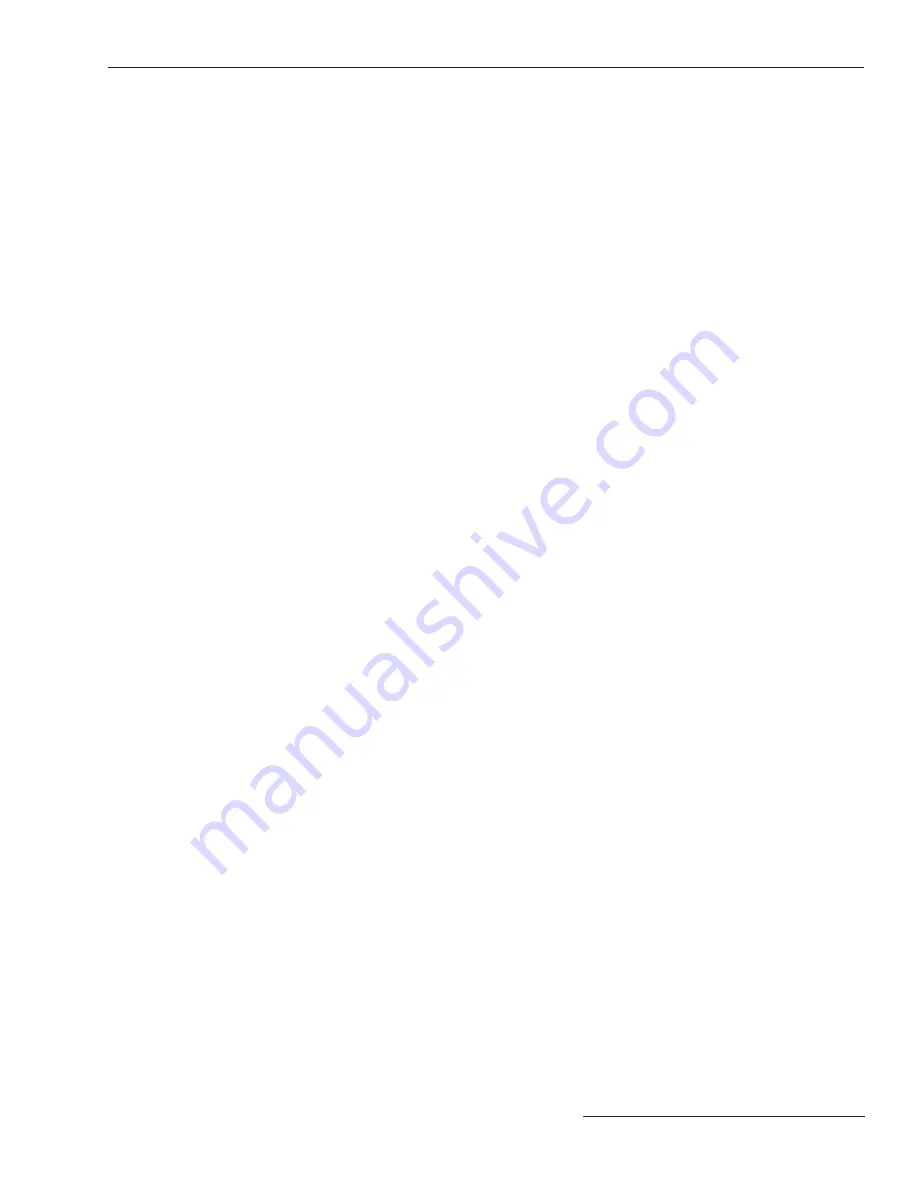
S&C Instruction Sheet 1042-511
11
Installation
STEP 8.
Enter the information from Step 7 on the
Setup>Team
screens.
STEP 9.
Determine the
Return to Normal
mode for each team and enter this information
on the
Setup>Team
screen.
