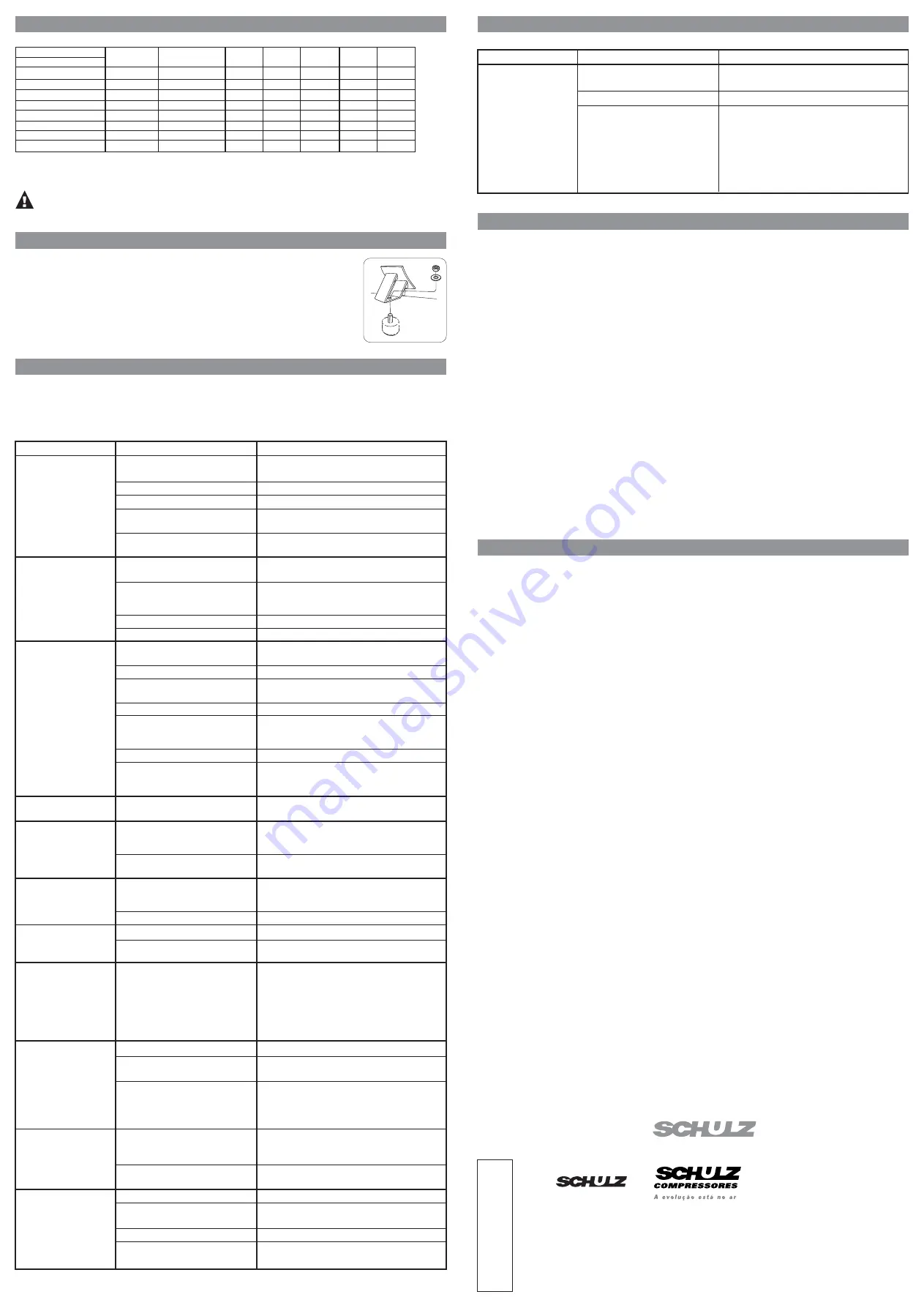
025.0149-0
05
/2009
rev
.0
6
W
rite
here
the
serial
number
of
product:
15) WARRANTY
15) WARRANTY
14) ENVIRONMENTAL GUIDANCE AND RECOMMENDATIONS
14) ENVIRONMENTAL GUIDANCE AND RECOMMENDATIONS
Ó
INFORMACI N TÉCNICA
TECHNICAL INFORMATION
PIEZAS ORIGINALES / ORIGINAL REPLACEMENT PARTS
(55) (47) 3451-6252
(55) (47) 3451-6051
DPTO EXPORT
Phone
Fax
Rua Dona Francisca, 6 901
Fone (55) (47) 3451 6000 Fax (55) (47) 3451 6055
JOINVILLE SC BRASIL
[email protected]
www.schulz.com.br
CEP 89219600
3420 Novis Pointe
Acworth, GA 30101
Phone # (770) 529-4731 / 32 / Fax # (770) 529-4733
[email protected]
www.schulzamerica.com
Schulz of America, Inc.
