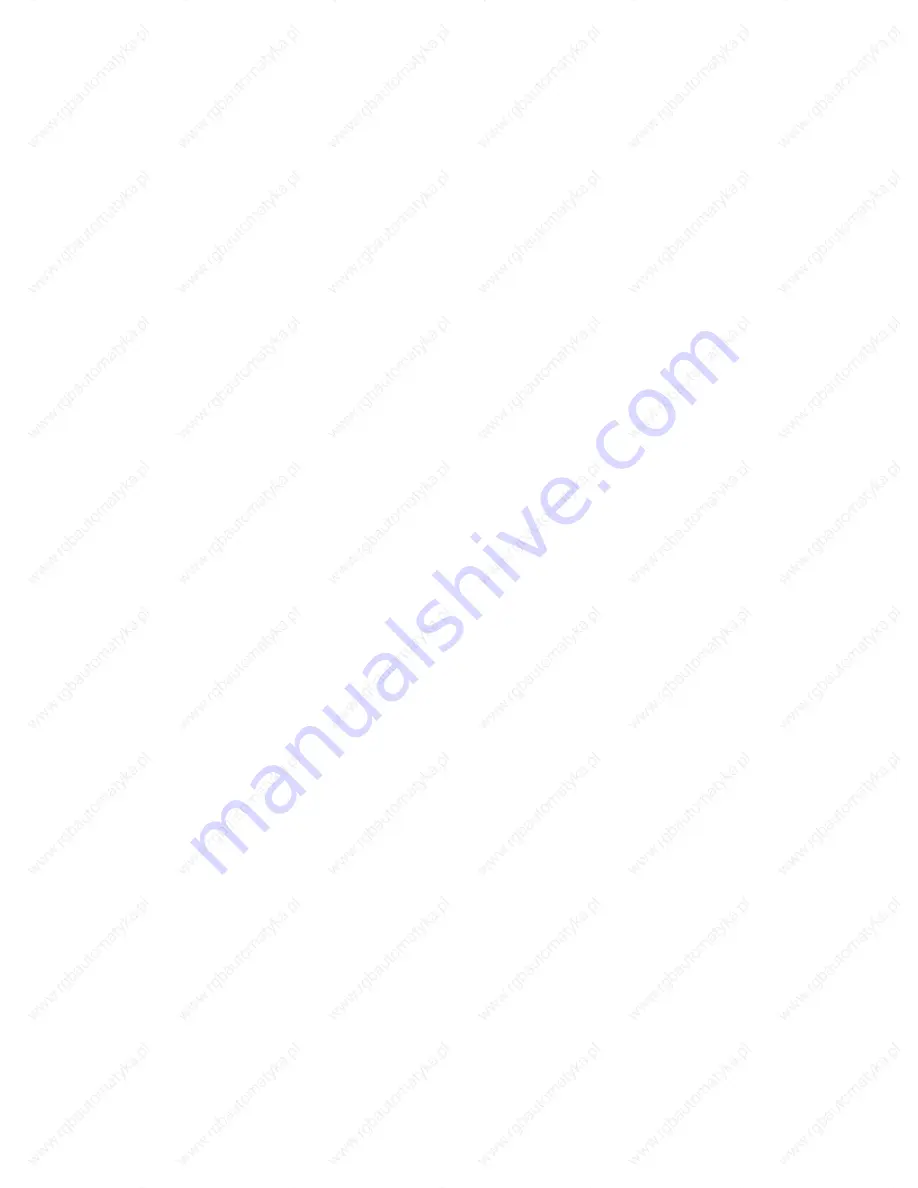
05.91
8 Spindle/PLC Interface (DB 31)
8.1 Introduction
The set speed for a spindle can be specified in three ways: in the S value from the NC, as the
basic speed, or as the oscillation speed from the PLC. If the PLC SPINDLE CONTROL signal
is set, no more new S words can be transferred to the spindle by the NC program; the PLC
user program can switch the direction of rotation of the spindle in this mode or it can specify
the basic or oscillation speed as required.
The hardware assignment spindle number <-> measuring circuit module is made by means
of NC machine data 400*. The spindle declared spindle 1 in the MD is also the 1st spindle at
the NC/PLC interface, that is to say it is assigned data words 0 ... 3, 24 and 25 in DB 31.
Generally speaking, the spindle control can operate in different spindle modes:
•
Control mode
Controlled operation with preset spindle speed and direction of
rotation
•
Oscillation mode
Controlled operation with preset motor speed and direction of
rotation
•
Positioning mode
"Oriented spindle stop"; the spindle is incorporated in position
control
Two additional modes are available for spindles that are controlled by 32-bit servo CPUs:
•
C axis mode
Spindle operated as closed-loop position-controlled rotary axis
•
Synchronous mode
"Synchronous spindle" function; two spindles (leading and following
spindle) run at synchronous speed with preset speed ratio and
defined angular offset (optional)
Notes:
•
For C axis operation, the spindle is assigned an axis by means of machine data (MD 461*).
If a C axis is assigned to the spindle by MD 461* the axis-specific signals are also evaluat-
ed.
Note in particular that the measuring circuit monitors for the axis can be switched off with
the PARKING AXIS signal so that the axis-specific measuring circuit monitors can be sup-
pressed.
•
See the "Extended Spindle Functions" Function Manual for further notes.
©
Siemens AG 1991 All Rights Reserved 6ZB5 410-0HE02
8
–
3
SINUMERIK 880 (PJ)