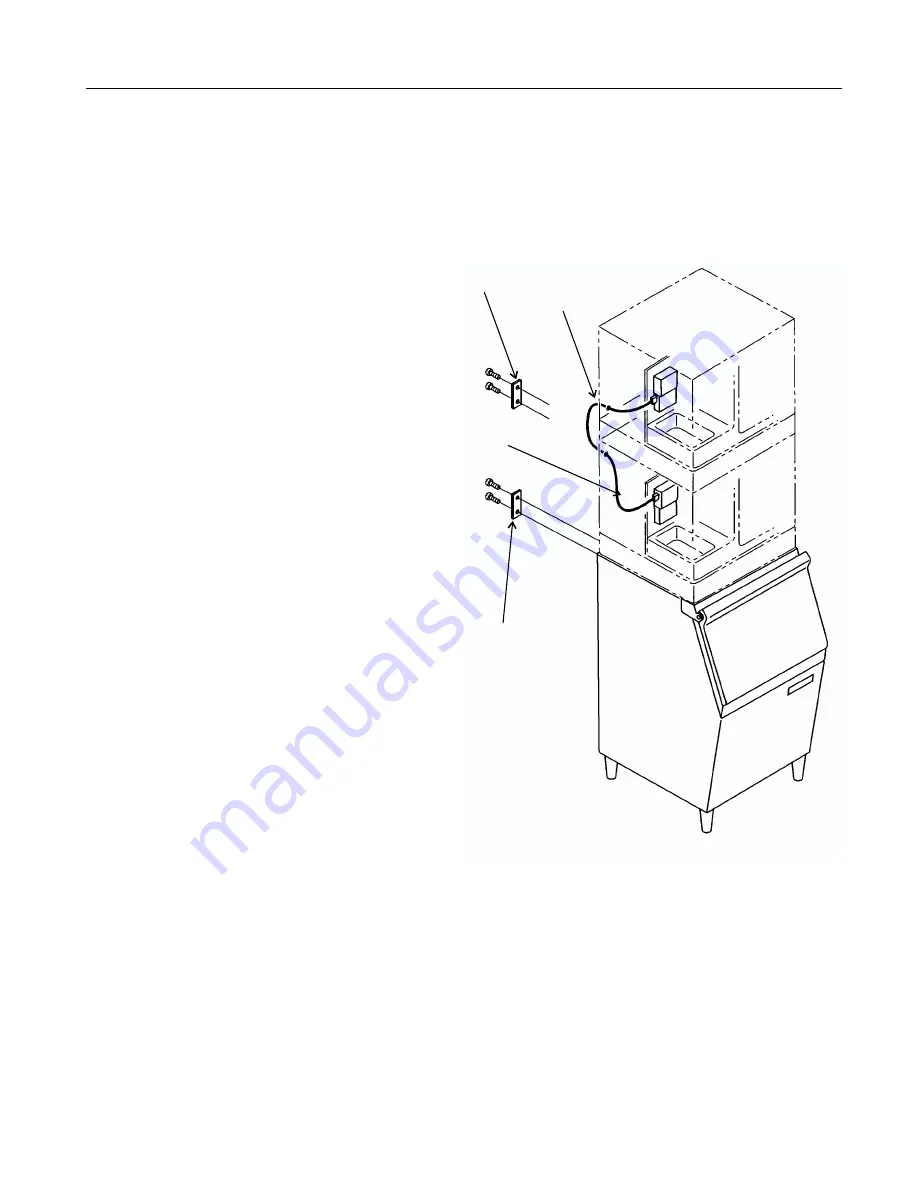
Stacking:
Models CME256, CME506, CME656 and CME806
may be stacked together in any combination. Use
kit number KSCME6-30.
1. Remove the front, left side and top panels
from the bottom machine. Discard the top
panel.
2. Remove the front and left side panels
from the top machine.
3. Place the upper machine onto the lower
machine. Check that the tabs on the top of
the freezing compartment in the lower
machine engage the slot in the base of the
upper machine (around the cube port).
4. Fasten the upper cabinet to the lower
cabinet with the hardware (two metal straps
and four bolts) provided with the machine.
5. Knock out 1 hole in the upper left (viewed
from the front) corner of the lower unit’s
back panel. Knock out the hole in the lower
left (viewed from the front) corner of the
upper unit’s back panel.
6. Position the strain reliefs over the
wrapped portion of the stacking kit wire
harness.
Route the Stacking Kit Wire Harness from
the back to the top and bottom machines
thru the holes made in step 5.
The harness
is marked which end goes to which
machine
. Push the strain reliefs into place
from the back of the machines.
Follow local electrical codes for 24 volt wire.
In the lower unit, route the wire behind the
suction line and thru the snap bushing just
below the AutoIQ Controller. Tape any
excess wire to the insulated suction line.
In the upper unit, route the harness thru the
snap bushing just below the Controller.
Plug one end into each Controller connection
number 7.
7. Place insulation pad from the kit over the
reservoir drain tubing in the upper machine. Make
certain that the insulation is in contact with the
tubing.
8. Return all panels to their normal places.
CME506R, 656R, 806R: AutoIQ Cubers
January 2000
Page 5
Stacking Two Ice Machines Together
Mounting
Strap
Strain
Relief
Stacking Kit Wire
Harness
Mounting
Strap
Содержание CME506R
Страница 42: ......