P E Ç A S
O R I G I N A I S
11) CORRETIVE MAINTENANCE
11) CORRETIVE MAINTENANCE
To assure product SAFETY and RELIABILITY, repairs, maintenance and adjustment should be performed
by
always using identical replacement original parts Schulz.
Schulz Authorized Technical/Distributor
12) VIBRATION BUFFER’S ASSEMBLY
12) VIBRATION BUFFER’S ASSEMBLY
Procedures to installation:
1.
2.
3.
4.
Choose the place to install the product.
Take the compressor from the wooden base and put it on the vibration buffers, as
shown by Figure 15.
The compressor must be leveled and the buffer must be screwed to the tank’s foot.
After the installation, do not push the product to avoid damaging the vibration buffers
(always use a lifting device to move the product).
13) TROUBLESHOOTING GUIDE
13) TROUBLESHOOTING GUIDE
13) TROUBLESHOOTING GUIDE
13) TROUBLESHOOTING GUIDE
This section provides a list of the more frequently encountered malfunctions, their causes and corrective actions.
The operator or maintenance personnel can perform some corrective actions, and others may require the
assistance of a
.
Schulz Authorized Technical/Distributor
PROBLEM
PROBLEM
POSSIBLE CAUSE
POSSIBLE CAUSE
POSSIBLE SOLUTION
POSSIBLE SOLUTION
Voltage drop or electrical supply
is out.
Damaged electric motor.
Tank is full of air.
Check valve does not seal
because of impurities.
Check the installation and/or wait for
the electrical supply stabilization.
Send it to a specialized technician.
Electric motor will start as soon as the
pressure in the tank decreases.
Send the compressor to the nearest
.
Schulz Authorized Technical/Distributor
Motor does not
start or does not restart.
Obs.: Do not insist
to start the motor. Do
it only after you have
discovered and
eliminated the cause
of the problem.
Installation fuse has burned out.
Find out the burning cause (see Table 3).
Motor pulley and/or motor out
of specification.
Filter element clogged.
Air leakage in the compressor.
See Table 1 - Technical Data and make the
necessary adjustments at your
.
Schulz
Authorized Technical/Distributor
Replace it
Re-fasten bolts and/or fittings.
High ambient temperature
(max. 40 C or 104 F).
0
0
Improve local conditions.
Reduce air production
(Pressure gauge keeps
showing a lower
pressure than that of
the job).
The demand is above the
compressor's capacity.
Check the compressor's capacity.
Incorrect speed direction.
See item 3, Start Up Procedure - Chapter 9.
The demand is above the
compressor's capacity.
Check the compressor's capacity.
The compressor unit
overheats.
Filter element clogged.
Replace it.
Motor pulley and/or motor out
of specification.
See Table 1 - Technical Data and make the
necessary adjustments at your
.
Schulz
Authorized Technical/Distributor
Wrong oil or low oil level.
Change oil.
Carbonized valve plate.
Clean it every 1,000 working hours or 9
months at your nearest
.
Schulz Authorized
Technical/Distributor
Deficient or inadequate
electrical supply.
Have a specialized technician check it
Electric motor
overheats.
The oil change did not occur at
the recommended interval .
See item 3, Preventive Maintenance - Chapter
10, the oil change procedures.
Operating in a non-adequate
environment.
Improve local conditions and adjustments
at your
.
