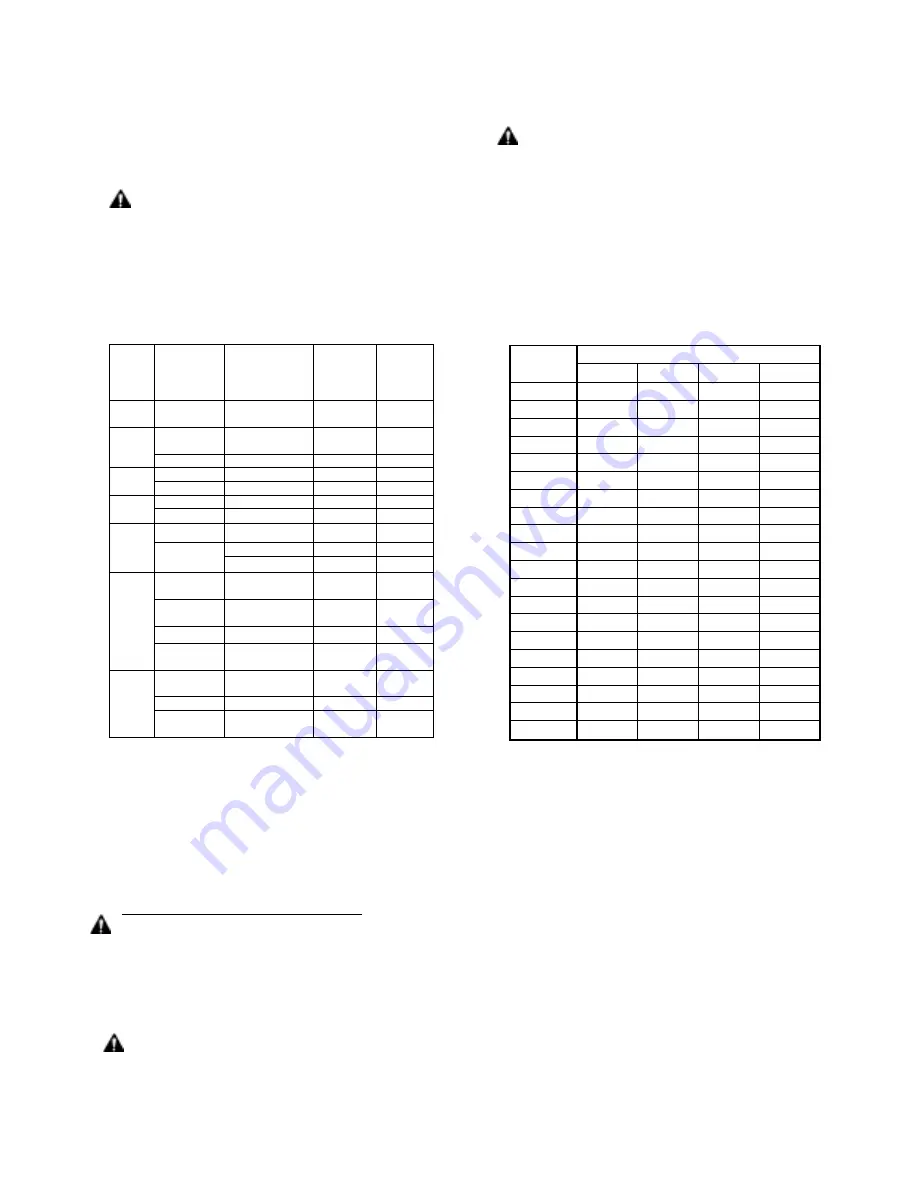
mounting a rigid base (footed) motor vertically is the responsibility of
the installer.
VERTICAL SHAFT DOWN:
Most standard horizontal motors thru
449 Fr. (excluding brake motors) can be mounted in a vertical shaft
down orientation. For vertical brake motors see section 3.3.6.2.
VERTICAL SHAFT UP:
WARNING:
HAZARDOUS LOCATIONS VERTICAL
MOUNT:
Hazardous locations motors must
NOT
be mounted
vertically shaft up without approval by the motor manufacturer.
Without proper retaining provisions the rotor may move axially and
contact components, creating a spark hazard.
Belted or Radial Load when mounted vertically
: The
following frame sizes / constructions with applied (axial) down
loads within the limit stated are acceptable when mounted vertical
shaft up.
Table 3-1 Belted or Radial Load Applications (All speeds)
Frame
Size
Enclosure
Construction
Shaft Up
OK
Max
Applied
Down
Load
3
56
TEFC &
ODP
Steel
Yes
25 lbs
TEFC
Steel & Cast
Iron
Yes
25 lbs
140
ODP
Steel
Yes
25 lbs
TEFC
All
Yes
35 lbs
180
ODP
Steel
Yes
35 lbs
TEFC
All
Yes
40 lbs
210
ODP
Steel
Yes
40 lbs
TEFC
All
Yes
40 lbs
Steel
Yes
40 lbs
250
ODP
Cast Iron
No
2
N/A
320 TTFC
models
Cast Iron
Eng
1
N/A
All Other
TEFC
Cast Iron &
Aluminum
Yes
30 lbs
ODP
Cast Iron
No
2
N/A
280-320
TEFC &
ODP
Steel
Build Up
Only
4
N/A
TEFC
Cast Iron
Build Up
Only
4
N/A
ODP
Cast Iron
No
2
N/A
360 &
Up
TEFC &
ODP
Steel
Build Up
Only
4
N/A
Notes:
1
For TEFC model numbers beginning with 324TTFC or 326TTFC
consult the motor manufacturer to determine if a build up motor
is required.
