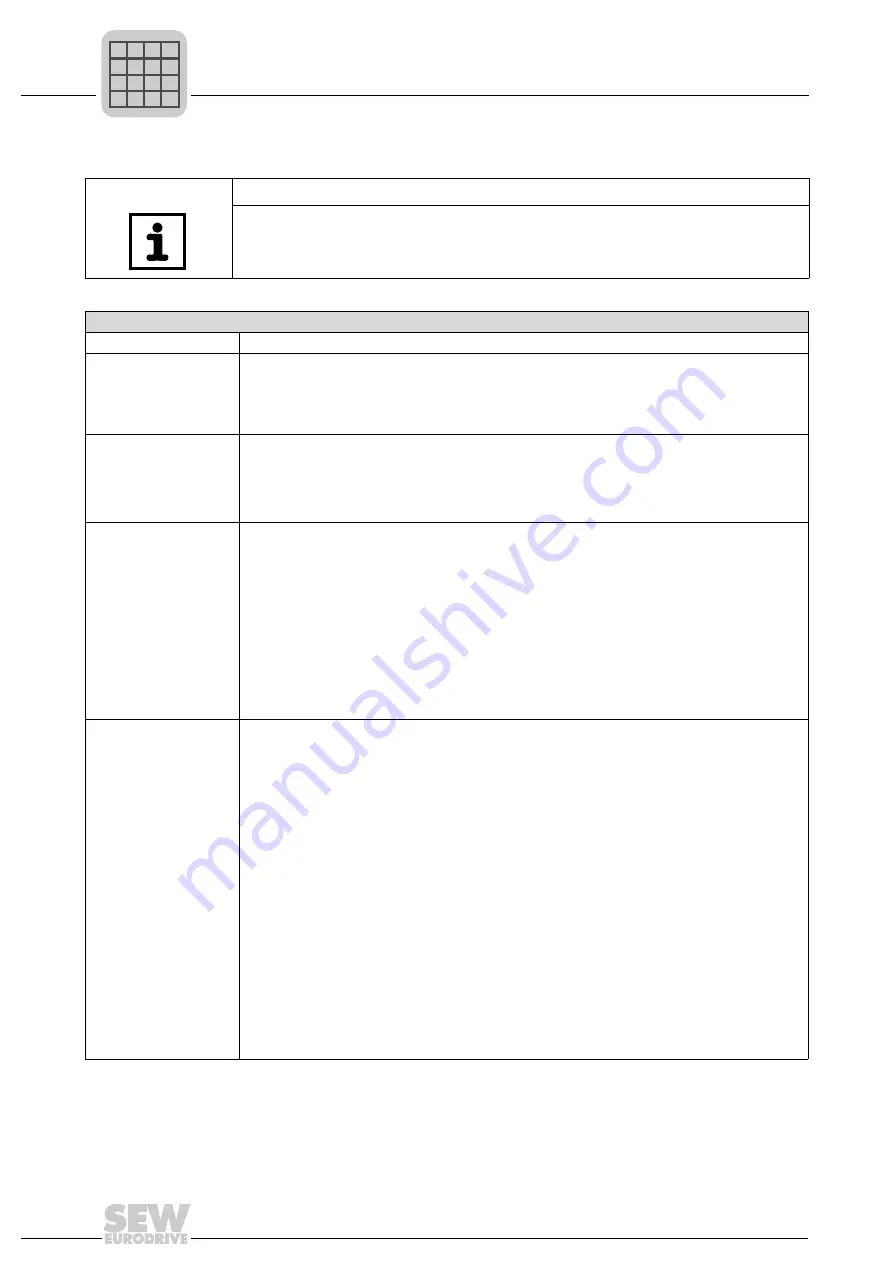
64
Manual – MOVI-PLC® advanced DHE41B/DHF41B/DHR41B Controller
7
MOVI-PLC® advanced DHF41B controller
Technical Data and Dimension Drawings
7.3
MOVI-PLC
®
advanced DHF41B controller
NOTE
The connections identical with DHE41B are described in section "MOVI-PLC
®
advanced
DHE41B controller".
MOVI-PLC
®
advanced
DHF41B controller
Part number
MOVI-PLC
®
advanced
DHF41B: 1821 161 5
Electrical supply
Integrated in MOVIDRIVE
®
MDX61B:
•
Power consumption: P
max
= 8 W
Installed in the MOVIAXIS
®
master module (MXM):
•
Power consumption: P
max
= 10 W
Potential levels
The MOVI-PLC
®
advanced
DHF41B controller has the following potential levels:
•
Potential controller/CAN 1/COM1
•
Potential COM2
•
Potential binary inputs and outputs
•
Potential system bus CAN 2
•
Potential PROFIBUS
PROFIBUS connection
X30P:1 ... X30P:9
Bus terminator
Automatic baud rate
detection
Protocol options
GSD file
DP ID number
Via 9-pin sub D connector, pin assignment according to IEC 61158
Not integrated. Implement bus termination with suitable PROFIBUS connector with switchable terminating
resistors.
9.6 kBaud ... 12 MBaud
PROFIBUS DP and DP-V1 to IEC 61158
SEW_6007.GSD
Not yet assigned
DeviceNet connection
X30D:1 ... X30D:5
•
2-wire bus and 2-wire supply voltage DC 24 V with 5-pole Phoenix terminal
•
Pin assignment according to DeviceNet specification
Communication protocol
Master/slave connection set according to DeviceNet specification version 2.0
Number of process data
words
•
Programmable via IEC function (0 ... 64 process data words)
•
A parameter channel can be used as option in addition to the process data words.
Baud rate
125, 250 or 500 kBaud, can be set using DIP switches 2
6
and 2
7
Bus cable length
For thick cable according to DeviceNet specification 2.0 appendix B:
•
500 m at 125 kBaud
•
250 m at 250 kBaud
•
100 m at 500 kBaud
Transmission level
ISO 11 98 - 24 V
MAC ID
0 ... 63, can be set using DIP switch2
0
... 2
5
Max. 64 stations
P
i
f
kVA
Hz
n
Содержание DHE41B
Страница 2: ...SEW EURODRIVE Driving the world ...
Страница 71: ...SEW EURODRIVE Driving the world ...