Schulz Authorized-
Technical/Distributor
Premature wear of the
compressor unit
internal parts.
Product’s incorrect installation.
Re-install the product in appropriate
place and/or check the buffer use
conditions.
Abnormal vibration
level.
Loose or unaligned belt(s).
Adjust it (them) according to Figures 2 and 3.
Too much dust on the compressor. Clean the compressor externally.
Compressed air high
temperature. If the
compressor operates in
a continuous mode, the
discharge air must be
exhausted outside the
environment
(machine room).
Drain the tank through the drain as
indicated in Figure 8. For your comfort Schulz
S.A., provides an electronic drain, model PS 16,
which is adaptable to the tank exhaust
connection (drain)
and that can be
purchased at Schulz Authorized Technical/
Distributor.
9
Excess water in the tank.
Tank pressure increases
quickly or too frequent
starts (The normal
number of starts is
roughly 6 an hour -
compressors with
pressure switch).
Loose fastening elements.
Loose flywheel/motor pulley
and pulley cover.
Find and re-fasten them.
Re-fasten its.
Abnormal noise
or vibration.
Excessive consumption
of lubricating oil
(Compressors usually
use more oil in the first
200 working hours until
rings are smoothly
adjusted).
Compressor operates
uninterruptedly (models
with pressure switch).
Wrong electrical connection
(Pressure switch is not connected
to the electrical supply).
See Installation - Chapter 8, item 5 - Electrical
connection (Figures 4, 5 and 6).
High ambient temperature
(max. 40 C or 104 F).
0
0
Improve local conditions.
Filter element clogged.
Replace it
Filter element clogged.
Replace it
The demand is above the
compressor's capacity.
Check the compressor capacity.
Schulz S.A., assures this product's first buyer/user a warranty against manufacturing fault that develops
within 1 (one) year (including the legal warranty - first 90 (ninety) days) from date of purchase invoice
issuing.
GENERAL WARRANTY CONDITIONS
A.
C.
D.
E.
F.
G.
WARRANTY TERMINATION
A.
B.
WARNINGS
C.
D.
E.
F.
Note:
The warranty servicing will be made upon purchase invoice presentation.
Parts that are naturally worn out by regular use and that are affected by the installation and the way the product
is used are excluded from this warranty, such as: air filter element, gaskets, valves, rings, cylinders, pistons,
connecting rods, crankshaft, pressure switch, pressure gauge, roller or ball bearings, oil seal, drain plug, oil
level sight, oil level dipstick, drain, valve and belts. Schulz S.A., will only take responsibility on the servicing
expenses of the above mentioned parts if a
detects manufacturing
defects.
This warranty will not apply to cleaning and installation services, adjustment requested by customer,
lubricating oil changes, neither to any damage caused to the product's external parts due to incorrect use,
neglect, modifications, use of inadequate accessories, inadequate use, falls, drillings, use not according to the
instruction manual, electrical connections in the wrong voltage, voltage conversion of the electric motor
inadequate for the compressor or electrical supply nets subject to excessive voltage drops or voltage
overloads.
Representatives or dealers are not authorized to receive a product to send it to a
, take it from there to return it to the client or provide information on Schulz S.A., behalf about the
servicing.
Schulz S.A. or any
will not be responsible for eventual damages or
delays resulting from the non-accomplishment of this clause.
Only approved lubricoolant and original Schulz repair/maintenance parts are used.
This warranty will be considered void in the following situations:
At the end of its validity.
When the product is delivered for servicing to non-authorized shops; signs of violation to its original features
can be noticed; when it is assembled out of the manufacturer standards.
The deadline of a servicing will be shown in the service report, on the date a product is delivered at a
.
Dealers, representatives or
are not authorized to change this Term or
take responsibilities on Schulz S.A.’s behalf.
Schulz S.A., reserves the right to make changes without prior notice.
B.
H.
A.
B.
G.
Any warranty service should be realized exclusively by Schulz Authorized Technical/Distributor.
Schulz Authorized Technical/Distributor
Electric motor and electric key manufacturers assume the warranty of their products if they fail for
manufacturing defects. Defects caused by bad installation are not covered by this warranty.
