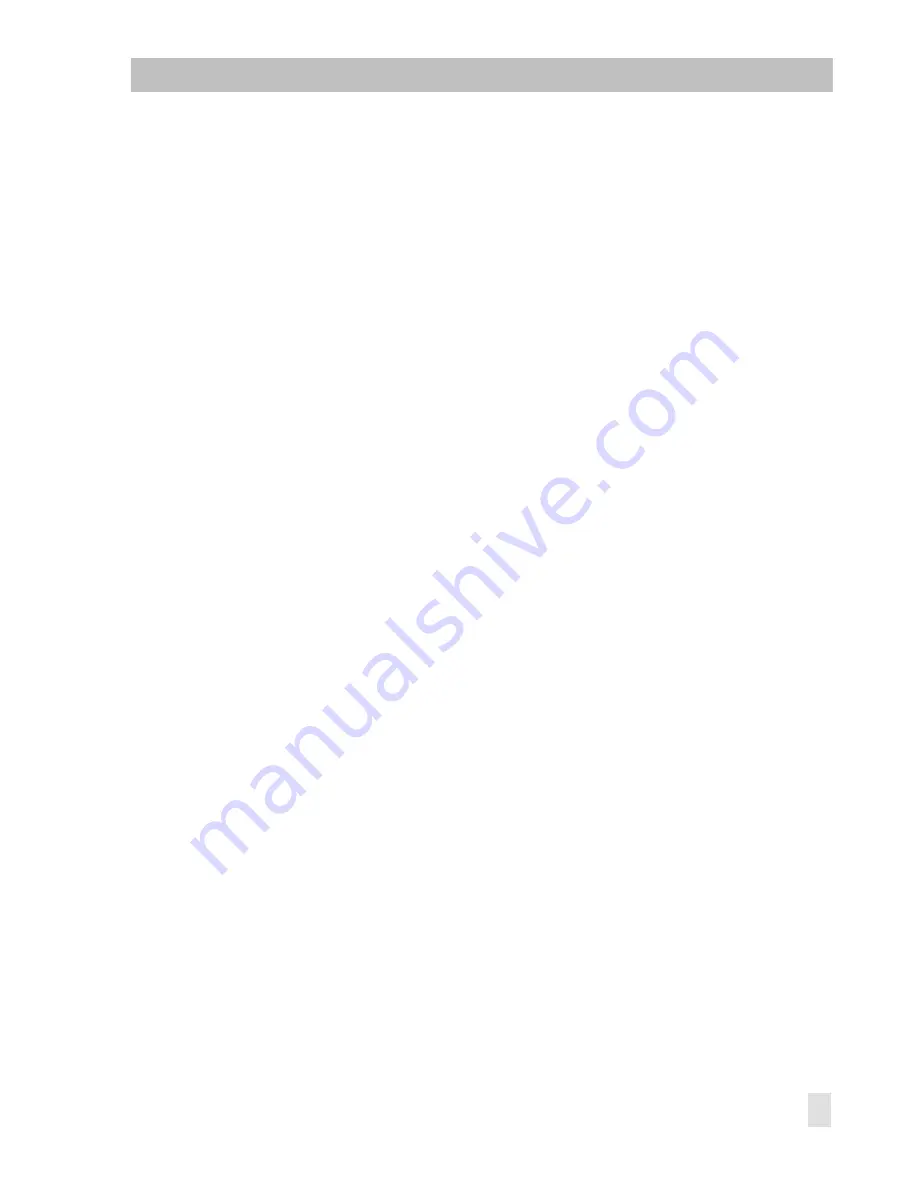
1.1 Application
The linear actuators operate the final control
elements which require a linear travel motion
from 15 to 120 mm and a positioning force in
the range of 2 to 25 kN.
The shut-off force of the actuators is adjusted
permanently. The travel, however, can be
modified at a later date.
1.2 Versions
The electrical components are located sepa-
rately from the gear underneath the sealed
cover where they are protected from dust and
can be easily accessed when the cover is
removed.
The
basic version
of the device comprises:
– Two torque
switches DE-S1
and
DE-S2
.
They switch off the motor when the force ad-
justed in the actuator is counterbalanced by
a corresponding force. Thus, they protect
the final control element from damage, and
the actuator from overload.
– One travel
switch WE-S3
for limitation of
the travel in the opening direction.
– Two travel
switches WE-S4
and
WE-S5
for
indicating intermediate and positions of the
final control element.
The following components can be installed
optionally
:
– A fourth travel
switch WE-S6
for indicating
certain control element positions.
– One or two
potentiometers
or one
electronic
position transmitter ESR
for analog remote
transmission of the final control element’s
position.
– One
heating resistor
to prevent the forma-
tion of condensation water underneath the
cover when the humidity is high and the am-
bient temperatures fluctuate considerably.
At an inside temperature of
>
60
°
C, the
heating resistor deactivates the heating via
a temperature relay; it reactivates the heat-
ing at a temperature of
<
40
°
C.
– One electronic positioner for the analog
control 0 (2) to 10 V / 0 (4) to 20 mA (only
for 230 V, 50 Hz AC motors).
1.3 Function
The rotary motion of the motor is transferred
to the gear wheel with a female thread via the
gearing.
The piston rod with the matching male thread
engages the female thread. An anti-rotation
device secures the rod and prevents it from ro-
tating.
The piston rod performs a linear motion,
either pulling or pushing, when the female
threaded gear wheel is turned via the motor
gear.