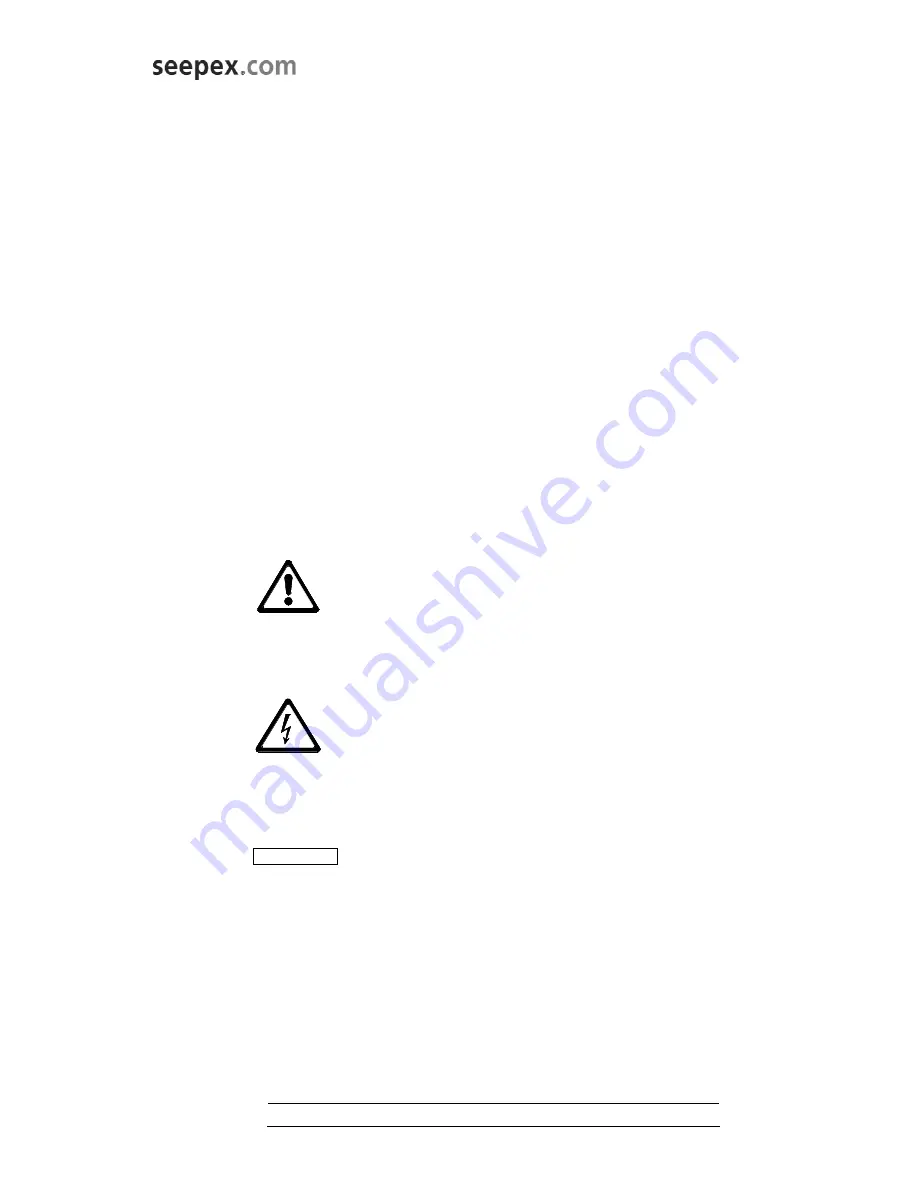
Safety
Ausgabe
issue
B / 21.04.1999
Dokument
document
OM.SAF.01e
Blatt
sheet
1 (2)
2.0
Safety
These operating instructions contain basic require-
ments to be observed during the installation, opera-
tion and maintenance of the machine. Therefore, the
instructions must be read by the mechanical fitter and
by the technical personnel/operator responsible for
the machine prior to assembly and commissioning,
and kept available at the operating site of the
machine/plant at all times.
Compliance is required not only with the general
safety instructions given in this section but also with
the detailed instructions, e.g. for private usage, given
under the other main headings in these operating
instructions.
2.1
Labeling of Advice in the Operating Instructions
In these operating instructions safety advice whose
non-observance could lead to danger for life or limb is
labeled with the following general hazard symbol:
safety symbol acc. to ISO 3864 - B.3.1
Warnings regarding electric power are labeled with:
safety symbol acc. to ISO 3864 - B.3.6
Safety instructions whose non-observance could
jeopardize the machine and its functions are labeled
by the word
CAUTION
Always comply with instructions mounted directly on
the machine, e.g.
- rotational direction arrow
- fluid connection indicators
and ensure that the information remains legible.
2.2
Personnel Qualifications and Training
Personnel charged with operation, maintenance,
inspection and assembly must be in possession
of the appropriate qualifications for the tasks.
The company operating the machine must define
exact areas of responsibility, accountabilities and
personnel supervision schemes. Personnel lacking
the required skills and knowledge must receive
training and instruction. If necessary, the opera-ting
company may commission the manufacturer/
supplier to conduct these training courses. Further-
more, the operating company must ensure that the
personnel fully understand the contents of the
operating instructions.
2.3
Dangers Resulting from Failure to Observe
Safety Instructions
Failure to comply with the safety instructions may
lead to hazards to life and limb as well as dangers
for the environment and the machine. Non-obser-
vance of safety instructions can invalidate the right of
claim to damages.
The following are just some
examples
of possible
dangers resulting from failure to comply with the
safety instructions:
- Failure of important machine/plant functions
- Failure of prescribed methods of service and
maintenance
- Danger to life and limb due to electrical,
mechanical and chemical influences
- Danger to the environment due to the leakage
of hazardous substances
2.4
Safety-conscious Working
Always comply with the safety instructions listed in
this document, the existing national accident
prevention regulations and any company-internal
work, operating and safety rules.
6
Содержание BW 10
Страница 26: ......
Страница 27: ......
Страница 28: ......
Страница 30: ......
Страница 32: ......
Страница 63: ......
Страница 65: ...Section 1 General Information ii Table of Contents MN400 ...
Страница 79: ...3 6 Maintenance Troubleshooting MN400 ...
Страница 80: ...Baldor District Offices Baldor District Offices Baldor District Offices ...
Страница 82: ......
Страница 84: ......
Страница 85: ...Meadowbank mining Corp ACP 700R Technical Data Sheet Reference NC01 DOSING PUMP ...
Страница 86: ......
Страница 111: ......
Страница 112: ......
Страница 113: ......
Страница 121: ......
Страница 122: ......
Страница 123: ......
Страница 124: ......
Страница 158: ...BIM 1010 2005 03 6 www nord com ...
Страница 162: ...BIM 1010 2005 03 10 www nord com PARTS LIST ...
Страница 163: ...BIM 1010 2005 03 11 www nord com NOTES ...
Страница 180: ......
Страница 181: ......
Страница 186: ......