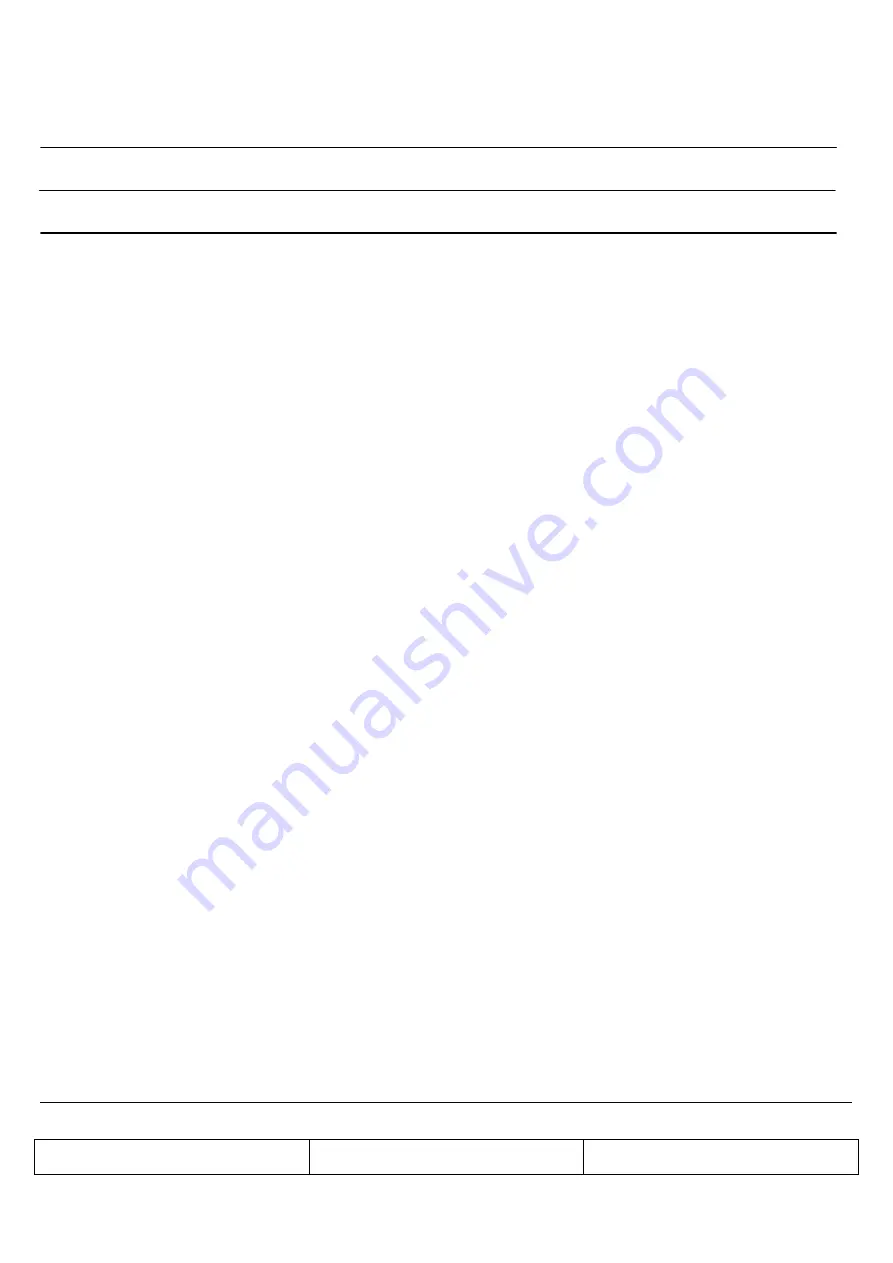
CONTROLLED COPY
Centre for Biological Engineering
Standard Operating Procedure
SOP122
Title: Use and Maintenance of Sigma Refrigerated Centrifuge 3-16PK
Location:
CBE Laboratory Unit (H21/22)
Version 003
Effective Date: 26
th
June 2018
Review 26
th
June 2020
Written by: Victoria Workman
Reviewed by: P.Hourd
Approved by: R/I.Temple
Page 19 of 22
B.1.6.3 Avoid moving defective and damaged components, unless it is necessary for
decontamination of hazardous materials, and in any event retain all components and debris
for inspection by the manufacturer's representative.
B.1.6.4 Note all the details of the incident and any measures subsequently taken and inform the
relevant authority of the laboratory.
B.1.6.5 Do not use the centrifuge or the rotation assembly again until the necessary repairs and
replacements have been completed and the manufacturer's representative has given an
assurance that its safety is not impaired.’ The Appendix of BS 4402 goes on to deal with
extra precautions required when centrifuging hazardous materials (see below).
Rotors
It is essential that rotors are properly handled, used and maintained.
An ultracentrifuge rotor, for example, experiences 600,000 times the force of gravity. Each gram of it will
effectively weigh over 600kg. Under these conditions a small flaw in part of it may lead to failure and the
virtual explosion of the rotor within the centrifuge.
The centrifugal forces cause rotors to stretch. At low and normal speeds the change of size is elastic and
the rotor returns to its original size when stationary. At high or over speeds the elastic limit of the material
may be exceeded and plastic deformation occurs. If this process recurs micro cracks may be formed and
grow at high stress points within the rotor and subsequently cause catastrophic failure.
Corrosion of the rotor by moisture or chemicals greatly reduces the level of stress at which micro cracks
form and grow. This increases the probability of early failure (by corrosion fatigue or stress-corrosion
cracking). For these reasons it is essential to conform to the manufacturer's conditions on maximum rotor
speeds and maximum running times, and to follow closely their cleaning and maintenance procedures.
Useful advice on the care of rotors is given in the cited references. The publication Centrifuges by L.W.
Price, University of Cambridge, is particularly useful and contains the following list of some causes of rotor
failure.
1. Misplaced trunnions on MSE Minors
2. Use of wrong accessories e.g. with horizontal rotors. In a laboratory where several makes of centrifuge
are in use, it is possible to mix up accessories which are not interchangeable. Keep them separate.
3. Failure to reduce speed above sample specific gravity of 1.2.
4. Powdered glass in rotor.
5. Failure to use speed restriction curves to avoid recyrstallisation with CsC1 gradients.
6. Mis-hooked buckets on swinging bucket rotors.