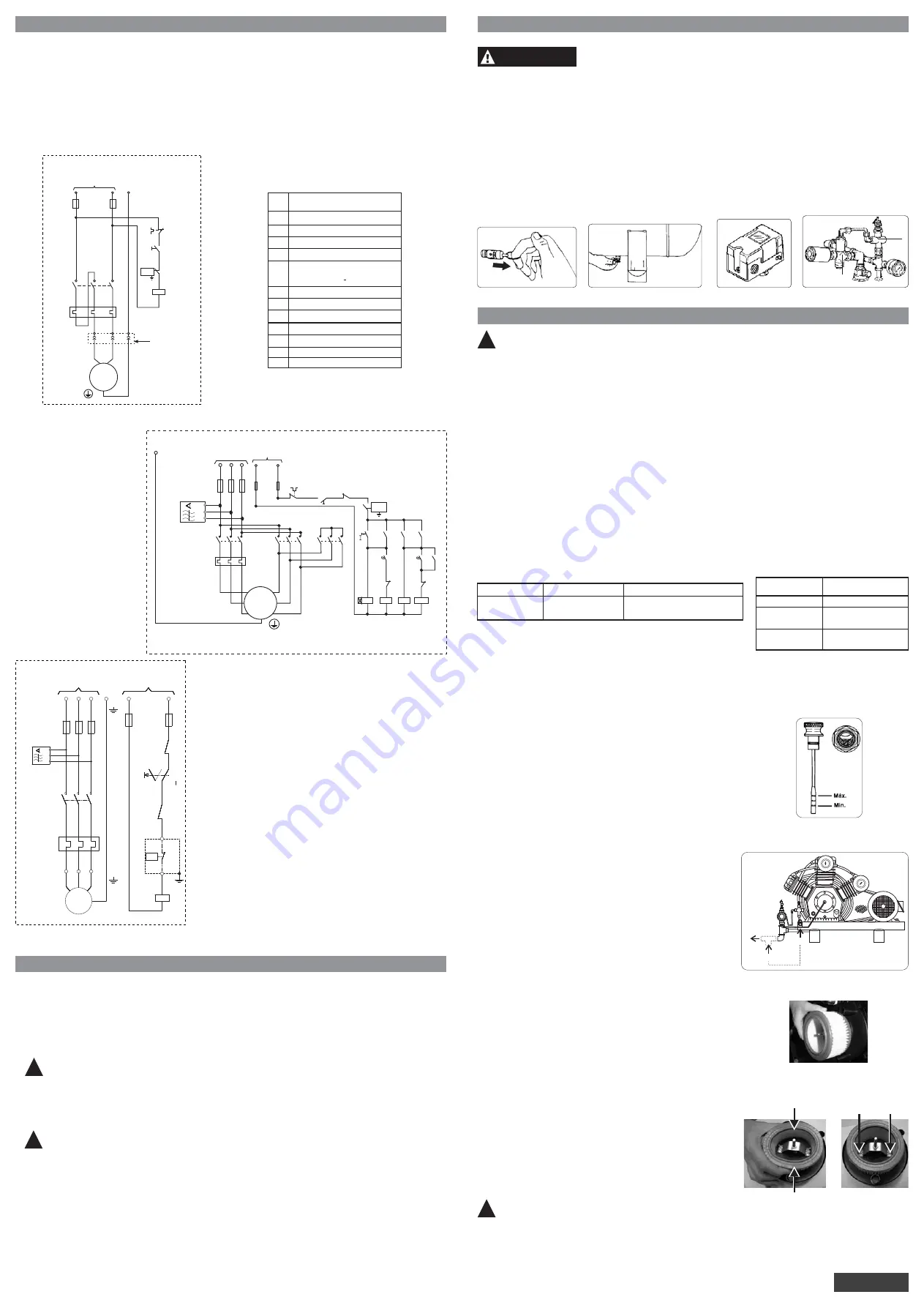
8) INSTALLATION
8) INSTALLATION
9. Multiwire diagram and ON/OFF switch
FIGURE 4 -
MULTIWIRE DIAGRAM - SINGLE PHASE -
STANDARD MOTOR (WITHOUT THERMAL PROTECTOR)
K1
FT1
1
1
2
2
3
3
4
4
5
5
6
6
Supply
voltage
Customer’s responsibility
M
1~
F1
GROUND
PLUG 2P+G
(see item 5.5, Chapter 8)
OR ELECTRIC CABLE
FT1
96
95
CH
K1
P-FK
A1
A2
FIGURE 6 - MULTIWIRE DIAGRAM - THREE
PHASE MOTOR STANDARD
FIGURE 5 - THREE-PHASE MOTORS DELTA STAR START
NOTE:
INSTALLATION EXPENSES ARE THE
PURCHASER RESPONSIBILITY.
This equipment is tested and filled up, in the factory, with reciprocating piston air compressor lubricant mineral oil.
If the ambient temperature is different from (Table 5) specification, change the lubricant oil.
After the arrangements regarding the location, the pressure vessel adequacy to local Technical Norms and
Legislation, electric network, electric switch and compressed air network (customer's responsibility) have been
carried out, do the following:
Completely open valve
(Customer's assembly).