2 The max applied down load is any applied load external to the
motor, including such things as sheave weight, fan loads, axial
belt force, pump load, etc. If the application is direct drive with
no applied radial load, consult the motor manufacturer.
3 ”Build-up only”, refers to motors that are specifically ordered
and built for shaft up applications. It does not imply that all build-
up motors are suitable for shaft up applications.
3.3
APPLICATION ASSEMBLY TO MOTOR:
CAUTION:
EQUIPMENT DAMAGE:
Do not connect or couple motor to load until correct rotational direction
is established.
3.3.1
GENERAL: PROPER ALIGNMENT
of the motor and
driven equipment minimizes vibration levels, maximizes bearing life,
and extends the overall life of the machinery. Consult the drive or
equipment manufacturer for more information.
CAUTION:
BEARING FAILURE
During assembly do NOT force components onto the shaft. Striking
or hammering the component may result in bearing damage.
3.3.2
DIRECT COUPLING:
Use flexible couplings if possible.
For applications that apply radial, axial or moment loading on the
motor shaft see section 3.3.3.
CAUTION:
BEARING FAILURE
Unless approved by the motor manufacturer do
NOT
direct couple a
vertical shaft up or roller bearing motor. Direct coupling a vertical
shaft up motor or a motor with a roller bearing may result in bearing
damage.
3.3.3
DIRECT CONNECTED:
Radial loading for direct
connected equipment (gears, fans etc.) must be approved by the
motor manufacturer unless within the maximum overhung load limits
(Table 3-2). Combined loading (axial, radial and/or moments) must
be approved by motor manufacturer. For belted loads see section
3.3.4.
Table 3-2 Maximum Radial Load (lbf) @ Middle of the Shaft
Extension Length
Motor Rated RPM
Frame
Number
3600
1800
1200
900
143T
106
166
193
210
145T
109
170
199
218
182T
187
230
261
287
184T
193
237
273
301
213T
319
317
470
510
215T
327
320
480
533
254T
500
631
729
793
256T
510
631
736
820
284T
-
866
990
1100
286T
-
871
1005
1107
324T
-
950
1100
1215
326T
-
950
1113
1230
364T
-
1078
1365
1515
365T
-
1078
1380
1540
404T
-
1388
1590
1762
405T
-
1400
1610
1780
444T
-
1580
1795
2005
445T
-
1520
1795
1985
447T
-
1455
1765
1985
449T
-
1640
1885
2130
Values based on 26,280 hrs B-10 Life
For “End of Shaft” Load multiply value by 0.88
To convert from lbf to N multiply value by 4.4482.
3.3.4
BELTED:
The goal of any belted system is to efficiently transmit the required
torque while minimizing the loads on the bearings and shafts of the
motor and driven equipment. This can be accomplished by following
four basic guidelines:
1.
Use the largest practical sheave diameter.
2.
Use the fewest number of belts possible.
3.
Keep sheaves as close as possible to support bearings.
4.
Tension the belts to the lowest tension that will still transmit the
required torque without slipping. It is normal for V-belts to
squeal initially when line starting a motor
3.3.4.1
Sheave Diameter Guidelines:
In general, smaller sheaves produce greater shaft stress and shaft
deflection due to increased belt tension. See Table 3-3 for
recommended minimum sheave diameters. Using larger sheaves
increases the contact with belts which reduces the number of belts
required. It also increases the belt speed, resulting in higher system
efficiencies. When selecting sheaves, do not exceed the
manufacturer's recommended maximum belt speed, typically 6,500
feet per minute for cast iron sheaves. Determine belt speed by the
following formula:
Содержание BW 10
Страница 26: ......
Страница 27: ......
Страница 28: ......
Страница 30: ......
Страница 32: ......
Страница 63: ......
Страница 65: ...Section 1 General Information ii Table of Contents MN400 ...
Страница 79: ...3 6 Maintenance Troubleshooting MN400 ...
Страница 80: ...Baldor District Offices Baldor District Offices Baldor District Offices ...
Страница 82: ......
Страница 84: ......
Страница 85: ...Meadowbank mining Corp ACP 700R Technical Data Sheet Reference NC01 DOSING PUMP ...
Страница 86: ......
Страница 111: ......
Страница 112: ......
Страница 113: ......
Страница 121: ......
Страница 122: ......
Страница 123: ......
Страница 124: ......
Страница 158: ...BIM 1010 2005 03 6 www nord com ...
Страница 162: ...BIM 1010 2005 03 10 www nord com PARTS LIST ...
Страница 163: ...BIM 1010 2005 03 11 www nord com NOTES ...
Страница 180: ......
Страница 181: ......
Страница 186: ......