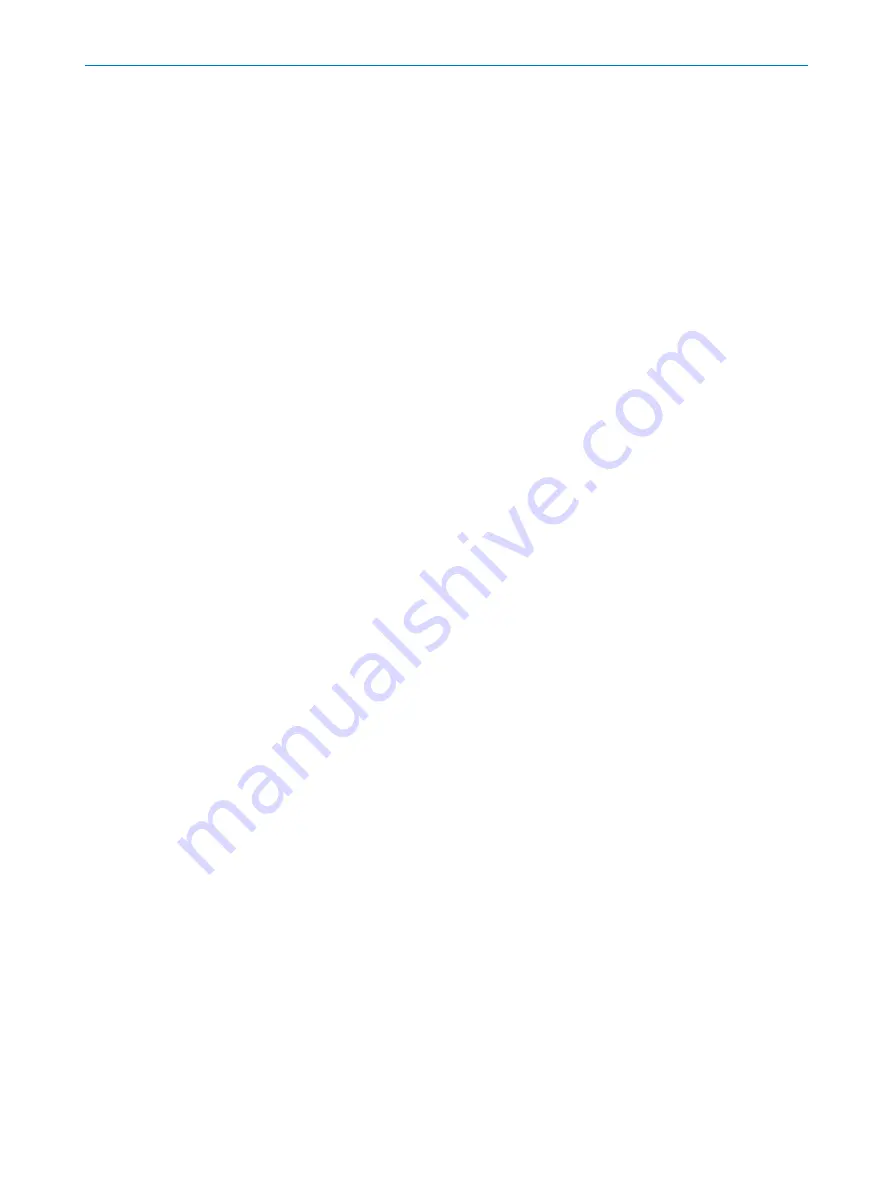
•
If the ESPE is clear, exit monitoring is ended after the sensor gap monitoring of
0.5 s has passed
•
If the light path of the ESPE does not become clear, exit monitoring is ended at the
latest once the muting condition is no longer satisfied
4.3.6.4.3
Sensor gap monitoring
Overview
Sensor gap monitoring allows signals from the muting sensors and the muting end
by ESPE function to be ignored for a defined period without removing a valid muting
condition.
Sensor gap monitoring (muting sensor)
If a muting sensor briefly becomes clear, i.e. an object gap is detected, the deactivated
muting signal continues to be interpreted as an active signal and muting is maintained.
Muting is only ended if one of the muting sensors is clear for longer than 0.5 s.
The following applies to sensor gap monitoring (muting sensor)
•
Sensor gap monitoring is always active
•
Only one of the muting sensors may be clear (deactivated) briefly. If the 2nd
muting sensor is also clear, muting is ended.
•
Muting is ended if one of the muting sensors is clear (deactivated) for longer than
0.5 s
Sensor gap monitoring (ESPE)
If the ESPE is becomes clear for a short time, i.e. an object gap is detected, muting is
maintained.
Muting is only ended if the ESPE is clear for longer than 0.5 s.
The following applies to sensor gap monitoring (ESPE):
•
Sensor gap monitoring (ESPE) is active during exit monitoring in combination with
the muting end by ESPE function
•
The ESPE is allowed to be clear for a short time, i.e. to detect a short object gap
•
Muting is ended if the ESPE is clear for longer than 0.5 s
4.3.6.4.4
Concurrence monitoring
Overview
Concurrence monitoring is configured for protecting the safety application from tamper‐
ing (e.g. covering an optical sensor).
Principle of operation
Concurrence monitoring checks whether both muting sensors are actuated within
24 hours. If a muting signal does not appear within this period, muting is not triggered.
Muting can only be triggered again if all muting sensors are clear.
Concurrence monitoring is always active.
4.3.6.4.5
Total muting time
The total muting time limits the maximum duration of muting to 24 hours, i.e. muting
then ends at the latest once the total muting time has passed. The system then
changes to the override required status.
The total muting time is always active.
PROJECT PLANNING
4
8021645/1EB0/2022-04-28 | SICK
O P E R A T I N G I N S T R U C T I O N S | deTec4
45
Subject to change without notice