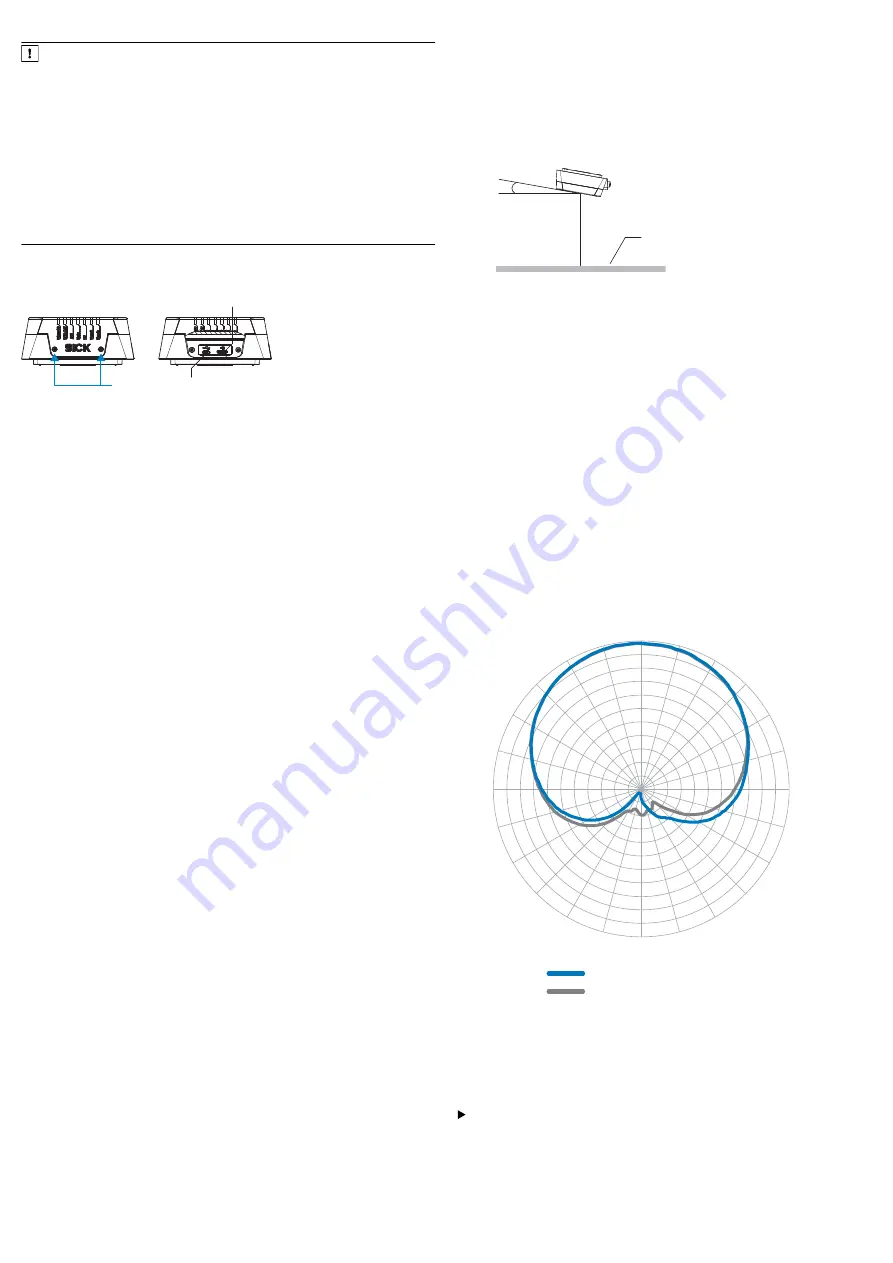
Inserting or removing a memory card
NOTICE
Possible data loss or irreparable damage to the memory card!
The device does not signal the direct access (read/write) to the card but the
current status of the card,
•
Only use the memory card when the device power is off.
•
Do not remove the memory card or switch off the supply voltage while
the following functions are taking place in the device:
°
Storage of parameter values with the SOPAS ET configuration soft‐
ware with the “Permanent” option
°
Functions have been started that access the memory card (e.g.
concurrent logging of data)
•
To remove the memory card safely during operation, select the
Remove
card
function under
Analysis tools/MicroSD card
in SOPAS ET. Wait for the
feedback from SOPAS ET to release the card.
The card slot can be accessed on the device behind the side cover (plastic foil),
.
Maintaining enclosure rating IP65 or IP67:
see Safety information, page 1
.
3
2
1
Figure 2: Access to USB interface and memory card slot
1
Slot for microSD memory card
2
“USB” connection (female connector, 5-pin, Micro B type)
3
2 x screw, Torx T8
1.
Switch off the supply voltage to the device.
2.
Loosen both screws on the cover.
3.
Carefully fold up the cover.
4.
Making sure it is in the correct position, insert the memory card into the card
slot until it locks into place. When doing so, orient the contacts forwards and
downwards as per the symbol on the device.
