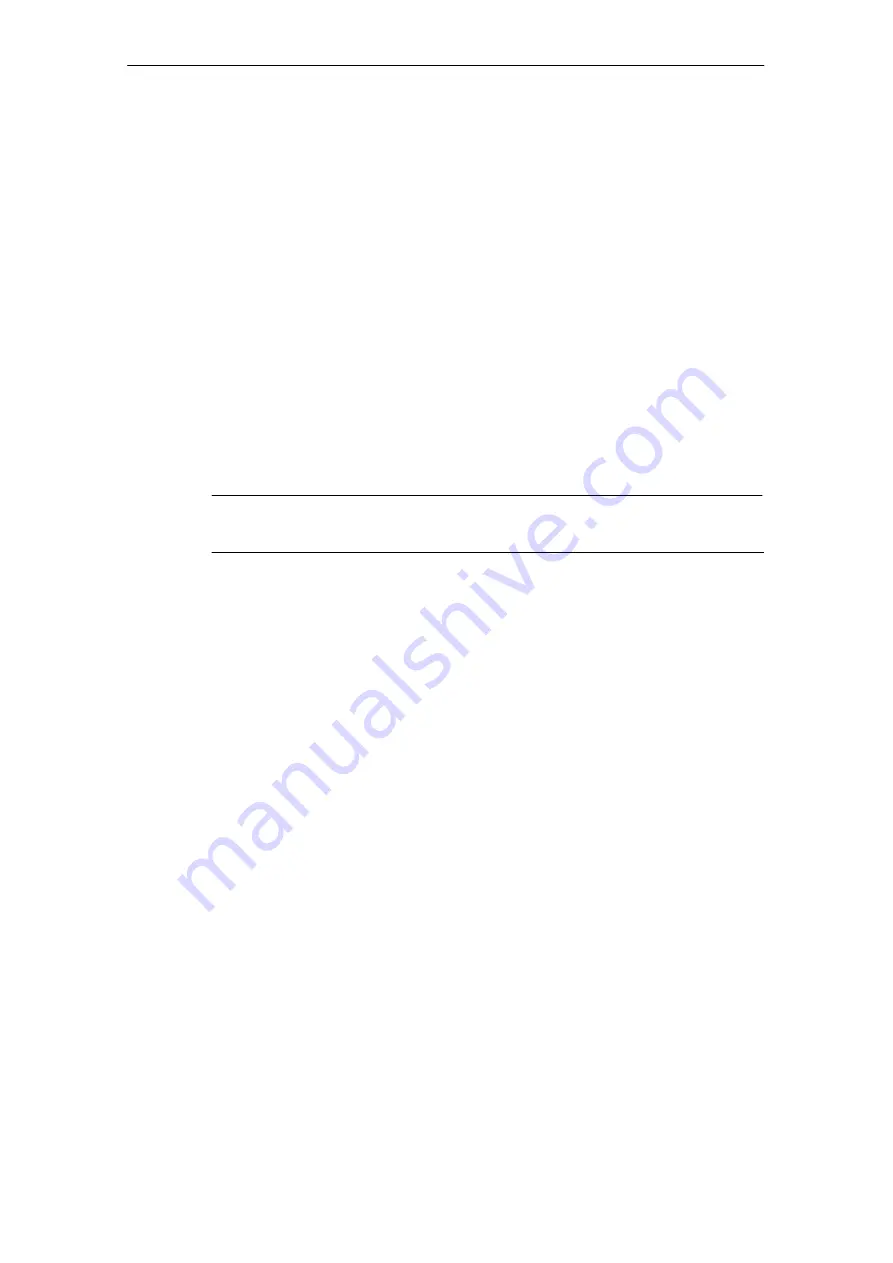
Commissioning / Operation / Maintenance
AddFEM
5-52
AddFEM
C79000–G8076–C900–03
5.6.2
FEM_AO – Analog Output
The following OBs must call the function block FEM_AO:
a) Watchdog interrupt OB for cyclic operation (for example OB 32).
b) In addition the block has to be called in the OB 100 for the start–up processing.
Area of Application
The block writes the output data to the AddFEM.
Functional Description
The FEM_AO block converts the 8 analog values in REAL format at the input bar
which are to be output into standardized fixed–point values and transfers these to
the analog outputs of the AddFEM. If the switch SIMULx = 1 is set, the simulation
value AOx_SIM is output.
Note
SIMUAIx means SIMUAI<Channel Number 1 to 12> e.g. SIMUAI1.
If the range is exceed, the output value is limited to approx. 18% over the physical
limit.
Mode of Operation
The block reads the logic addresses entered in the BLOCKCON input structure
and writes all the output data (analog and digital outputs) consistently to all the
connected AddFEMs.
Error Handling
If there is a fault at a channel (Qualifier Bit=1), the corresponding channel fault out-
put QCHx_F is set to 1.
In case of configuration errors all the channel faults outputs are set. The outputs
cannot be simulated in this case.
If there is a configuration error (incorrect address), this is signaled at the output
QPARF = 1.
Start–up Characteristics
The range limits (AIx_HRG and AIx_LRG) are converted into factors and offsets in
order to calculate the current input values during the initial start–up or restart. In
case of incorrect error configuration (for example Upper limit <= Lower limit) the
output value is set to zero.
Artisan Technology Group - Quality Instrumentation ... Guaranteed | (888) 88-SOURCE | www.artisantg.com
Содержание Add 7 AddFEM
Страница 7: ...Artisan Technology Group Quality Instrumentation Guaranteed 888 88 SOURCE www artisantg com ...
Страница 27: ...Artisan Technology Group Quality Instrumentation Guaranteed 888 88 SOURCE www artisantg com ...
Страница 51: ...Artisan Technology Group Quality Instrumentation Guaranteed 888 88 SOURCE www artisantg com ...
Страница 81: ...Artisan Technology Group Quality Instrumentation Guaranteed 888 88 SOURCE www artisantg com ...