Turn the start key electric motor and/or engine motor and check if the rotation direction is identical to the one
indicated by the arrow in the flywheel. If it isn’t, disconnect the equipment from the electrical supply and invert
any of its main cables if motor
is a three-phase one or motor’s cables 5 and 6 or 5 and 8 if it is single-phase.
Thereafter, connect the equipment to the electrical supply.
Let the compressor run for about ten (10) minutes to allow a homogeneous lubrication of the moving
parts.
Fully close the valve, so that the compressor can fill up the tank. Compressor will automatically turn off (through
the pressure switch - See Figure 9) or will automatically enter discharge mode (through the pilot/discharge
valve - see Figure 10) when the pressure gauge shows maximum pressure respectively around 175 psig (12
bar) for the model CSWV 40/460 this will happen at 250 psig (17 bar).
Check the tank filling up time according to Table 1.
FIRST START PROCEDURES:
1.
Check the oil level that must be between the maximum and minimum marks in the oil dipstick or in
the center of the oil level sight 17 (See Figure 11).
2.
20
3.
3
4.
5.
Important:
6.
7.
8.
7
9.
9
Open the valve to discharge the compressed air from the tank and this will decrease the internal pressure in the
compressor. The compressor will automatically re-start (through the pressure switch) when the pressure
gauge registers around 135 psig (9.3 bar) or (through the pilot discharge valve) when the pressure gauge
register approximately 155 psig (10.7 bar). For the model CSWV 40 /460 this will happen 210 psig (14.5 bar).
Close the valve and unplug the equipment.
Verify if safety valve (Figure 7) is working, pulling the ring.
Open drain
(Figure 8) to exhaust the tank condensed water, collecting it into a container; close the drain has
soon as the compressed air starts to come out. See item 2 of the following note.
!
!
9) START UP PROCEDURE
9) START UP PROCEDURE
9) START UP PROCEDURE
9) START UP PROCEDURE
F1
F21
K1
K2
K3
P
M
CH
KT1
I/O
FT1
FUSE TYPE "D" OR "NH"
(SEE TABLE 3)
COMMAND FUSE (2A)
THREE-POLE CONTACTOR
THREE-POLE CONTACTOR
THREE-POLE CONTACTOR
PRESSURE SWITCH
ELECTRIC MOTOR
ON/OFF SWITCH
TIME RELAY
ON/OFF BUTTON
OVERLOAD RELAY
(MUST BE AJUSTED TO THE ELECTRIC
MOTOR’S NOMINAL CURRENT FOR
DIRECT START AND -Y 3)
D Ö
FK
KFSF
FLOAT KEY
SEQUENCE AND PHASE FAULT RELAY
Note:
9
Important:
Attention:
1- The initial start procedure must be repeated whenever maintenance occurs or when the compressor is moved
to another location.
2- For your comfort Schulz S.A., Provides an electronic drain, model PS 16, which is adaptable to the tank’s
exhaust connection (drain)
and that can be purchased at Schulz Authorized Technical/ Distributor Schulz.
When installing it, the tank must be depressurized (empty).
See item 9, Safety Instruction - Chapter 6.
FIGURE 7
FIGURE 8
FIGURE 9
FIGURE 10
1
2
In order to guarantee the compressor's performance and to extend its life, please follow the
recommendations below:
1. Daily
A.
17
B.
9
C.
2. Recommended lubricant mineral oil
Important
-
3. Oil change procedures
A.
Check the oil level and add oil if necessary before switching the compressor on. The level must be between the
maximum and minimum marks in the oil dispstick or in the center of the oil level sight
(Figure 11).
Remove the condensed water from the tank through drain (Figure 8).
Check abnormal noise or vibration. If the problem persists after the following corrective actions are take, get in
touch with the nearest
.
- Your reciprocating piston compressor has been filled up in the factory with lubricant mineral oil.
Do not change the oil type. It may cause contamination by chemical incompatibility, thus reducing its useful
life and causing lubrication problems.
Change the oil according to the instructions , see Table 4:
* Oil change with the hot pump.
-
B.
15
16
17
Change Procedures:
- Unplug the equipment;
- Remove drain plug
and let the oil flow* into a container;
- Fasten the plug using thread sealing;
- See the correct oil volume on Table 1 - Technical Characteristics;
- Replace the oil through the plug's lodging orifice
or the oil dispstick
, located on the crankcase;
-
Table 4, shows the oil change intervals.
Schulz Authorized Technical/Distributor
!
10) PREVENTIVE MAINTENANCE
10) PREVENTIVE MAINTENANCE
B
B
A
Every 200 working hours or 2
months (wichever occurs first)
8 working hours
40 working hours after
the first change
FIRST CHANGE
OTHER CHANGE
TABLE 4 - OIL CHANGE INTERVALS
SECOND CHANGE
Below 0 C/32°F
0
SAE 10W or ISO 32
0 C to 20 C/
32°F to 68°F
0
0
SAE 20W or ISO 68
20 C to 40 C/
68°F to 104°F
0
0
ENVIRONMENT
TEMPERATURE
OIL TYPE
TABLE 5 - RECOMENDED OIL FOR PUMP
SAE 30W or ISO VG 100
FIGURE 11
4.
