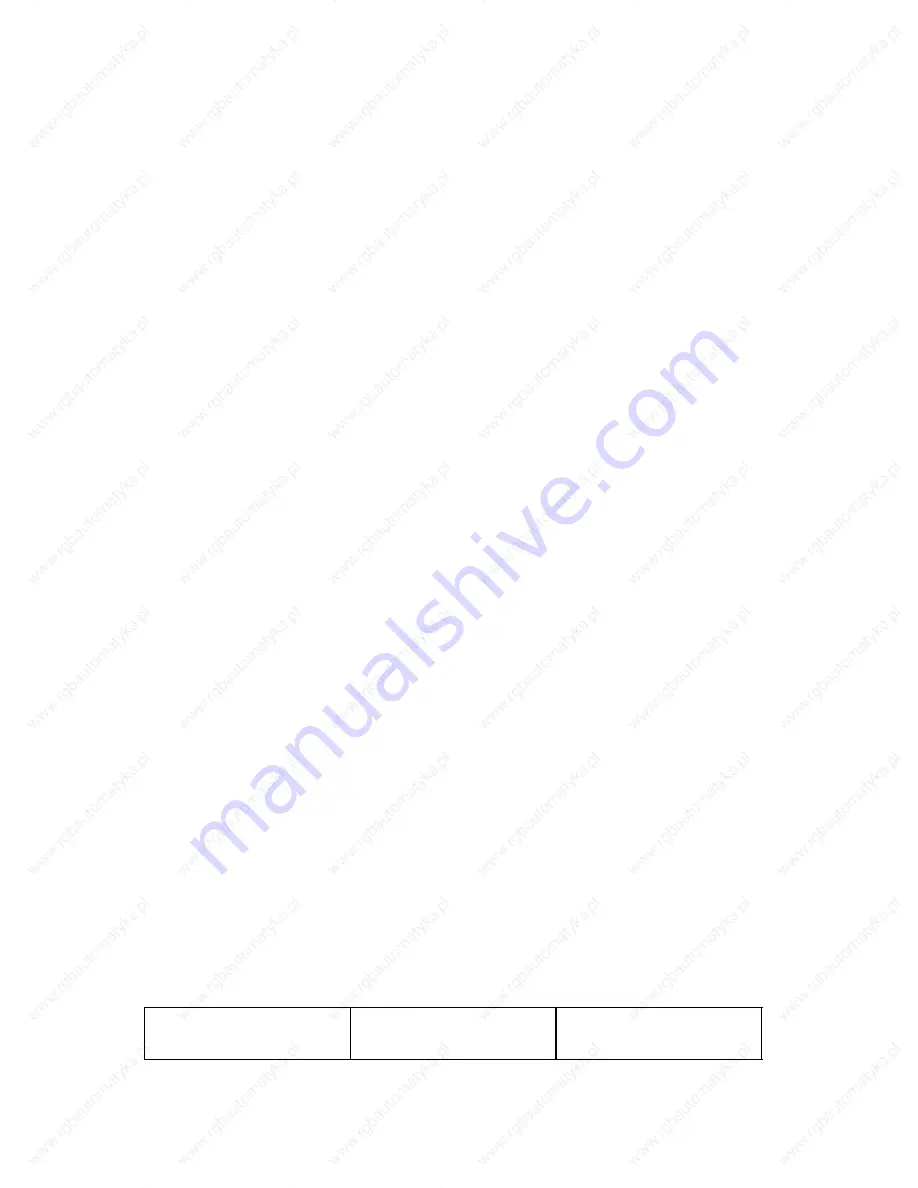
05.91
7 ELG-Specific Signals (DB 29)
7.3 Signals to ELG (DB 29)
7.3
Signals to ELG (DB 29)
a a a a a a a a a a a a a a a a a a a a a a a a a a a a a a a a a a a a a a a a a a a a a a a a a a a a a a a a a a a a a a a a a a a a a a a a a a a a a a a a a a a a a a a a a a a a a a a a a a a a a a a a a a a a a a a a
a a a a a a a a a a a a a a a a a a a a a a a a a a a a a a a a a a a a a a a a a a a a a a a a a a a a a a a a a a a a a a a a a a a a a a a a a a a a a a a a a a a a a a a a a a a a a a a a a a a a a a a a a a a a a a a a
a a a a a a a a a a a a a a a a a a a a a a a a a a a a a a a a a a a a a a a a a a a a a a a a a a a a a a a a a a a a a a a a a a a a a a a a a a a a a a a a a a a a a a a a a a a a a a a a a a a a a a a a a a a a a a a a
a a a a a a a a a a a a a a a a a a a a a a a a a a a a a a a a a a a a a a a a a a a a a a a a a a a a a a a a a a a a a a a a a a a a a a a a a a a a a a a a a a a a a a a a a a a a a a a a a a a a a a a a a a a a a a a a
a a a a a a a a a a a a a a a a a a a a a a a a a a a a a a a a a a a a a a a a a a a a a a a a a a a a a a a a a a a a a a a a a a a a a a a a a a a a a a a a a a a a a a a a a a a a a a a a a a a a a a a a a a a a a a a a
a a a a a a a a a a a a a a a a a a a a a a a a a a a a a a a a a a a a a a a a a a a a a a a a a a a a a a a a a a a a a a a a a a a a a a a a a a a a a a a a a a a a a a a a a a a a a a a a a a a a a a a a a a a a a a a a
a a a a a a a a a a a a a a a a a a a a a a a a a a a a a a a a a a a a a a a a a a a a a a a a a a a a a a a a a a a a a a a a a a a a a a a a a a a a a a a a a a a a a a a a a a a a a a a a a a a a a a a a a a a a a a a a
a a a a a a a a a a a a a a a a a a a a a a a a a a a a a a a a a a a a a a a a a a a a a a a a a a a a a a a a a a a a a a a a a a a a a a a a a a a a a a a a a a a a a a a a a a a a a a a a a a a a a a a a a a a a a a a a
a a a a a a a a a a a a a a a a a a a a a a a a a a a a a a a a a a a a a a a a a a a a a a a a a a a a a a a a a a a a a a a a a a a a a a a a a a a a a a a a a a a a a a a a a a a a a a a a a a a a a a a a a a a a a a a a
CALCULATE NEW K
Ü
DW m + 2, bit 15
0/1 transition:
The speed ratios between the following axis and its leading axes are recalcu-
lated with the signal change from 0 to 1. The speed ratio parameters must be
entered in the setting data first. The NC sets the NEW K
Ü
CALCULATED sig-
nal if it was possible to calculate the speed ratios without error. If an error
occurs during the calculation, the NC sets the NEW K
Ü
DEFECTIVE signal
and issues an alarm.
