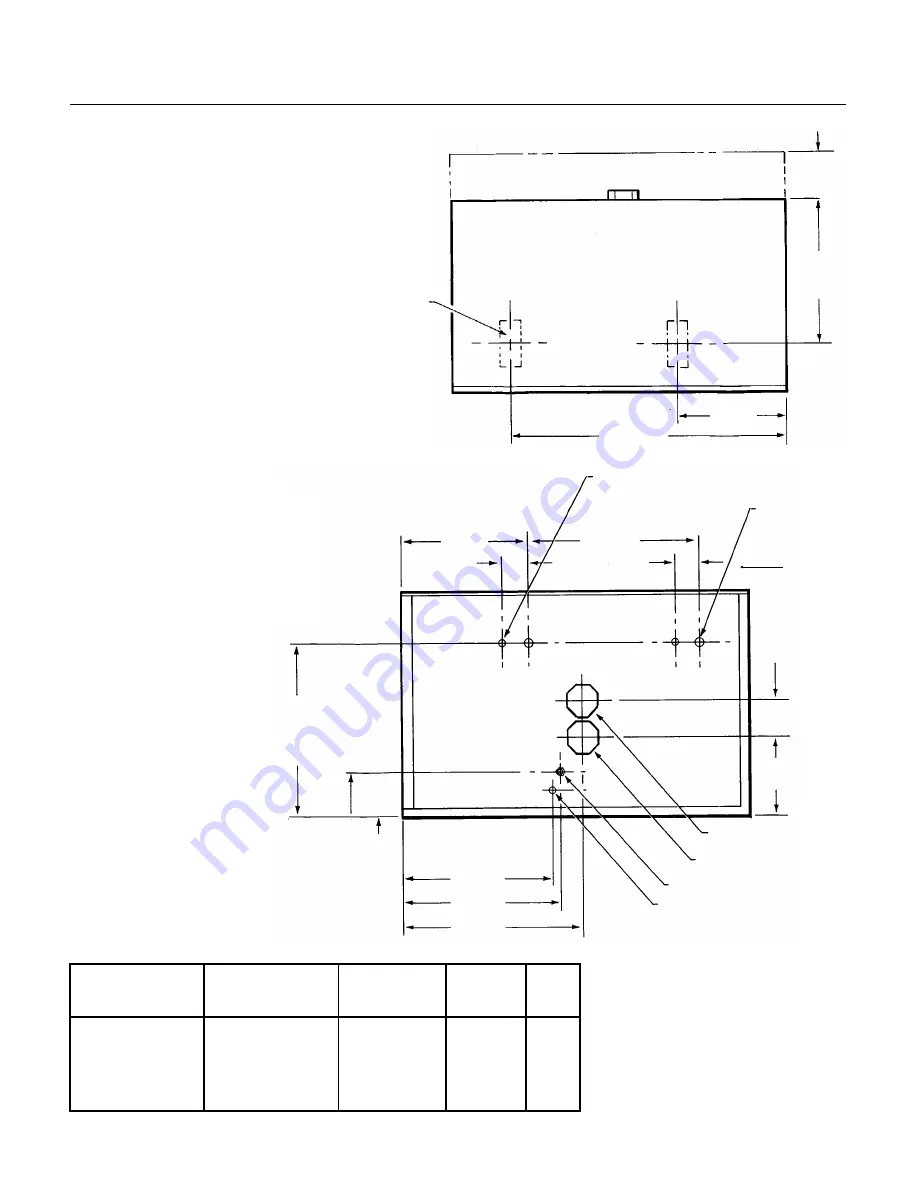
FOR THE INSTALLER
These machines are designed to fit
the following Scotsman storage
bins:
••
B90 and extensions, with bin
top KBT18.
••
BH800 no bin top needed.
••
BH900 using bin top KBT14.
When installing a new system,
check to be sure that you have
everything you need before
beginning:
••
Correct Bin
••
Correct Ice Machine
••
Correct Bin Top
••
All kits, legs, and information
required for the specific job.
BACK VIEW
Liquid Line
Connection
(right system)
Discharge Line
Connection
(left system)
Remote Condenser
Junction Box
Electrical Inlet
Water Inlet 3/8" Flare
Drain 3/4" FPT
21.66"
3"
5.25"
20.84"
Allow 6"
above
machine for
service.
15.53"
21"
3.1"
3.1"
4.5"
9.43"
17.8"
18.8"
There are two separate ice making
and refrigeration systems in this
model. The liquid and discharge
lines from each system must go
to separate circuits in one remote
condenser (RCE502).
*
Model
Number
FME2400RE-32A
FME2400RE-3A
NME1850RE-32A
NME1850RE-3A
Dimensions
(w/o bin)
H X W X D
27" x 42" x 24"
same
same
same
Basic
Electrical
208-230/60/1
208-230/60/3
208-230/60/1
208-230/60/3
Ice
Type
FLAKE
same
Nugget
same
Cond.
Type
R/Air
R/Air
R/Air
R/Air
TOP VIEW
Allow 6" of space behind the machine
for utility connections.
Ice Chute
6.7" x 6.2"
34.84"
13.84"
18.28"
SPECIFICATIONS: ICE MAKER
The Standard Finish is Enamel -
Sandalwood. There is an optional
stainless steel panel kit,
SPKFM42 available to convert
the unit to Stainless Steel. It is
field installed.
NME1850R & FME2400R
February 1995
Page 2