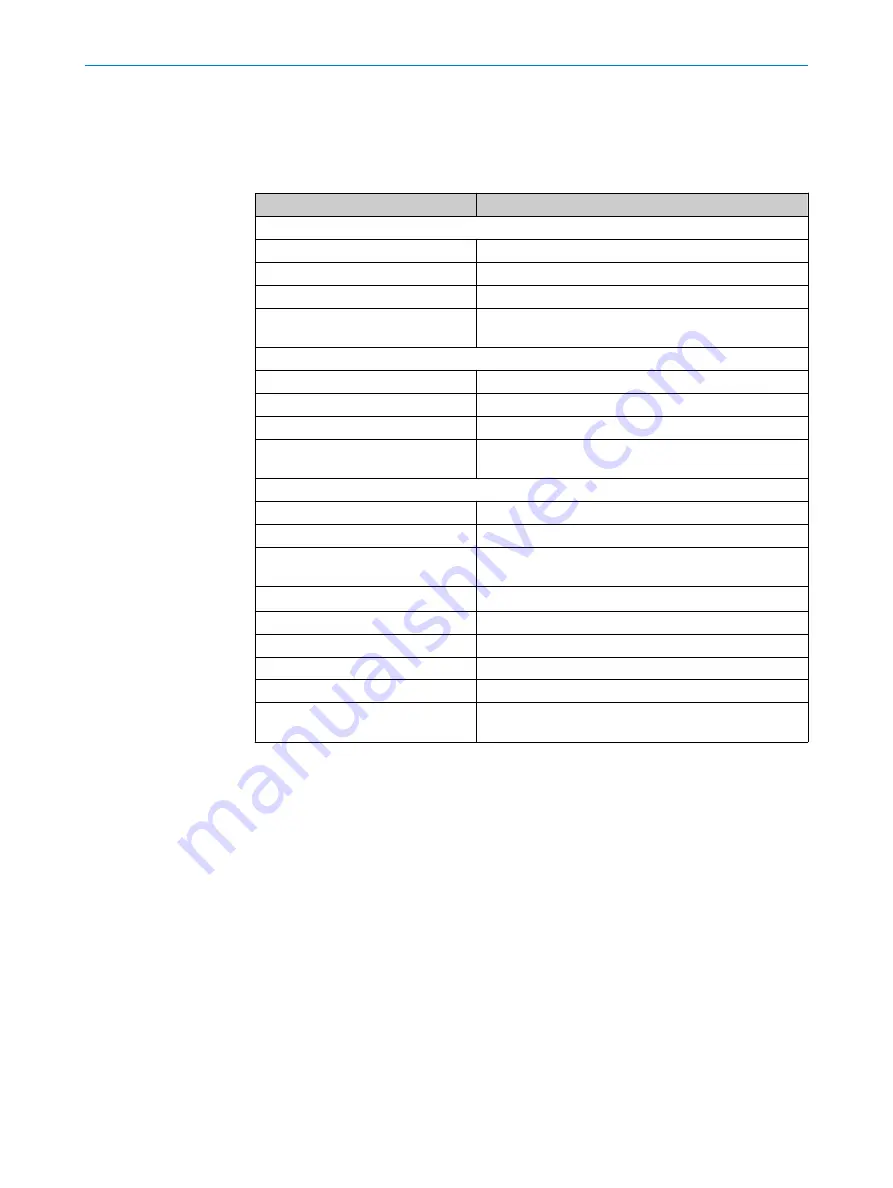
12
Technical data
12.1
Data sheet
Table 15: Safe Entry Exit data sheet
Safe Entry Exit
For higher-level control with MTTFd value of at least 10 a
Performance level
PL d (ISO 13849-1)
Category
Category 3 (ISO 13849-1)
SIL claim limit
SILCL2 (EN 62061)
PFHd (mean probability of one dan‐
gerous failure per hour)
2.15 × 10
–7
For higher-level control with performance level PL e
Performance level
PL e (ISO 13849-1)
Category
Category 3 (ISO 13849-1)
SIL claim limit
SILCL3 (EN 62061)
PFHd (mean probability of one dan‐
gerous failure per hour)
4.53 × 10
–8
Safe Entry Exit manual muting function
Performance level
PL d (ISO 13849-1)
Category
Category 2 (ISO 13849-1)
PFHd (mean probability of one dan‐
gerous failure per hour)
5.34 × 10
–7
Supply voltage U
V
24 V DC (16.8 V DC ... 28.8 V DC) (SELV)
1)
Ambient operating temperature
See operating instructions for the individual components
Storage temperature
See operating instructions for the individual components
Air humidity
See operating instructions for the individual components
Permissible operating height
See operating instructions for the individual components
Safe state
The safety-related semiconductor outputs are in the OFF
state.
1)
The external supply voltage must jumper a brief power failure of 20 ms as specified in IEC 60204-1. Suit‐
able power supply units are available as accessories from SICK.
12
TECHNICAL DATA
44
O P E R A T I N G I N S T R U C T I O N S | Safe Entry Exit
8021675/ZV26/2019-05-13 | SICK
Subject to change without notice