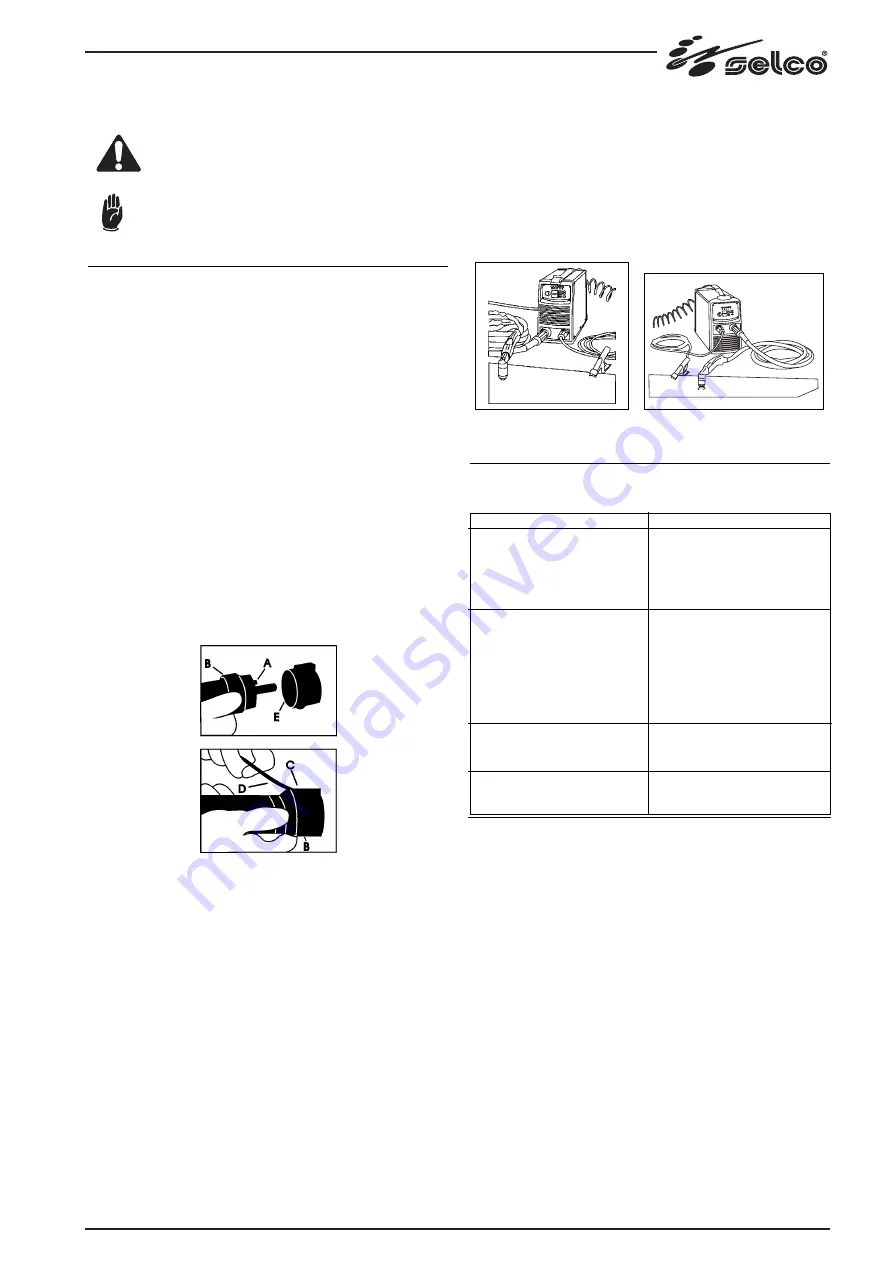
Description of operation of the power sources
11
4.6.2 Connecting the equipment components
Keep to the safety regulations contalned in sec-
tion “4.1SAFETY”.
Connect the componente carefully, in order to
avoid power losses.
4.7 SETTING UP
For installation of the system, follow the instructions below:
1. Place the generator in a dry, clean place with suitable ventila-
tion.
2. Connect up the compressed air supply with a 1/4 inch to the
air inlet P1 in the filter unit F (Fig.2). The pressure must ensure
at least 5 bars with a flow rate of at least 200 litres a minute.
Securely connect the earth cable connector to the generator as
shown in figure 4.
3. Position the earthing clamp onto the piece to be cut, ensuring
that it makes a good electric connection (Fig. 4).
4. Check that all the components of the torch are present and cor-
rectly fitted and connect the torch fitting to the connector on
the generator as shown in figure 3.
Insert the male fitting (torch side) into the corresponding fema-
le fitting (machine side). Align the locating tooth (A) on the hou-
sing and insert the ring nut (B) which must be compatible.
To permit screw-tightening of the ring nut (B), the tool provided
(D) must be first inserted and pressed into the hole (C) in order
to release the anti-rotation lock. This operation must be perfor-
med until the ring nut has been completely tightened. To di-
sconnect the torch, first release the anti-rotation lock by inser-
ting the tool provided (D) into the hole (C).
Fig. 3
5. Switch on the system, ensuring the LED's are working cor-
rectly and some display.
If operating faults occur in the generator it will be inhibited
until normal operating conditions are restored. Press the gas
test pushbutton (T2 in Fig 1) in order to remove residual
impurities from the compressed air circuit, then lift and turn
the knob to adjust the pressure (F1 Fig.2) until the display D2
shows a pressure reading of 5 bars (carry out the operation
keeping the gas test button pressed down, so as to make the
adjustment with air circulating in the piping).
6. Set the value of the cutting current with the potentiometer,
keeping in mind the thickness to be dealt with.
7. Press for a moment the torch button so as to generate the
pilot arc; release the control, checking the machine is cor-
rectly operating with the display panel. It is advisable not to
keep the arc lit to no purpose without making contact, so as
to prevent wear on the electrode and the nozzle. If you con-
tinue to use it like this the apparatus itself will turn off the
pilot light after about 6 seconds.
In the case where a fault is found during the above phases,
check the LED's, the display and if necessary consult the
chapter "Possible electrical faults" in the manual.
Fig. 4
4.8 PROBLEMS - CAUSES
4.8.1 Possible cutting defects
Fault
Insufficient penetration
The cutting arc goes out
Substantial burr formation
Nozzle overheating
Cause
- Cutting speed too high
- Current set too low
- Earth clamp with inefficient
contact
- Thickness of piece excessive
- Electrode, nozzle or diffuser
worn
- Air pressure too high
- Cutting speed too low
- Insufficient air flow
- Defective pressure switch
- Supply voltage too low
- Inadequate air pressure
- Cutting speed too low
- Nozzle eroded
- Electrode eroded
- Insufficient air quantity
Содержание Genesis 90
Страница 1: ...REPAIRS MANUAL Genesis 90 E N G L I S H...
Страница 17: ...6 WIRING AND CONNECTION DIAGRAM 6 1 Genesis 90...
Страница 19: ...18 PC boards location 7 PC BOARDS LOCATION...
Страница 20: ...PC boards location 19...
Страница 24: ...8 3 Thermal devices connectors locations Description of diagnostic indications 23...
Страница 25: ...24 Description of diagnostic indications...
Страница 45: ...11 AVAILABLE SPARE PARTS 44 Available spare parts 56 01 090 GENESIS 90...