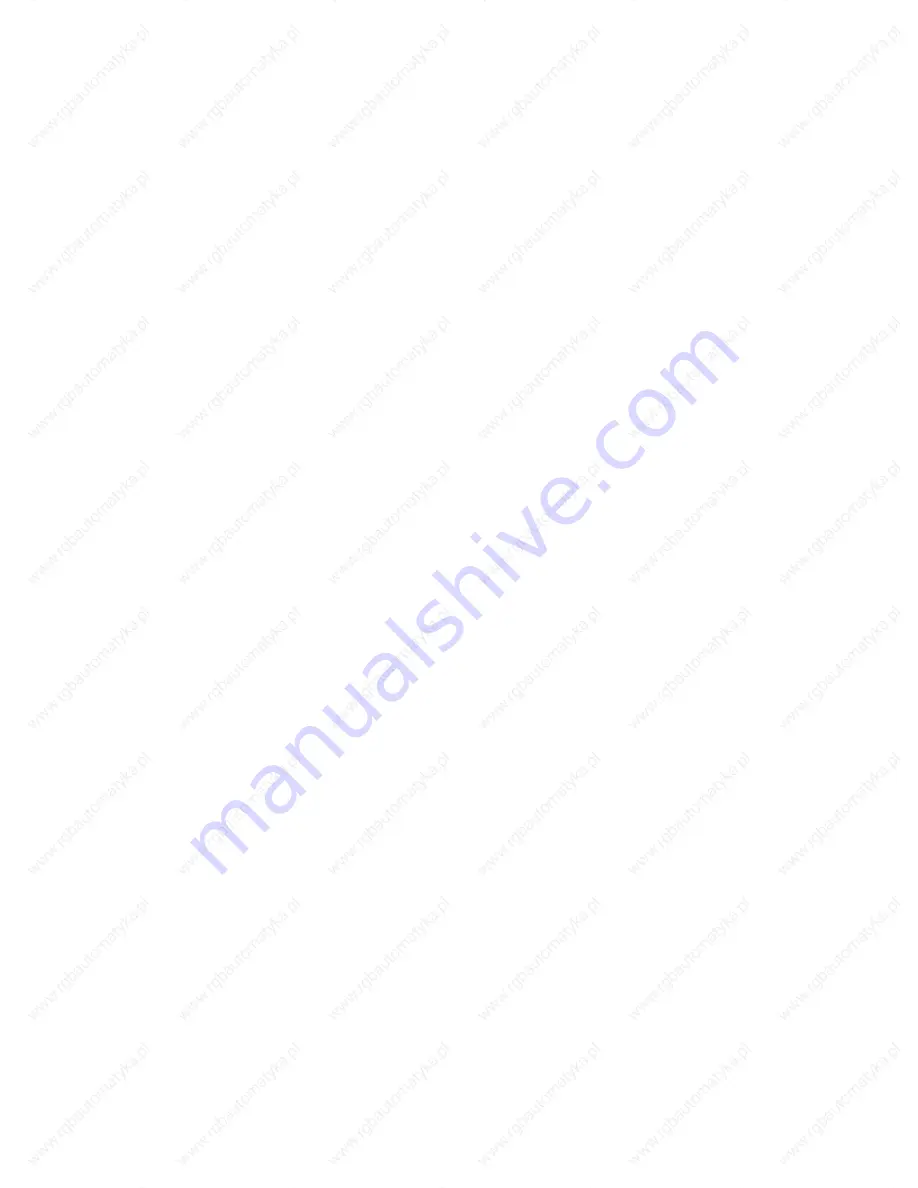
9 Axis/PLC Interface (DB 32)
01.93
9.3 Signals to axis
a a a a a a a a a a a a a a a a a a a a a a a a a a a a a a a a a a a a a a a a a a a a a a a a a a a a a a a a a a a a a a a a a a a a a a a a a a a a a a a a a a a a a a a a a a a a a a a a a a a a a a a a a a a a a a a a a
a a a a a a a a a a a a a a a a a a a a a a a a a a a a a a a a a a a a a a a a a a a a a a a a a a a a a a a a a a a a a a a a a a a a a a a a a a a a a a a a a a a a a a a a a a a a a a a a a a a a a a a a a a a a a a a a a
a a a a a a a a a a a a a a a a a a a a a a a a a a a a a a a a a a a a a a a a a a a a a a a a a a a a a a a a a a a a a a a a a a a a a a a a a a a a a a a a a a a a a a a a a a a a a a a a a a a a a a a a a a a a a a a a a
a a a a a a a a a a a a a a a a a a a a a a a a a a a a a a a a a a a a a a a a a a a a a a a a a a a a a a a a a a a a a a a a a a a a a a a a a a a a a a a a a a a a a a a a a a a a a a a a a a a a a a a a a a a a a a a a a
a a a a a a a a a a a a a a a a a a a a a a a a a a a a a a a a a a a a a a a a a a a a a a a a a a a a a a a a a a a a a a a a a a a a a a a a a a a a a a a a a a a a a a a a a a a a a a a a a a a a a a a a a a a a a a a a a
a a a a a a a a a a a a a a a a a a a a a a a a a a a a a a a a a a a a a a a a a a a a a a a a a a a a a a a a a a a a a a a a a a a a a a a a a a a a a a a a a a a a a a a a a a a a a a a a a a a a a a a a a a a a a a a a a
a a a a a a a a a a a a a a a a a a a a a a a a a a a a a a a a a a a a a a a a a a a a a a a a a a a a a a a a a a a a a a a a a a a a a a a a a a a a a a a a a a a a a a a a a a a a a a a a a a a a a a a a a a a a a a a a a
a a a a a a a a a a a a a a a a a a a a a a a a a a a a a a a a a a a a a a a a a a a a a a a a a a a a a a a a a a a a a a a a a a a a a a a a a a a a a a a a a a a a a a a a a a a a a a a a a a a a a a a a a a a a a a a a a
a a a a a a a a a a a a a a a a a a a a a a a a a a a a a a a a a a a a a a a a a a a a a a a a a a a a a a a a a a a a a a a a a a a a a a a a a a a a a a a a a a a a a a a a a a a a a a a a a a a a a a a a a a a a a a a a a
FOLLOW-UP MODE
DW K+1, bit 14
1 signal:
NC position control loop open; no controller enable; the drives are operated via
an external set speed value.
0 signal:
Normal state; NC position control loops closed.
Notes:
•
With the axis stationary, the 1 signal opens the position control loop.
•
If the axis is in motion, the 1 signal effects rapid deceleration with maximum braking
current, opens the position control loop after the time delay set by machine data has run
down and sets an alarm. Then only the actual position value is held.