5.
Screw the cover back on. Recommended tightening torque for the cover
screws: 60 Ncm ± 5 Ncm.
6.
Switch the supply voltage for the device back on.
7.
Once it is switched on, the device automatically detects the presence of a
memory card and, depending on the memory card’s content, behaves as fol‐
lows:
°
If the memory card is empty or if does not contain a parameter set that
can be interpreted by the device:
the device saves its currently valid internal parameter set to the card
(provided there is sufficient storage space) and starts with the internal
parameter set.
°
If the card contains a parameter set that can be interpreted by the
device:
the device overwrites the currently valid internal parameter set with this
external parameter set.
The goal is for the internal parameter set and the parameter set saved
externally to always be identical.
4
Mounting
4.1 Scope of delivery
•
Device in the version ordered (variant line, regional assignment). Electrical
M12 connections are fitted with protective caps or plugs. RFU620-101xx/
RFU620-105xx: Without connecting cables. All devices: Without brackets.
•
Regional printed Quickstarts. Included language versions:
. Other language versions may be available in PDF for‐
mat on the device product page on the Internet at:
.
4.2 Equipment required
•
2 x M6 screws or 4 x M5 screws for mounting the device on a mounting
device (bracket) provided by the customer. The screw length depends on the
mounting base (wall thickness of the bracket).
•
When using an optional SICK bracket, the screws for mounting the device on
the bracket are included the scope of delivery of the bracket.
4.3 Mounting requirements
•
The permissible ambient conditions for operating the device must be
observed, e.g. assigned radio region, ambient temperature:
and ground potential
see Electrical installation, page 4
•
The device must be mounted using all 2 M6 or 4 M5 blind tapped holes pro‐
vided,
•
If necessary, provide stable mounting equipment with sufficient load-bearing
capacity and appropriate dimensions for the device. Weight of the device
(without cables)
•
Make sure there is no electrically conductive material between transponder
and device.
4.4 Mounting the device
1.
Select a suitable mounting location for the device. The mounting location
and position depend on the antenna field of the device and the transpon‐
ders used.
2.
Perform one of the following steps:
a)
Mount the device on the bracket provided by the customer using 2 or 4
screws. Screw the M6 screws no more than 6 mm deep or M5 screws
no more than 9 mm deep into the blind tapped holes,
.
b)
Mount the device on the SICK mounting accessories ordered sepa‐
rately. Proceed as described under a).
3.
Align the surface of the integrated antenna of the device (front face) to the
transponder on the object. While doing so, take into account the shape,
alignment, and dimensions of the antenna field. Avoid as far as possible any
large metal surfaces positioned to the front. If this is not possible, do not
mount the antenna plane parallel with the surface.
10°
1
Figure 3: Selection of the approach angle with a large metal surface on the
front. e.g.
10°
1
Metal surface
4.
Ensure there is no electrically conductive material (e.g., metal, liquids) or
persons between the device and the transponder during the write or read
process. This will absorb or reflect the generated UHF field and thereby
reduce the read range.
Read range
The environment influences the UHF field of the integrated antenna, making it
impossible to provide a “clear” demarcation of the read range.
•
Application-specific reflections can result in both overreaches and “holes”
•
Other factors that can significantly impact the read range include:
°
Quality of the transponder: antenna gain, the integrated transponder
chip and related sensitivity, reflected energy
°
Material of the carrier object (plastic, wood, metal)
°
Objects between the device and transponder that can affect the UHF
field (items, liquids, people)
In addition to the read results, the device can also output diagnostic data. The
diagnostic data provides an indication of the write and read quality. This diagnos‐
tic data can be used to achieve optimum read results when setting up the system.
The radiation pattern shown here for the device’s integrated antenna was
obtained in a repeatable environment (absorber chamber as a reflection-free
space) for illustrative purposes. The diagram shows how the UHF field propagates
in the reflection-free space, but cannot be used to draw any conclusions on the
likely read range in a real application on-site.
–28
–25
–22
–19
–16
–13
–10
–7
–4
–1
2
0°
15°
30°
45°
60°
75°
90°
105°
120°
135°
150°
165°
180°
–165°
–150°
–135°
–120°
–105°
–90°
–75°
–60°
–45°
–30°
–15°
5
2
1
Figure 4: Radiation pattern of the integrated antenna of the RFU62x (typical):
Measured antenna gain in dBic at 866.5 MHz, RHCP (right-hand circularly polar‐
ized)
1
Horizontal plane (azimuth)
2
Vertical plane (elevation)
2
Elevation plane (vertical)
4.5 Mounting the CDB620 connection module
Mount the CDB620 connection module in the vicinity of the device
(RFU620-101xx, RFU620-104xx). When using the serial data interfaces
(RS-232), the recommended cable length between the devices is 5 mmaxi‐
mum. Mount the CDB620 in such a way that the connection module can be
accessed at all times, see the CDB620 connection module operating instruc‐
tions.
8015928/10XW/2019-12-12/en
RFU62x | SICK
3