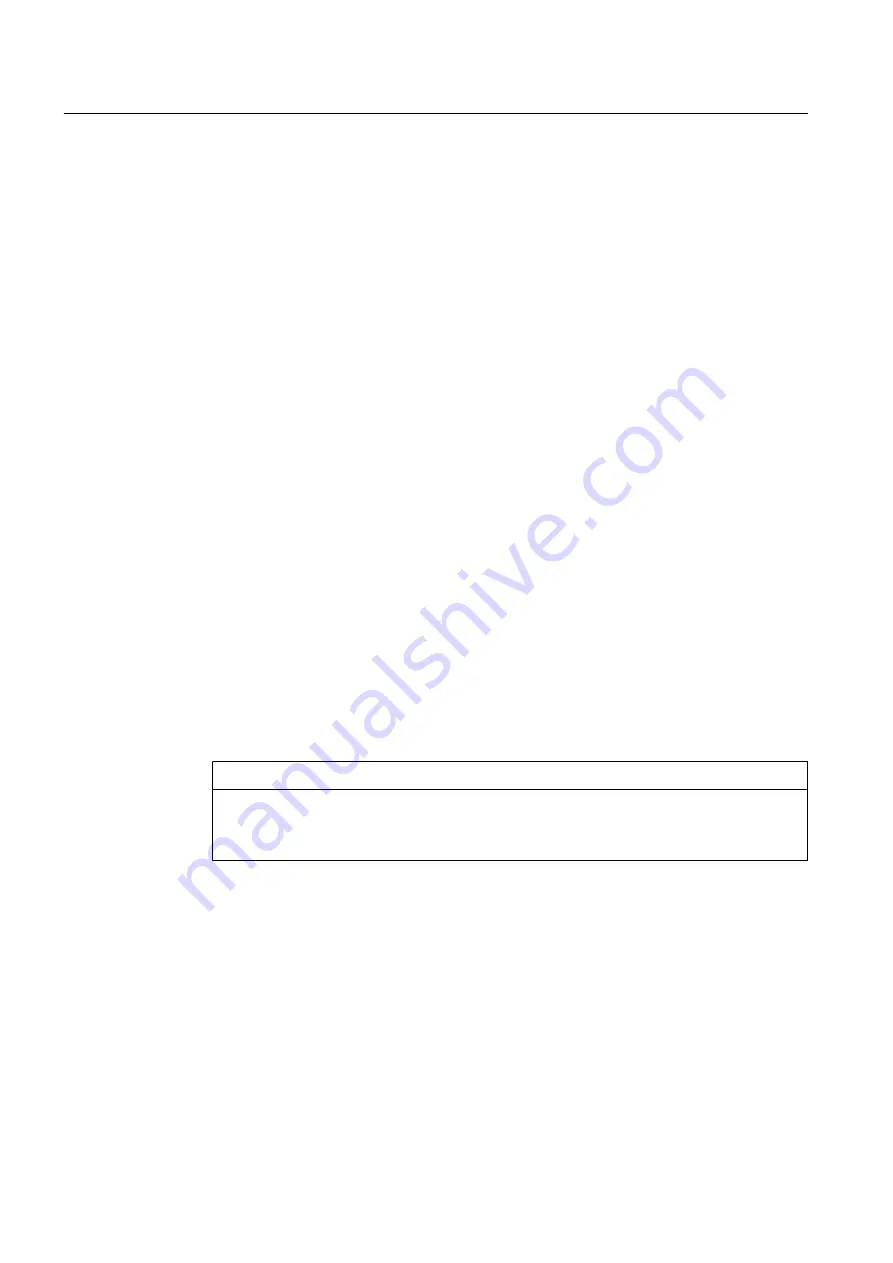
Avoiding mechanical damage to bearings
Regularly inspect all machines for any mechanical damage. Especially observe that the
bearing replacement intervals and relubrication intervals, respectively grease change intervals
or oil change intervals specified by the machine manufacturer are maintained.
