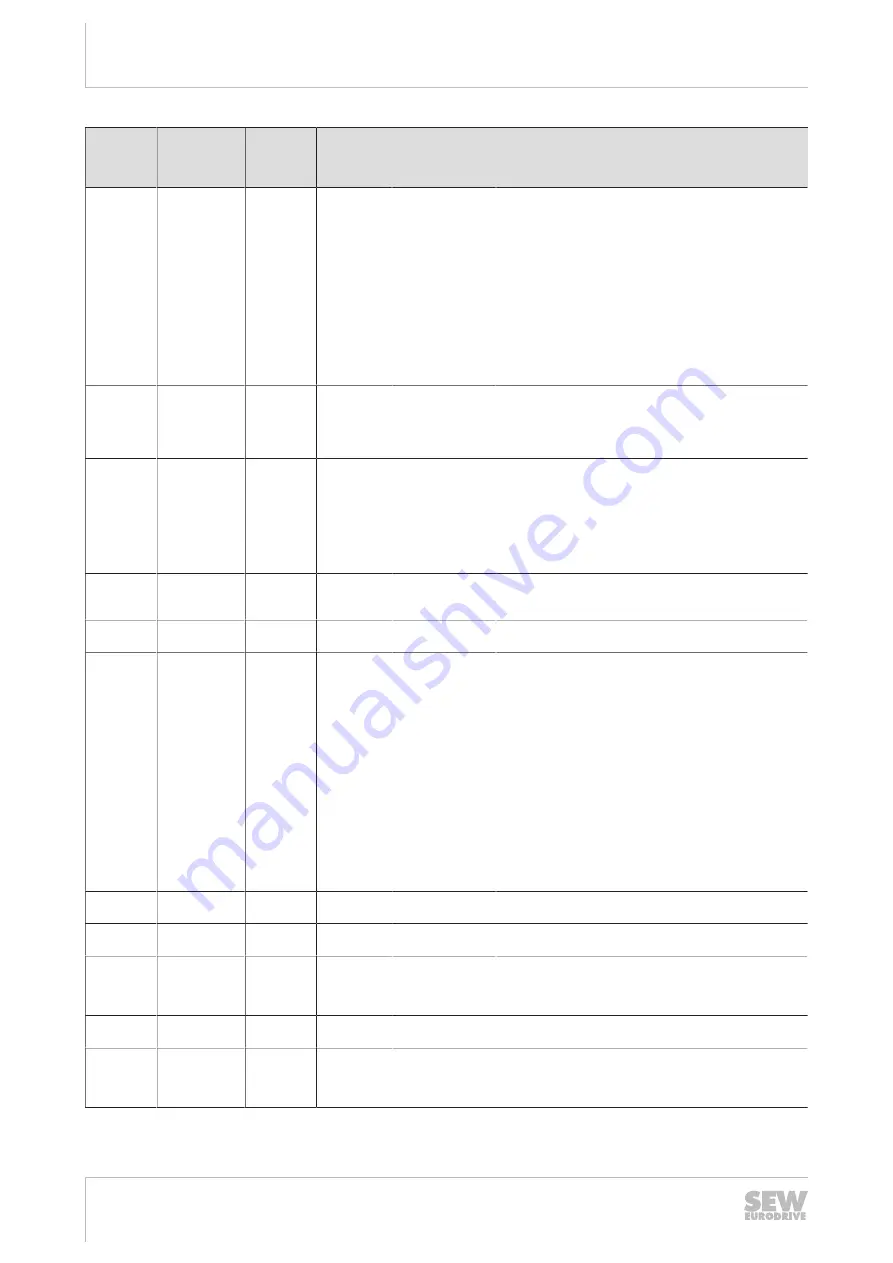
6
Operation
Error list
Compact Operating Instructions – MOVITRAC
®
LTP-B
44
Code (in-
verter dis-
play)
Code
(MotionStudio
in P0-13)
Error code
status
word
if Bit5 = 1
CANopen
emergency
code
Meaning
Measure
O-Volt
06
0x07
0x3206
DC link over-
voltage
The error occurs if a high flywheel load or overhauling
load is connected, and the excess regenerative energy is
transferred back to the inverter.
If a fault occurs while stopping or during deceleration, in-
crease the deceleration ramp time
P1-04
or connect a
suitable braking resistor to the inverter.
The proportional gain in
P4-03
is reduced in vector mode.
In PID control mode, ensure that the ramps are active by
reducing
P3-11
.
Additionally check if the supply voltage is within the speci-
fied range.
Note: The value of the DC bus voltage can be displayed
in
P0-20
. A history log is saved in parameter
P0-36
in
256 ms intervals prior to a switch off with error.
OI-b
01
0x04
0x2301
Brake channel
overcurrent,
braking resistor
overload
Make sure that the connected braking resistor does not
fall below the minimum value approved for the inverter
(see technical data). Check the braking resistor and the
wiring for possible short-circuits. See also fault reset
delay for O-I and hO-I errors.
OL-br
02
0x04
0x1002
Braking resistor
overload
The software detected an overload at the braking resistor
and switches off to protect the resistor. Make sure that the
braking resistor is operated within the planned parame-
ters before performing any changes to the parameters or
the system. To reduce the load at the resistor, increase
the deceleration time, reduce the loads mass moment of
inertia, or connect additional braking resistors in parallel.
Note the minimum resistor values for the inverter in use.
OF-01
60
0x1C
0x103C
Internal connec-
tion to option
module error.
Check if all optional fieldbus cards correspond to the
same fieldbus type. Contact SEW‑EURODRIVE Service.
OF-02
61
0x1C
0x103D
Option module
fault
Contact SEW‑EURODRIVE Service.
Out-F
26
0x52
0x101A
Inverter output
stage error
• Motor phase failure detection: One or more motor
phases were disconnected at the inverter output.
Check the motor lead.
• Check the EMC-compliant cabling of any external con-
trol cables. Use shielded cables.
• As a test, apply use the internal 24 V supply directly to
the digital inputs, to rule out errors in the signal cable.
• As a test, use the internal 24 V supply directly at the
STO inputs to exclude malfunctions at the STO circuit.
• The safety relay at the STO inputs must not send
pulsed signals.
• Check STO for correct wiring.
• As a test, disconnect the temperature sensor to rule out
errors in the sensor cable.
• As a test, disconnect the motor cable from the inverter
to rule out errors originating in the inverter.
• Contact SEW‑EURODRIVE Service.
P-LOSS
14
0x06
0x310E
Input phase failure An input phase has been separated or interrupted at an
inverter planned for a 3-phase supply.
P-dEF
10
0x09
0x100A
Factory settings
are restored.
Ph-Ib
Unequal voltage
on the input
phases
• Check the device input voltage.
• Check the values in
P0-22, P0-23, P0-24
.
The values may deviate by a maximum ±10%. Use an in-
put choke if required.
Ph-SEq
45
0x51
Input phases
swapped
The inverter requires the correct input phase sequence
for controlling the fan. Swap any two input phases.
PS-trP
05
0xC8
0x1005
Output stage error
(IGBT self-protec-
tion in case of
overload)
See error
O-I
.
26879778/EN – 03/2021
Содержание MOVITRAC LTP-B
Страница 2: ...SEW EURODRIVE Driving the world...
Страница 47: ......