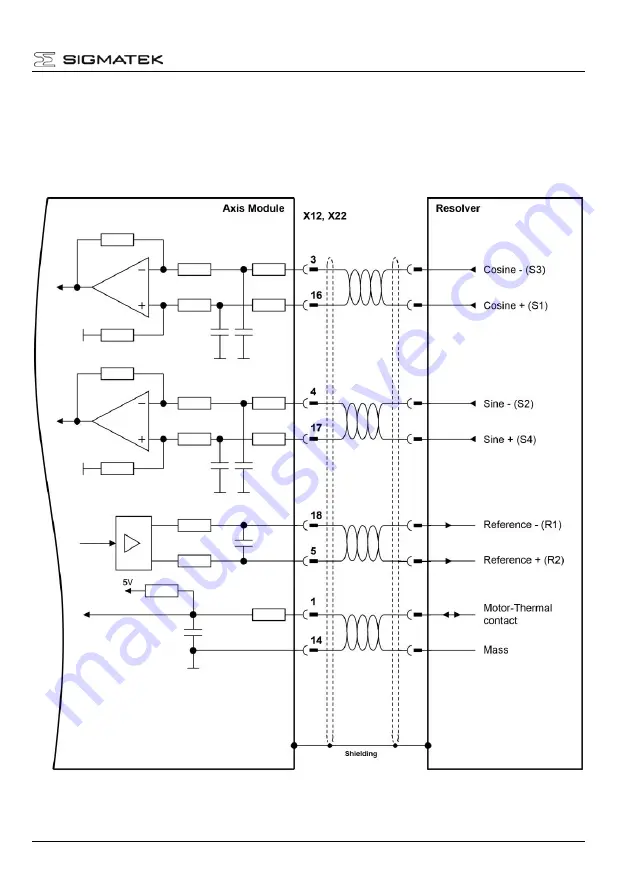
MDP 102-1
29.08.2019
Page 59
5.5.1 Resolver Feedback
The standard feedback system for servomotors is resolver feedback. The servo drive allows
evaluation of single speed (2-pole) and also multi speed resolvers (up to 32-pole). The
maximum cable length is limited to 50 m.
If a thermal contact is used in the motor, the signal is also connected via the resolver cable.
Содержание MDD 111-1
Страница 4: ...MDP 102 1 Page 4 29 08 2019 1 1 Components of a servo system...
Страница 13: ...MDP 102 1 29 08 2019 Page 13 2 6 Nameplate...
Страница 14: ...MDP 102 1 Page 14 29 08 2019 2 7 Block Diagram and Concept Block diagram of the Power Supply Module...
Страница 27: ...MDP 102 1 29 08 2019 Page 27...
Страница 28: ...MDP 102 1 Page 28 29 08 2019 Connector layout of X1 X2 X3 X4 and X6...
Страница 30: ...MDP 102 1 Page 30 29 08 2019 The entire MDD System is grounded over the module carrier in the control cabinet...
Страница 48: ...MDP 102 1 Page 48 29 08 2019...
Страница 50: ...MDP 102 1 Page 50 29 08 2019...
Страница 84: ...MDP 102 1 Page 84 29 08 2019...