Weekly
A.
13
B.
C.
12
D.
7
5. Monthly
A.
6. Quarterly
A.
B.
C.
7. 9 months or every 1,000 hours (whichever occurs first)
A.
8
Check if the belt, located inside the belt protector
, is making
abnormal noise or movements. If so, see item 6 C procedure
below.
Clean the compressor external surface with neutral detergent.
Remove air filter element
(Figure 13). Check and when clogged
is necessary change. Immediately after, compress it and
assemble the element in the filter according to procedure 1**
(Figure 14) making sure it fits in and that its edges are properly
supported. Not following these instructions (the same for the other
filter models) may cause the air compressor to fail.
Check performance of safety valve (Figure 7).
Check performance of pressure switch (see items 5 and 6 of Start
Up Procedure).
Change the air filter element every 300 hours (whichever occurs
first).
Refasten screws (see Table 6) and nuts .
Check belt tension (Figure 2) and alignment (Figure 3). Belt's
tension, at medium point, deflects from 3/8" to 1/2" on manual
strength. To check deflection, remove belt's protector.
Check, re-fasten and clean: the valves located between the
cylinder's upper part and its cover, check the valve*
place in the
tank or base, re-fasten the screw located inside the compressing
unit and lubricate valve discharge item 2, Figure 10. Do it at the
nearest
.
* See item 9, Safety Instructions - Chapter 6.
Schulz Authorized Technical/ Distributor
8. Annually
A. Have the pressure switch, pressure gauge and valves (safety, pilot
and discharge) calibrated either by an official institution, or
according to local Technical Norms and Legislation. This
operation must be carried out to a device not coupled to the air
tank.
9. Removing From Service (discard)
All compressed air systems contain maintenance parts
(lubricating oil, filters) which are periodically replaced. These
used parts may be, or may contain, substances that are regulated
and must be disposed of in accordance with local, state, and
federal laws and regulations. See instruction in the Chapter 14.
Note:
Heavy duty and multi-viscous oils are not adequate for air compressor’s lubrication. The same applies to oils that
tend emulsify. We recommend good industrial oil for air compressors, with rust and oxidation inhibitors and high
viscosity level (from 90 to 95), SAE or ISO, as indicated in the Table 5.
FIGURE 12
025.0149-0
05/2009
rev. 06
IMPORTANT
!
SHEET 04/04
P-FK
Customer’s responsability
GROUND
Supply voltage
Comand Voltage
see item 5.5,
Chapter 8
R
T
S
3~
MOTOR
2
U
FT1
1
K1
2
1
KFSF
4
6
W
V
PE
5
3
6
4
5
3
F1
R
S
T
PE
K1
SH1
KSFF
I
F21
L1
A1
A2
FT1
95
96
16
15
0
I
0
F21
L2
Note:
- The energy supply must not present voltage changes over ± 10%.
- Voltage drop caused by start up must not be over 10%
- For three-phase electric motor, we recommend the installation of a sequence and phase fault relay at the
electric panel (provided the motor is not accompanied with one).
- For your safety, the installation must have a grounding conductor to avoid electric shocks.
- For dimensional of the nominal corrent (A), to consider the factor service (FS) indicated in the plate of
electric motor.
The above instructions are based on normal operation conditions. If the compressor is installed in a polluted area,
increase the number of inspections.
- Switch off the air compressor, remove the water and exhaust the air from the tank at the end of every working day.
** Assembly procedure of frontal filters from models CSV 15 MAX to MSWV 80 MAX. For all other models,
assembly must be carried out according to Figure 14 (item 1*).
FIGURE 13 -
REMOVING AIR FILTER
FIGURE 14
10.
11.
Open the valve to completely exhaust the tank and close it afterwards.
Your Schulz compressor is now ready to operate. Connect it to the air distribution network and start the
electric motor. When the compressor reaches maximum pressure, open the valve so that the air can flow to
the distribution network. Check if there is any leakage along the tubing, by using a water and soap lather.
ATTENTION
Risk of personal injuries
The tank maximum pressure when drained must be 10 psig (0.7 bar).
P-FK
CUSTOMER’S RESPONSABILITY
SUPPLY
VOLTAGE
GROUND
COMAND
VOLTAGE
see item 5.5, Chapter 8
*
**
Intermitence controlled by pressure switch
Intermitence controlled by pilot/discharge valve
*
**
T
S
R
F1
FT1
KFSF
FT1
CH
K1
K2
KT1
K3
K3
K2
K2
K1
K1
K1
K3
96
1
1
1
1
2
2
2
A1
A1
21
28
21
18
15
14
14
22
22
K2
KT1
KT1
K3
A1
A1
A2
A2
A2
A2
2
3
3
3
3
4
4
4
14
25
13
13
13
43
44
4
5
5
5
5
6
6
6
6
95
M
3~
F21
16
15
R
T
S
KFSF