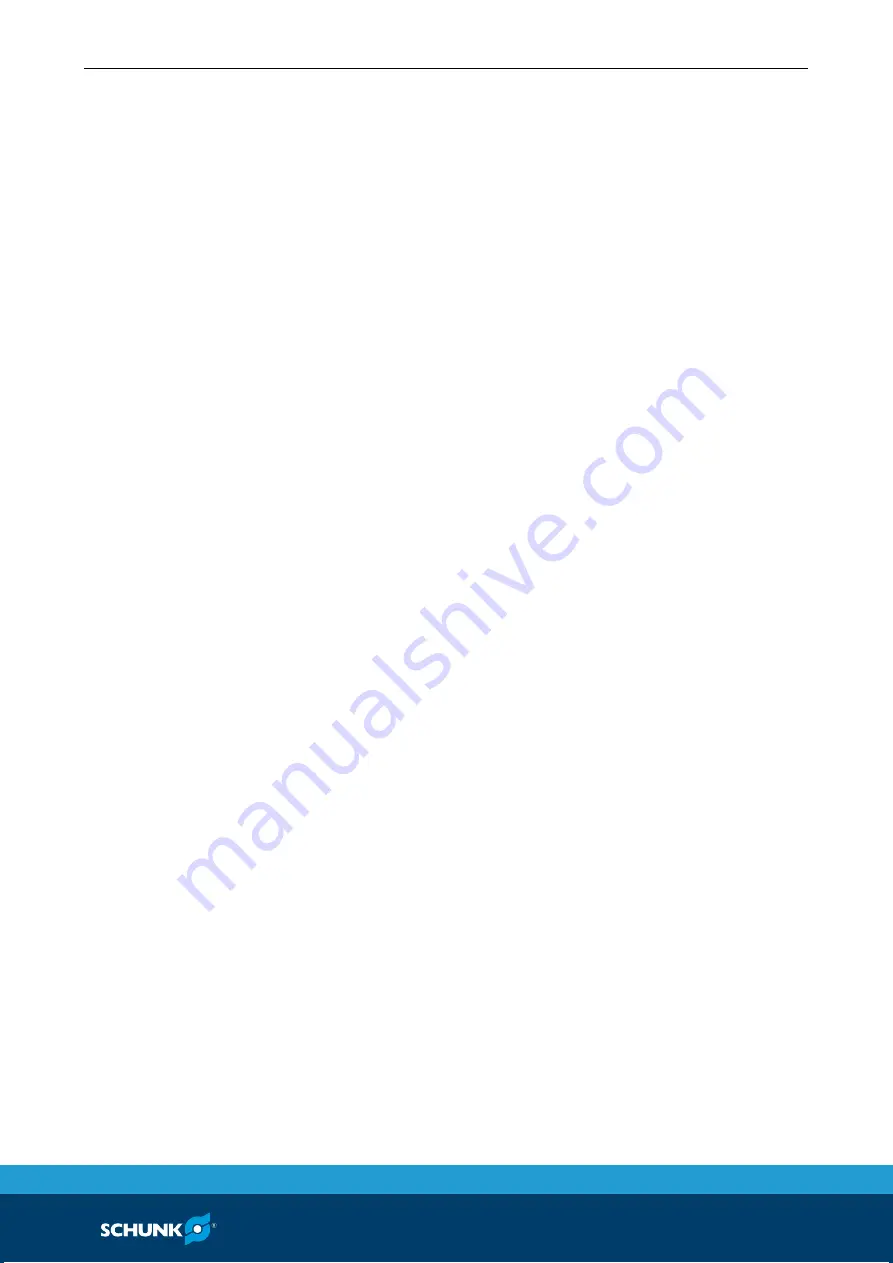
Operational Considerations
01.00|SWS-001 |en
23
3 When the two faces are within the specified No-Touch™ dis-
tance, release the pressure from the Unlock Port and supply
air to the Lock Port
Note:
The SWA will be drawn toward the SWK and coupled.
Air must be maintained on the Lock Port during operation to
assure rigid coupling.
4 A sufficient delay must be programmed between locking valve
actuation and robot motion so that the locking process is
complete before moving the robot.
The fail-safe design prevents the SWA from being released in the
event of air-pressure loss to the Lock Port, thereby increasing safe-
ty and reliability. Positional accuracy may not be maintained dur-
ing air loss, but will be regained once air pressure is re-established
to the Lock Port.
Uncoupling Sequence
1 Position the SWA in the Tool Stand such that there is little or
no contact force between the SWA and Tool Stand.
2 Release air on the Lock Port and apply air to the Unlock Port.
NOTICE! The air will cause the locking mechanism to be re-
leased and the weight of the SWA and attached tooling will
assist in its removal. Tool weight assists in uncoupling if the
Tool is released in the vertical position only.
3 Move the SWK axially away from the SWA.
4 A sufficient delay must be programmed between unlocking
valve actuation and robot motion so that the unlocking
process is complete and the SWA is fully released before mov-
ing the robot.
7.2
Содержание SWS-001
Страница 35: ...Drawings 01 00 SWS 001 en 35 Drawings Tool Changer SWS 001 Tool Changer 11 11 1...
Страница 36: ...Drawings 36 01 00 SWS 001 en quick change head SWK 001...
Страница 37: ...Drawings 01 00 SWS 001 en 37 quick change adapter SWA 001...
Страница 38: ...Drawings 38 01 00 SWS 001 en E04 Electrical Module Electrical Module 11 2...
Страница 40: ...40 01 00 SWS 001 en...