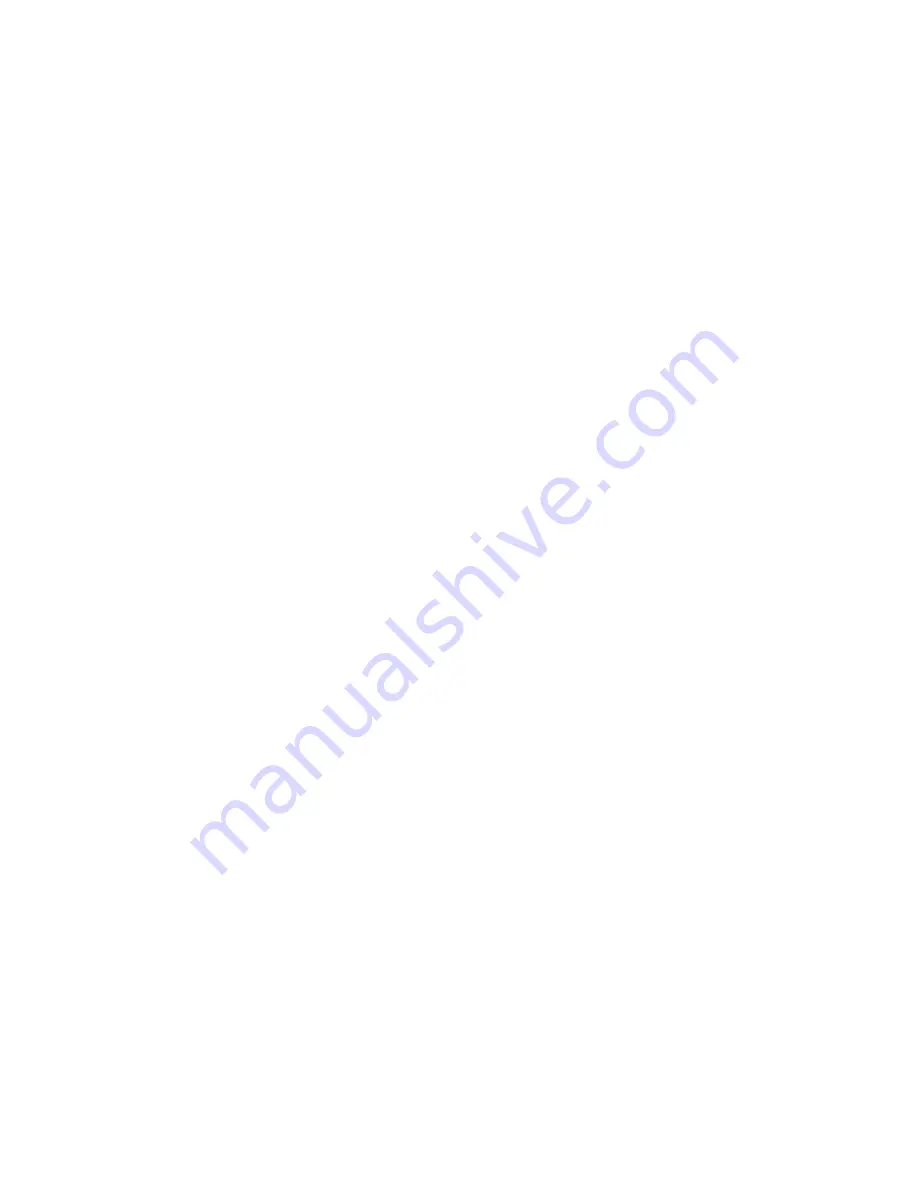
24
AIR MOTOR 18R36, DISASSEMBLY & REASSEMBLY
Considerable care must be used when an air motor is disassembled. Lack of lubrication and dirty
unfiltered air are the main causes of malfunctions, which are corrected by proper maintenance of
the filter, regulator and lubricator unit. Review Pneumatic Information in this manual for
installation and maintenance recommendations.
REGULATOR DISASSEMBLY:
1.
Remove the motor pressure regulator parts, clean and replace if necessary.
2.
Reassemble and test tool before proceeding with the Motor Disassembly.
MOTOR DISASSEMBLY:
1.
Loosen cap screw (13). Loosen ring nut (20) and remove motor from tool gear housing.
2.
Hold motor housing (28) lightly in a vise, and remove gear housing (29) by rotating counter-
clockwise when facing gearing end.
3.
Keep groups of parts together without separating bearings unless their replacement is
necessary.
4.
Wash out any dirty parts using a fresh clean oil base type solvent.
5.
Rotate bearings to make certain parts are clean. Apply a light coating of grease, #K-55, non-
fluid oil, or an equivalent light cup grease. Do not apply grease on rotor (27) since this will
cause sticking of vanes (22). Do not grease bearing (3) located in back end plate (21).
Lubricate rotor, vanes and end bearing with air line oil only.
6.
Replace gearing (18, 24, 27) and vanes (22) if worn or cracked. Apply a light coating of grease
to gearing and air line oil to rotor and vanes.
REASSEMBLY:
1.
Begin reassembly by making certain that the alignment pin (5) is correctly positioned to align
the back-end plate (21), the cylinder (26) and the front-end plate (25) with the hole in the motor
housing (28).
2.
Assemble parts (8, 11, 12, 14, 18, 19, 24) and place them in the gear housing (29). Make certain
that the roll pin (12) enters into the slot of the ring gear (19).
3.
Assemble the gear housing (29) and the ring nut (20) to the motor housing (28). Hand tighten.
Rotate the pinion of the gear case (24) by hand in the clockwise direction to be certain all parts
are free. If parts are not free, gears are not properly meshed.
4.
Add one teaspoon or squirt air line lubricating oil into the motor. Connect the air hose with
the pressure set at approximately 20 p.s.i.g. With motor housing in vise, slowly tighten gear
housing in a clockwise direction while the motor is rotating. Tighten the motor, noting an
increase in speed. The correct adjustment is about 400-600 inch lbs. If the motor is over
tightened it will slow down. When set, attach the air motor to the gear housing.
Содержание AMPT-12
Страница 1: ...SIGNODE 3620 WEST LAKE AVENUE GLENVIEW ILLINOIS 60025 AMPT 12 POWERED COMBINATION STRAPPING TOOL...
Страница 14: ...14 Apply one drop of Loctite 242 Sealant to cleaned parts Allow 12 hours to set if possible Use Loctite 609...
Страница 15: ...15...
Страница 16: ...16 Apply one drop of Loctite 242 Sealant to cleaned parts Allow 12 hours to set if possible...
Страница 21: ...21...