Replace the bearings once they have reached their nominal service life or verify that they are
mechanically in good working order as part of an inspection.
● Where bearings are sealed for life, there is a guarantee that the rated service life is achieved
only well after expiry of the service life of the grease in the bearing.
● The theoretical nominal service life of the bearings can be taken from the data sheet of the
machine if this was specified – or was specifically defined for mechanical design reasons
for a particular application.
● Where machines are subject to externally applied forces (e. g. the force on a drive belt or
axial forces arising from the driven machine), at the full loadings listed on the technical
specification the rated service life of the bearings is at least 20,000 hours.
● For all other machines, the rated service life of the bearings is at least 40,000 hours.
● For bearings with external oil supply, monitor the lubrication system to ensure that it is
operating correctly.
7.4
Test run
After installation or inspection, carry out a test run:
1. Start up the machine without a load. To do this, close the circuit breaker and do not switch
off prematurely. Check whether it is running smoothly.
Switching the machine off again while it is starting up and still running at slow speed should
be kept to a bare minimum, for example for checking the direction of rotation or for checking
in general.
Allow the machine to run down before switching it on again.
NOTICE
Avoiding mechanical damage to the cylindrical roller bearing
Under all circumstances maintain the minimum load on cylindrical roller bearings of 50%
corresponding to what is specified in the catalog.
2. If the machine is running smoothly and evenly, switch on the cooling equipment. Continue
to observe the machine for a while in no-load operation.
Commissioning
7.4 Test run
SIMOTICS HV C 1NB1402-2AA84-4CA0-Z
72
Operating Instructions 06/2018
Содержание 1NB1402-2AA84-4CA0-Z
Страница 2: ...26 06 2018 15 34 V3 00 ...
Страница 10: ...Table of contents SIMOTICS HV C 1NB1402 2AA84 4CA0 Z 10 Operating Instructions 06 2018 ...
Страница 22: ...Description SIMOTICS HV C 1NB1402 2AA84 4CA0 Z 22 Operating Instructions 06 2018 ...
Страница 84: ...Operation 8 9 Faults SIMOTICS HV C 1NB1402 2AA84 4CA0 Z 84 Operating Instructions 06 2018 ...
Страница 110: ...Disposal 11 4 Disposal of components SIMOTICS HV C 1NB1402 2AA84 4CA0 Z 110 Operating Instructions 06 2018 ...
Страница 112: ...Service and Support SIMOTICS HV C 1NB1402 2AA84 4CA0 Z 112 Operating Instructions 06 2018 ...
Страница 117: ...117 ...
Страница 118: ...118 ...
Страница 119: ...119 ...
Страница 120: ...120 ...
Страница 121: ...121 ...
Страница 122: ...122 ...
Страница 123: ...123 ...
Страница 124: ...124 ...
Страница 125: ...125 ...
Страница 126: ...126 ...
Страница 127: ...127 ...
Страница 128: ...128 ...
Страница 129: ...129 ...
Страница 130: ...130 ...
Страница 131: ...C 2 Declaration of conformity SIMOTICS HV C 1NB1402 2AA84 4CA0 Z Operating Instructions 06 2018 131 ...
Страница 132: ...Quality documents C 2 Declaration of conformity SIMOTICS HV C 1NB1402 2AA84 4CA0 Z 132 Operating Instructions 06 2018 ...
Страница 133: ...133 ...
Страница 148: ...148 ...
Страница 150: ...Additional documents SIMOTICS HV C 1NB1402 2AA84 4CA0 Z 150 Operating Instructions 06 2018 ...
Страница 154: ...Index SIMOTICS HV C 1NB1402 2AA84 4CA0 Z 154 Operating Instructions 06 2018 ...
Страница 155: ...AF Einbauerklärung Loher LDX U157 AJ EC Declaration of Conformity U161 ...