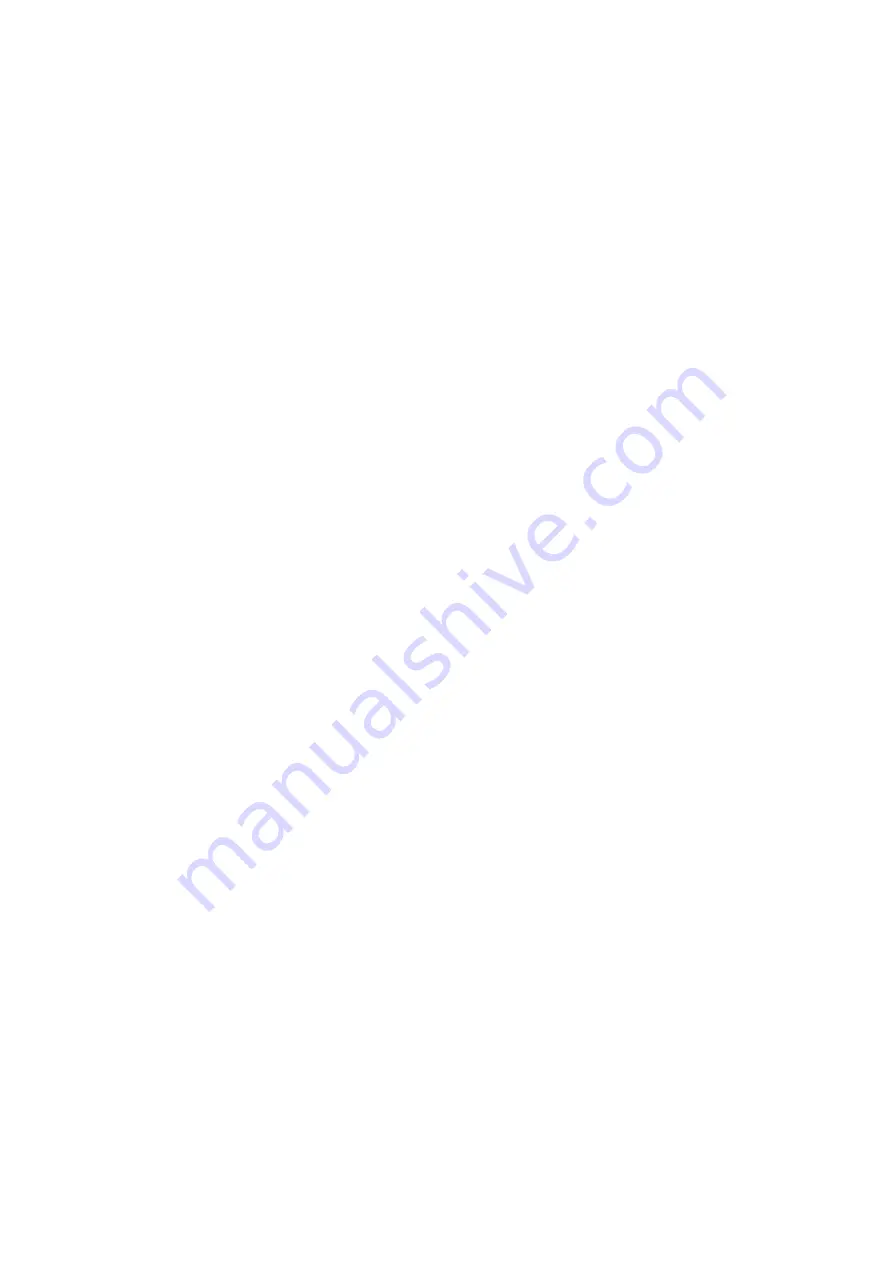
c. lightly push the search card A in the direction of the metal disc D, tighten the two fastening screws then remove the calibration template.
IMPORTANT:
after any adjustment or after replacing the encoder board, perform the relative test cycle by performing a spin with a wheel, and check
that the two numerical
values shown on the right hand side of the row denominated ENCODER TEST in the service environment match.