When the
Return to Normal
mode is enabled, team members can return the
circuit to its normal configuration either automatically once a stable three-phase
voltage has been restored to the faulted line segment, or by command. For teams
with one or more tie switches, the
Open Transition
mode can be selected (the
tie switch(es) open before the other team members return the circuit to its normal
configuration) or the
Closed Transition
mode can be selected (the team members
close all of the switches and then the tie switch(es) open). The
Return to Normal
process starts at the line segments closest to the normal source and works outward.
STEP 10.
Configure the
RTN Time
setpoint.
Power must be restored to the faulted line segment for this amount of time (in
minutes) before the
Return to Normal
process will start. Enter this information
on the
Setup>Team
screen.
STEP 11.
Configure the
Maximum Capacity
setpoint for each team member on the
Setup>
Team Configuration
screen.
The maximum capacity is the amount of load on the most limited line section
(because of conductor size, switch rating, etc.) served through a team member’s loca-
tion from either direction. Each member continuously subtracts its present load from
its
Maximum Capacity
setpoint to determine its
Local Capacity for Transfer
value.
The smallest
Local Capacity for Transfer
value encountered in a particular resto-
ration path determines the maximum load that the involved teams can transfer, the
Available Capacity to Transfer
value.
STEP 12.
Configure the
Alternate Source Sequence
setpoint on the
Setup>Team
screen.
Using the normal switch functionality determined in Step 7, set the sequence
team members will use to restore the line segment. This is an optional step used to
guide the restoration process. Regardless of the alternate-source sequence configu-
ration, restoration progresses in the following order: When the fault is downstream
of the team, the coach will: 1) try the normal source switch, 2) use the
Alternate
Source Sequence setting
(if applicable), 3) try any tie switch(es), and 4) try any
load-tie switch(es). When the fault is upstream of the team the coach will: 1) use
the
Alternate Source Sequence
setting (if applicable), 2) try any tie switch(es),
3) try any load-tie switch(es), and 4) try the normal source switch.
STEP 13.
Determine whether any contracts are required to avoid overloading a line segment.
A bifurcated circuit acting as an alternate source for teams on both legs of the
bifurcation may become overloaded if those teams must act to restore load at close
to, or exactly, the same time. This overload may occur because those teams are not
directly related and do not coordinate their reconfiguration activities.
To force coordination between these unrelated teams, set the
Contract
Required
setpoint to the
Yes
state on the
Setup>Team
screen for teams that may
add load to the alternate circuit during a reconfiguration event. The contract will
prevent both teams from simultaneously closing to use the alternate source. When
team members encounter a line segment in a restoration path that requires a con-
tract, they will communicate with all subsequent line segments in the direction of
the alternate source to make sure the source and line segments will not be over-
loaded. The first team contract to arrive at the source will be approved if the team
load would not overload the circuit. The second arriving contract will be approved
only if it would also not cause an overload.
The extra communication required to transmit the contracts slows down the
reconfiguration process. Contracts are described in Instruction Sheet 1042-541,
“S&C 5800 Series Automatic Switch Controls With IntelliTeam
®
II Automatic
Restoration System:
Operation
.”
Содержание 5800 Series
Страница 27: ...S C Instruction Sheet 1042 511 27 Installation Diagrams...
Страница 28: ...28 S C Instruction Sheet 1042 511 Installation Diagrams...
Страница 29: ...S C Instruction Sheet 1042 511 29 Installation Diagrams...
Страница 30: ...30 S C Instruction Sheet 1042 511 Installation Diagrams...
Страница 31: ...S C Instruction Sheet 1042 511 31 Installation Diagrams...
Страница 32: ...32 S C Instruction Sheet 1042 511 Installation Diagrams...
Страница 33: ...S C Instruction Sheet 1042 511 33 Installation Diagrams...
Страница 34: ...34 S C Instruction Sheet 1042 511 Installation Diagrams...
Страница 35: ...S C Instruction Sheet 1042 511 35 Installation Diagrams...
Страница 36: ...36 S C Instruction Sheet 1042 511 Installation Diagrams...
Страница 37: ...S C Instruction Sheet 1042 511 37 Installation Diagrams...
Страница 38: ...38 S C Instruction Sheet 1042 511 Installation Diagrams...