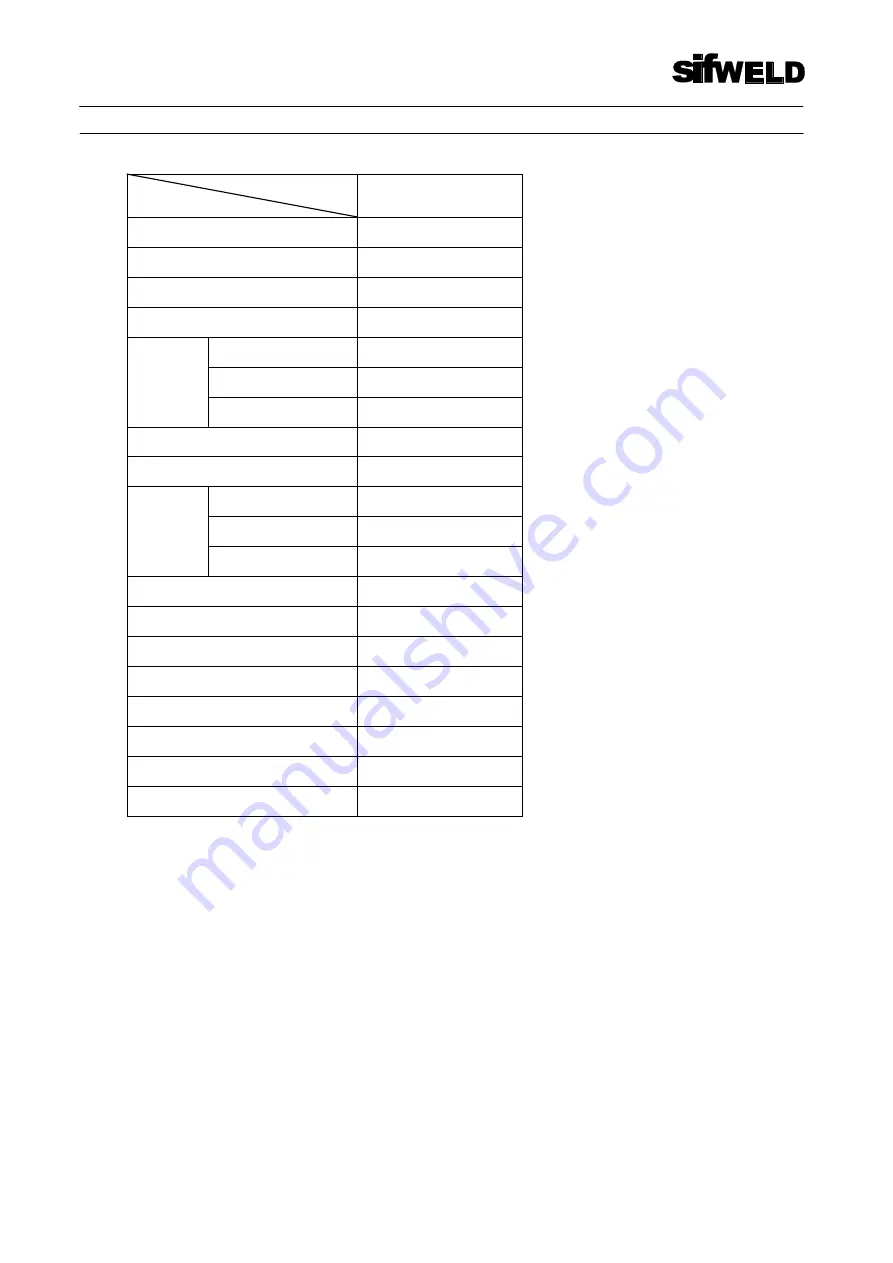
TSX1D200MTS V1 FEB13
- 6 -
3
Technical Data
Model
Item
SifWeld MTS200
Power Voltage (V)
1ph AC 230/240V
Frequency (Hz)
50/60
Rated Input Current (A) I-1max
40.6
Rated Input Current (A) I-1eff
20.3
MIG
5-200
TIG
5-200
Rated
Current
Range
(A)
MMA
30-200
Recommended Fuse Rating
32A
No Load Voltage
63
MIG
20.2-28
TIG
10.2-18
Output
Voltage
(V)
MMA
16.5-24
Duty Cycle (%) 40˚C 10min
25%
Efficiency
0.73
Wire Feed Speed (m/mm)
2.7-14.4
Wire Diameter (mm)
0.6/0.8/1.0
Protection Class
IP23S
Insulation Class
F
Weight (Kg)
15
Dimensions (mm)
439x214x405
Содержание MTS 200
Страница 1: ...MTS 200 User Manual SWMTS001 TSX1D200MTS ...
Страница 9: ...TSX1D200MTS V1 FEB13 9 Diagram for Installation for MIG Applications ...
Страница 12: ...TSX1D200MTS V1 FEB13 12 Diagram for Installation for Spool On Gun MIG Applications ...
Страница 14: ...TSX1D200MTS V1 FEB13 14 Diagram for Installation for TIG Applications ...
Страница 16: ...TSX1D200MTS V1 FEB13 16 Diagram for Installation for MMA Applications ...
Страница 22: ...TSX1D200MTS V1 FEB13 22 4 Hot Start ...
Страница 27: ...TSX1D200MTS V1 FEB13 27 8 Parts List Circuit Diagram Parts Diagram ...
Страница 29: ...TSX1D200MTS V1 FEB13 29 Circuit Diagram ...