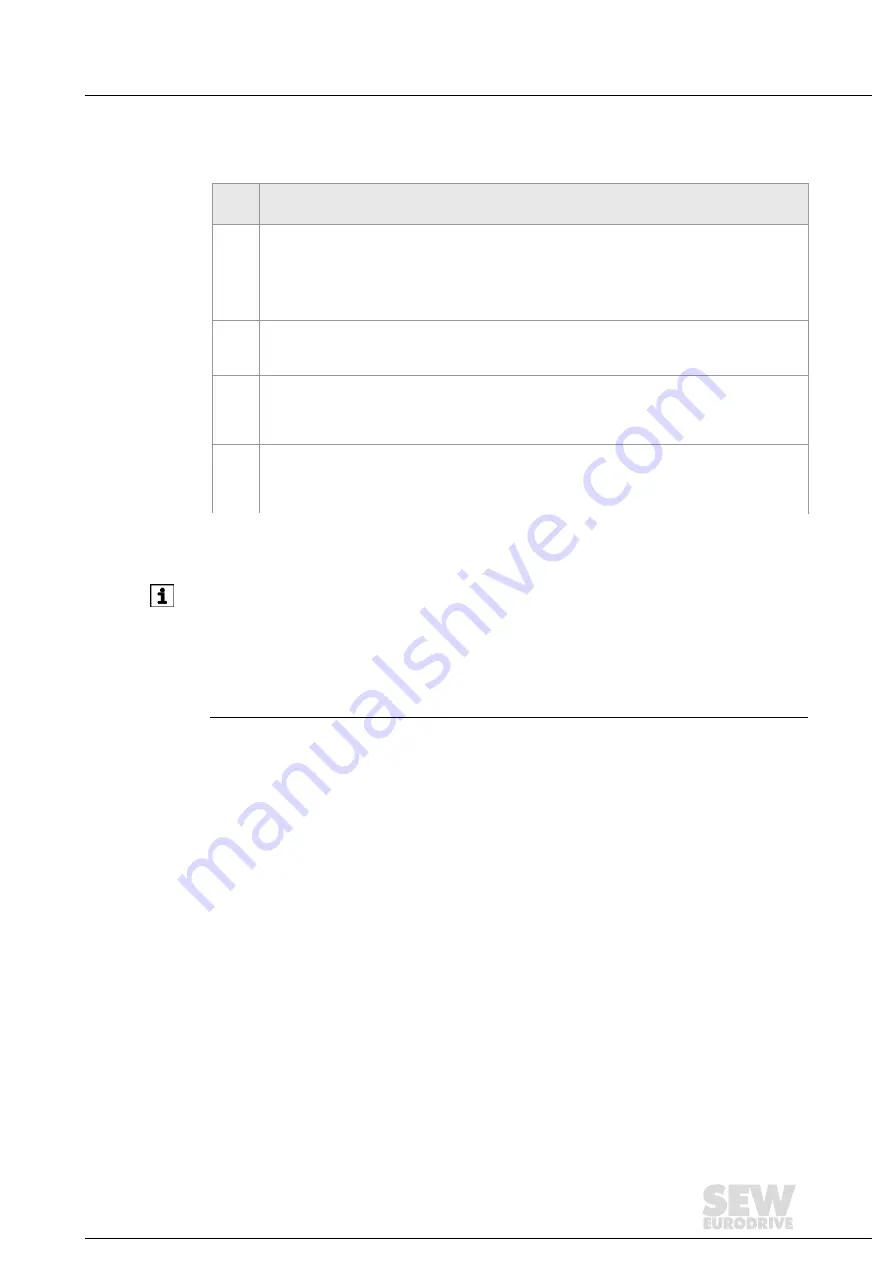
ECShell engineering software
Manual
– ECC-DFC field bus controller
65
The following table describes the available braking methods for motor rollers:
Method
Description
Normal Standard dynamic braking
– the motor roller power circuit in the ECC-DFC is connected internally
during the motor stop sequence in order to supply backwards-directed energy so that the rotor is
braked. If the ECC-DFC determines that the motor has been stopped, the winding current to the motor
roller is shut off completely. This is the industrial standard braking method for motor rollers and the ex
works presetting for all zones by the auto configuration procedure
Free
The motor roller power circuit in the ECC-DFC is interrupted internally, meaning that the rotor can
rotate freely (“free spin”) until its mechanical load brings it to a standstill.
Servo
Brake 1
If a zone is to be stopped, the ECC-DFC uses the Hall sensors of the motor roller to determine the
position of the rotor and feeds current into the motor windings in order to maintain the rotor position.
Servo brake 1 uses 2 of its power transistors for feeding in current.
Servo
Brake 2
If a zone is to be stopped, the ECC-DFC uses the Hall sensors of the motor roller to determine the
position of the rotor and feeds current into the motor windings in order to maintain the rotor position.
Servo brake 2 uses 3 of its power transistors for feeding in current.
INFORMATION
The operating principle of servo brake 1 and servo brake 2 is identical. Servo
brake 2 uses more power and provides a greater holding torque. The use of ad-
ditional current by servo 2 means that there is a risk of heat build-up. If servo
brake 1 provides sufficient holding torque for the application, it is advisable to
prefer this method for servo brake 2. Servo brake 2 should only be used if servo
brake 1 does not supply sufficient holding torque for the application.
Speed
The speed is set in meters per second (m/s). The ECR motor roller receives data
regarding its gear step-down ratio and the roller diameter, which can be read
from the ECC-DFC. The ECShell engineering software then uses this information
to display whether the speed that you enter is permissible for the roller that is
connected.
The motor roller gear step-down can be determined from the part number of the
motor roller, which is displayed when you move the mouse over the module diag-
nosis window. Further information about determining the nominal speed and the
permissible speed range for a certain part number can be found in the ECDriveS
®
catalog.
Содержание ECDriveS ECC-DFC
Страница 2: ...SEW EURODRIVE Driving the world ...
Страница 73: ...ECShell engineering software Manual ECC DFC field bus controller 73 ...
Страница 89: ...Appendix A Dimensions and Installation Instructions Manual ECC DFC field bus controller 89 Dimensions in mm ...
Страница 94: ......
Страница 95: ......