Distributor of Schulz
Compressor’s
Schulz Authorized Technical/Distributor
Will be excluded of warranty any repair or indemnification of damages occurred during the product transport.
This compressor is supplied according to the customer technical specifications at the time of ordering. It has
specific displacement, pressure and voltage characteristics that cannot be changed, modified or altered in any
way.
Lubrication of your reciprocating piston compressor is fundamental. Maintenance of proper lubricoolant levels
is paramount and has been discussed numerous times in this manual.
Schulz
Authorized Technical/Distributor
It's the purchaser's responsibility to pay for service expenses, which are proved unfounded.
Schulz Authorized Technical/Distributor
Drawings are intended to show component flow and orientation only and are not intended to be a specification
drawing. Specification drawings are available upon request from SCHULZ S.A. only.
The technician will provide service on a first come first served basis.
1. Disposal of Liquid Effluents
2. Draining the Lubricant Oil from the Compressor Unit (Pump)
3. Disposal of Solid Waste (parts in general and product packages)
The presence of liquid effluents or non-treated condensation from tank and separator in rivers, lakes or in other
water receiving bodies may adversely affect the aquatic life and the water quality as well.
The condensation withdrawn from the tank and separator, daily, according to the Preventive Maintenance
Chapter 10, must be kept in a container and/or in an appropriate collecting network for further treatment.
Schulz S.A., recommends that the liquid effluent produced inside the receiver of the compressor or condensed
separator should be adequately treated through processes that aim at protecting the environment and the healthy
quality of life of the population, complying with the country current regulation requirements.
Among the treatment methods available, one may choose the physical-chemical, chemical, and biological ones.
The treatment may be carried out by the company itself or by outsourcing.
The disposal of the lubricant oil coming from the lubricant oil change located either in the crankcase of the piston
compressor must meet technical requirements, as well as the regulation requirements of the current legislation of
the country the product has been exported to.
The generation of solid waste is an important aspect that must be considered by the users when using and
maintaining their piece of equipment. The impacts to the environment may cause meaningful changes in the
quality of the soil, in surface and underground water, and in the population's health, due to the inadequate
disposal of the discarded residues (on streets, water springs, landfills, etc).
Schulz S.A., recommends that the waste arising from the product, from its generation, handling, transportation,
and treatment to its final disposal should the handled carefully. Appropriate handling should consider the
following steps: quantification, qualification, classification, reduction at source, pick-ups and selective pick-ups,
recycling, storage, transport, treatment and final destination.
The disposal of solid waste must be carried out according to the regulation requirements of the current legislation
of the country the product has been exported to.
The demand is above the
compressor capacity.
Check the compressor capacity.
Change oil, see Table 5.
Wrong oil.
Oil leaks.
Check and eliminate it.
High ambient temperature
(max. 40 C or 104 F).
0
0
Improve local conditions.
The oil change did not occur at
the recommended interval .
See item 3, Preventive Maintenance - Chapter
10, Table 4 - oil change intervals.
Lubrificant oil with
unusual color.
Water is mixed with the oil
(milky coloration).
Change the lubricant oil and run your
pressure compressor for 30 min, at a
maximum pressure of 100 psig (7.0 bar).
This will remove any internal condensation
signs inside pump. Afterwards, run the
compressor and allow it to have roughly
6 starts per hour (70% ON and 30% OFF
or unload).
Location
Model
Cylinder
cover
Cylinder cover
center
Cylinder
Flange Cranckase
cover
Flange
cover
Flywheel
CSV 15 MAX
CSL 20 MAX
CSWV 40
MSW 60 MAX
MSWV 40/60 FORT
MSW 80 MAX
25
55
25
29
29
25*-29
29
25*-29
12
12
12
12
-
12
-
12
30
29
30
30
65
65
65
65
25
15
25
30
65
65
65
65
-
-
-
8
15
15
15
15
-
-
-
8
8
8
8
8
25
127
25
127
137
137
137
137
MSV 20/26 MAX
MSV 30/40 MAX
* Cylinder cover AP, Allen screw assembled
TABLE 6 - SCREW IN N x m TORQUE SPECIFICATIONS
FIGURE 15