If replacing this component does not resolve the problem, replace the fork cable (A, Fig.3).
- The values of the transducers / sensors used to obtain the geometric data of the wheel, together with their typical variation intervals.
These data allow to:
to easily check their efficiency. In particular, that when moving the sensor the relative values are continuously modified within the envisaged
intervals (see also paragraph 6):
diameter sensor
-110
distance sensor
from 0 to 630 if the sensor rod is short (527mm);
from 0 to 720
if the sensor rod is long (572mm);
There is a green window to the side of the distance sensor value that displays the message “ON”, which indicates the status of the zero sensor
used for zero-setting the automatic sensor.
This message changes to “OFF” when the internal sensor is extracted and returns to “ON” when it returns to the rest position (reference
distance sensor value 5 +/-1). If this update does not occur, carry out the checks described in the “internal and external sensor” chapter.
width dial setting from 5 to 255, with external sensor installed.
This value is updated by moving the external sensor towards and away from the operator.
External sensor distance from 5 to 1950, with ultrasonic sensor installed.
This value is updated within the operating range of the sensor itself (min. distance 60mm - max. distance 400mm).
- that the wheel guard (COVER) micro-switch is working correctly; OPEN state with wheel guard open, CLOSE state with wheel guard lowered.
- that the PL clamping system pedal (C CONTROL PEDAL) micro-switch is working correctly. OPEN state when the pedal is NOT pressed, PRESS
when the PL pedal is pressed.
These values may be used to determine if the wheel guard micro-switch and the micro-switch of the PL automatic clamping system control
pedal are working correctly.
- speed (rpm) and the number of any discarded periods in the last spin executed.
These data allow to:
check that the spin speed is correct (rpm), using an average sized wheel (typically 5.5” x 14”) - speed value must be within the range from 95-
105.
check for interference during the spin. If there is a number different from 0/X (where X is the number of sampled periods during the spin)
repeat the spin, taking care not to knock the wheel balancer during the readout phase.
If the machine was not knocked, check inside the machine whether:
• the wheel balancer is resting firmly on the floor;
• the shaft assembly has noisy bearings;
• the securing ring nut is fastened tightly;
• the anchor fixed to the hub is not touching the brake, and the clutch in the electromechanical locking system is not touching the anchor fixed
to the cone of the internal device during the signal acquisition phase.
- the following numerical values:
1. amplitude and phase of the signal generated by the internal pick-up.
2. amplitude and phase of the signal generated by the external pick-up.
3. the phase displacement (in relation to the
reference value of 180 degrees) of the signal of the external pick-up compared with that of the
internal pick-up. The value is expressed in encoder notches (whole part) and in tenths of a notch (decimal part). One encoder notch
corresponds to about 1.4 degrees.
4. to visualise or update the values, it is necessary to:
- to calibrate with the 100 g weight, mount a previously balanced medium sized wheel (5.5”X14”) on the swinging unit (after selecting “1
ON” mode with the icon) and apply the calibration weight (100 g) on the external side;
- to calibrate with the SLUG calibration counterweight, mount a previously balanced medium sized wheel (typically 5.5”X14”) or a larger
wheel, but with a mass NOT exceeding 40 Kg. Apply the SLUG (calibration weight) in the position indicated in the figure:
Содержание S 64E
Страница 43: ...Fig 20 fig 21...
Страница 45: ......
Страница 46: ...SECOND VERSION OF PNEUMATIC SYSTEM from April 2016...
Страница 47: ...THIRD VERSION OF PNEUMATIC SYSTEM from March 2017...
Страница 48: ...FOURTH VERSION OF PNEUMATIC SYSTEM...
Страница 50: ...PEAL 32F...
Страница 51: ......
Страница 52: ...MBUGRF 2 LIGHT...
Страница 53: ......
Страница 54: ...COMIM Cod 4 119446B_EN 05 2018...