•
All axes moving with interpolation are stopped if FOLLOW-UP MODE is set for one axis.
Axes with FOLLOW-UP MODE not set can be stopped only by selecting the set speed
value ZERO. The following error of these axes is still eliminated.
•
An alarm is output if FOLLOW-UP MODE is specified for an axis moving with interpolation.
Further execution of the NC program is then impossible.
•
After cancellation of follow-up operation (0 signal), the axis does not have to be resynchro-
nized (no approach to reference point) if the max. permissible speed of the axis has not
been exceeded at any time.
•
To avoid incorrect positioning, follow-up mode must be cancelled in the AUT mode
only if the NC program is in the STOP state.
•
If a rotary axis (C axis) is to be operated as a spindle, the axis-specific monitoring
functions can be switched off by setting the FOLLOW-UP MODE and PARKING AXIS
signals. Setting the PARKING AXIS signal also cancels the REFERENCE POINT
REACHED signal.
When subsequently switching back to C axis operation the actual value system of the axis
must be updated, whereby reference point approach can be avoided.
In conjunction with the 16-bit servo CPU
c)
the real actual position of the axis can be
calculated and output after the spindle operation with the aid of the "On-the-fly
synchronization of C axis" function. In this case, however, the REFERENCE POINT
REACHED signal is not set again. Execution of this function is subject to fulfilment of the
following preconditions:
–
Enable "On-the-fly synchronization of C axis" function (MD 1808*, bit 7 set)
–
Axis parameterized as rotary axis (MD 564*, bit 5 set)
–
"No start disable for reference point" MD bit set (MD 560*, bit 4)
–
PARKING AXIS and FOLLOW-UP MODE signals set for spindle operation
–
Incremental encoder of C axis has rotated by at least 360° in follow-up mode
(otherwise the position is calculated incorrectly, without an alarm)
–
When switching back to C axis operation, PARKING AXIS is set first, then FOLLOW-
UP MODE.
Subject to fulfilment of these preconditions, the actual position of the axis is calculated
once the FOLLOW-UP MODE signal is cancelled. Machining with the C axis can then
commence straight away.
In conjunction with the 32-bit servo CPU these operations are implemented by the
"Expanded spindle functions". Please refer to the associated Function Manual for further
details.
•
While follow-up mode is active the switchover to C-axis mode cannot be performed
completely. The block change is delayed.
_______
c)
up to and including software version 6
9
–
10
©
Siemens AG 1991 All Rights Reserved 6ZB5 410-0HE02
SINUMERIK 880 (PJ)