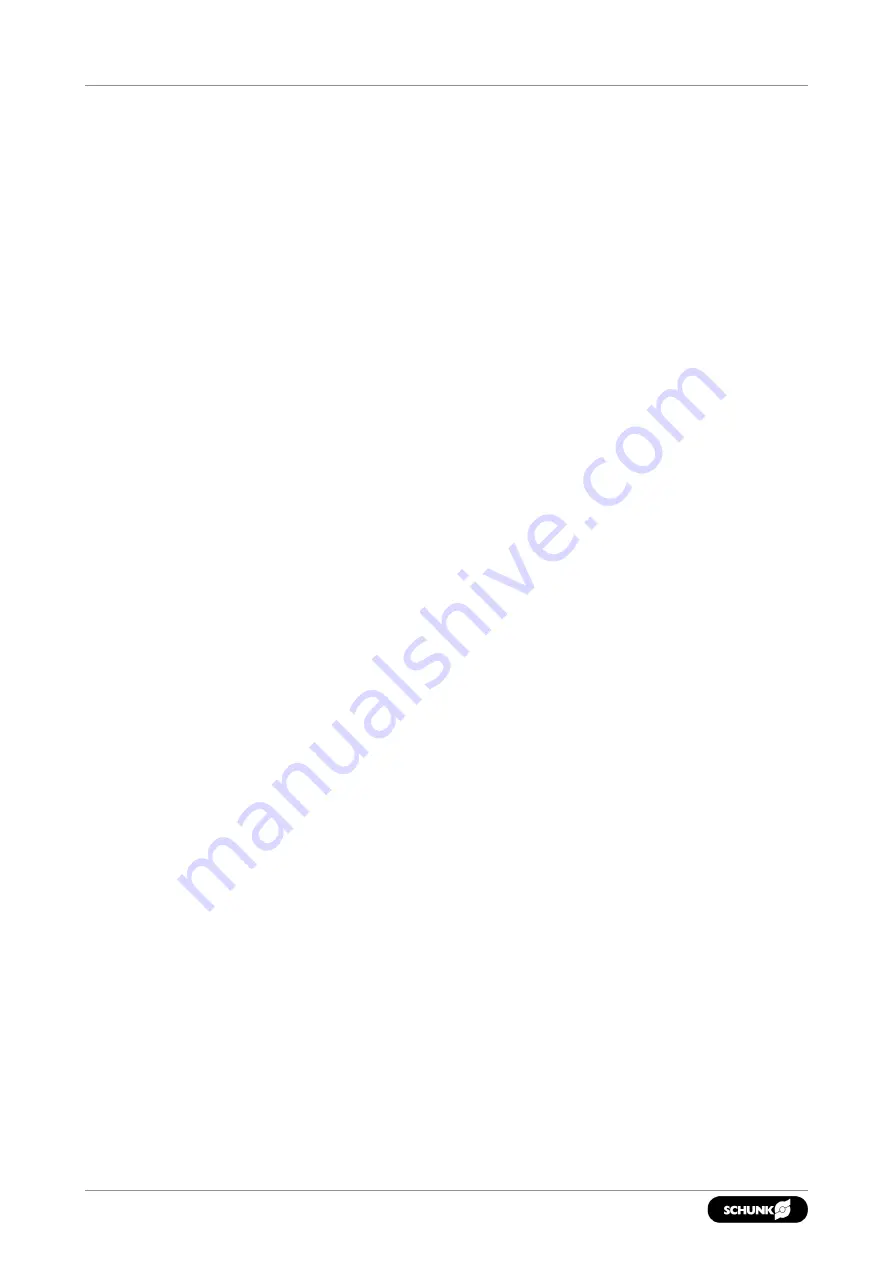
Assembly and connection
20
01.00 | KRP3, KRP3-LH | TANDEM Clamping Block | en | 1514176
• Do not open the connections on the front of the clamping force
block (
I, II
), or seal them with suitable dummy plugs (M5 or
G1/8").
• Insert the clamping sleeves from the accessory kit into the
centering holes on the base plate.
• Remove the center plugs from the base plate (internal air feed-
through
III, IV
) and insert the O-rings from the accessory kit into
the recesses for the air feed-throughs.
• Mount the clamping force block onto the base plate.
NOTE:
The TANDEM base plates do not have a connection possibility for
the inductive proximity switches on the TANDEM clamping force
blocks.
The function for monitoring the jaw position can only be
connected externally. When joining, make sure the air feed-
throughs for the clamping system and the base plate are precisely
aligned.
• Screw the two parts together using the four screws (item 84)
from the accessory kit. In doing so, observe tightening
torques
• Remove the locking screws from the pneumatic connections on
the base plate.
• Connect the diaphragm pressure switch and set the switch to
the required minimum pressure.
NOTE:
All four air connections come sealed on delivery of the clamping
force block. On the base side with set-screws (item 60) and on the
front with locking screws (item 23).
• When using the air purge via connection 5, the sound absorber
(V) must be removed and replaced by a set-screw (item
93).
Requirements for compressed air supply: compressed air,
compressed air quality according to ISO 8573-1: 7:4:4
Unconditioned compressed air contains dust and oil particles and
moisture, all of which can lead to malfunctions or premature wear
in the clamping force block. The oiler should be no more than 2
meters from the coupling point.
The clamping force block has two more base connections (
6/7
) for
direct lubrication through the machine table. These connections
come sealed on delivery with set-screws (item 62).