1/0 transition:
The PLC user program must reset the signal to 0 once the NC has calculated
the new speed ratios
(NEW K
Ü
CALCULATED = 1 or NEW K
Ü
DEFECTIVE = 1).
Notes:
•
The speed ratio parameters are specified in setting data words SD 10 to SD 39.
•
The calculation of speed ratios can also be initiated by the CALCULATE NEW K
Ü
setting
data bit. With each 0/1 transition of the CALCULATE NEW K
Ü
interface signal the NC
program sets the setting data bit of the same name.
•
The new speed ratios are put into effect by ACTIVATE NEW K
Ü
.
a a a a a a a a a a a a a a a a a a a a a a a a a a a a a a a a a a a a a a a a a a a a a a a a a a a a a a a a a a a a a a a a a a a a a a a a a a a a a a a a a a a a a a a a a a a a a a a a a a a a a a a a a a a a a a a a
a a a a a a a a a a a a a a a a a a a a a a a a a a a a a a a a a a a a a a a a a a a a a a a a a a a a a a a a a a a a a a a a a a a a a a a a a a a a a a a a a a a a a a a a a a a a a a a a a a a a a a a a a a a a a a a a
a a a a a a a a a a a a a a a a a a a a a a a a a a a a a a a a a a a a a a a a a a a a a a a a a a a a a a a a a a a a a a a a a a a a a a a a a a a a a a a a a a a a a a a a a a a a a a a a a a a a a a a a a a a a a a a a
a a a a a a a a a a a a a a a a a a a a a a a a a a a a a a a a a a a a a a a a a a a a a a a a a a a a a a a a a a a a a a a a a a a a a a a a a a a a a a a a a a a a a a a a a a a a a a a a a a a a a a a a a a a a a a a a
a a a a a a a a a a a a a a a a a a a a a a a a a a a a a a a a a a a a a a a a a a a a a a a a a a a a a a a a a a a a a a a a a a a a a a a a a a a a a a a a a a a a a a a a a a a a a a a a a a a a a a a a a a a a a a a a
a a a a a a a a a a a a a a a a a a a a a a a a a a a a a a a a a a a a a a a a a a a a a a a a a a a a a a a a a a a a a a a a a a a a a a a a a a a a a a a a a a a a a a a a a a a a a a a a a a a a a a a a a a a a a a a a
a a a a a a a a a a a a a a a a a a a a a a a a a a a a a a a a a a a a a a a a a a a a a a a a a a a a a a a a a a a a a a a a a a a a a a a a a a a a a a a a a a a a a a a a a a a a a a a a a a a a a a a a a a a a a a a a
a a a a a a a a a a a a a a a a a a a a a a a a a a a a a a a a a a a a a a a a a a a a a a a a a a a a a a a a a a a a a a a a a a a a a a a a a a a a a a a a a a a a a a a a a a a a a a a a a a a a a a a a a a a a a a a a
a a a a a a a a a a a a a a a a a a a a a a a a a a a a a a a a a a a a a a a a a a a a a a a a a a a a a a a a a a a a a a a a a a a a a a a a a a a a a a a a a a a a a a a a a a a a a a a a a a a a a a a a a a a a a a a a
ACCELERATION LIMITATION SYNCHRONOUS ACTIVE
DW m + 2, bit 14
0/1 transition:
On a positive edge of the signal, the signal ACCELERATION LIMITATION
SYNCHRONOUS is switched active. If the ACCELERATION LIMITATION
SYNCHRONOUS ACTIVE signal is a 0 signal, the acceleration limitation is
switched on, otherwise it is switched off.
1/0 transition:
The PLC user program must reset the signal to 0 if the status of ACCELERA-
TION LIMITATION SYNCHRONOUS ACTIVE has changed.
Notes:
•
The acceleration limitation for the following axis can also be switched with the ACCELER-
ATION LIMITATION SYNCHRONOUS setting data bit. The NC transfers every change ef-
fected by the interface signal to the setting data bit.
•
The acceleration limitation for the following axis ensures, if the gear link is active, that the
following axis runs in positional synchronism with the leading axes again even after
acceleration processes. Positional deviations that occur during the acceleration are added
up and corrected after the acceleration process; that is to say the following axis
accelerates for a slightly longer time than the leading axes and thus catches them up (see
figure).
FA 1: m=0
FA 2: m=4
FA 3: m=8
©
Siemens AG 1991 All Rights Reserved 6ZB5 410-0HE02
7
–
13
SINUMERIK 880 (PJ)