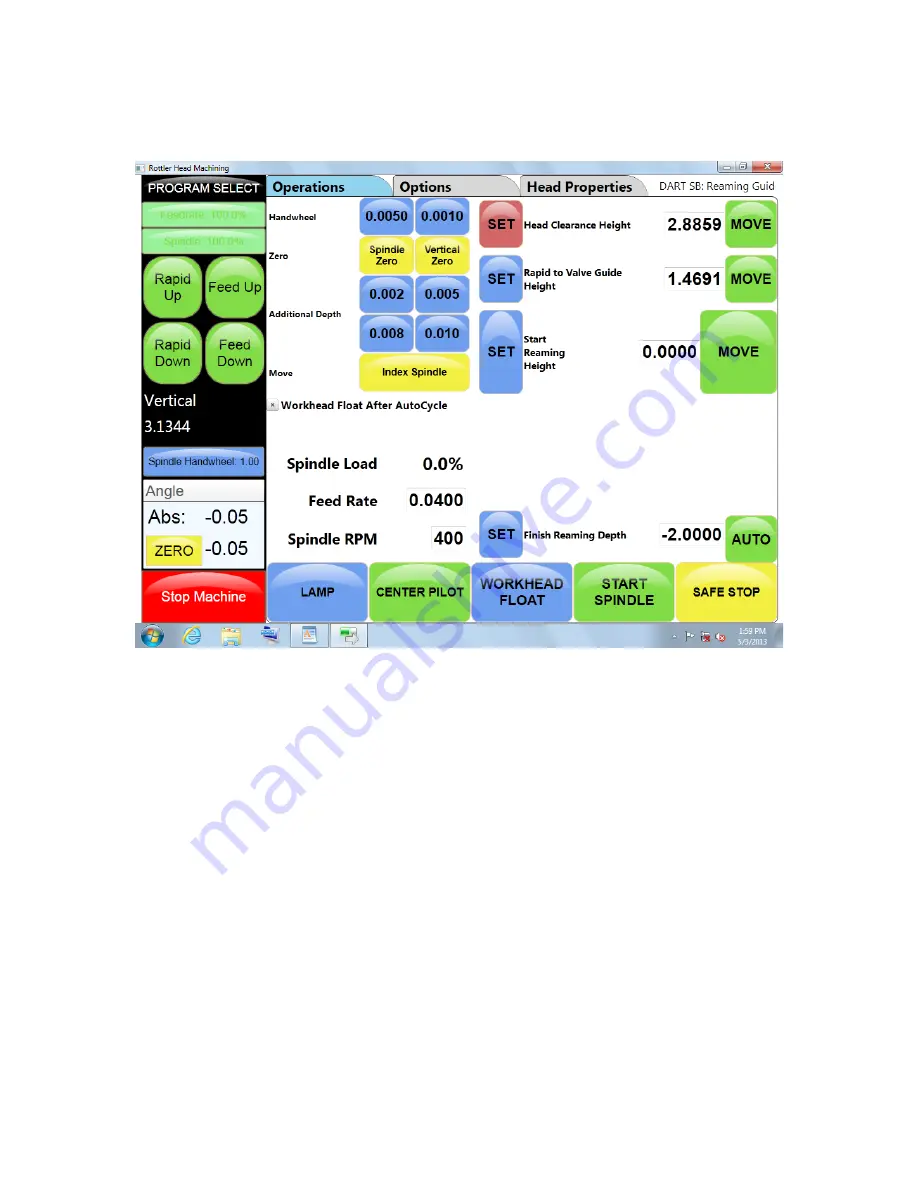
Section 4 Control Definitions
SG10A Manual
www.rottlermfg.com
4-9
Reaming Program: Operations Screen
Vertical Zero
Set this height when tip of reamer just contacts head surface or top of guide. Your choice.
HEAD CLEARANCE HEIGHT
and
RAPID TO VALVE GUIDE HEIGHT
is same as previously described.
Start Cutting Height
Is set when reamer pilot is into guide enough to center but not yet to cutting edges.
Finish Cutting Depth
Is length of guide being cut. Add guide length to “start reaming height “ figure and add .100 to be safe.
Remember to push the +/- for a negative #.
Содержание SG10A
Страница 2: ......
Страница 4: ......
Страница 8: ...Section 1 Introduction SG10A Manual www rottlermfg com 1 4...
Страница 22: ...Section 2 Installation SG10A Manual www rottlermfg com 2 13...
Страница 60: ...Section 5 Operating Instructions SG10A Manual www rottlermfg com 5 14 Rottler Six and One Instructions...
Страница 61: ...Section 5 Operating Instructions SG10A Manual www rottlermfg com 5 15...
Страница 62: ...Section 5 Operating Instructions SG10A Manual www rottlermfg com 5 16...
Страница 82: ...Section 6 Maintenance SG10A Manual www rottlermfg com 6 9...
Страница 90: ...Section 8 Machine Parts SG10A Manual www rottlermfg com 8 3 Base Table and Riser Assembly...
Страница 91: ...Section 8 Machine Parts SG10A Manual www rottlermfg com 8 4...
Страница 92: ...Section 8 Machine Parts SG10A Manual www rottlermfg com 8 5...
Страница 93: ...Section 8 Machine Parts SG10A Manual www rottlermfg com 8 6 Base Assembly...
Страница 94: ...Section 8 Machine Parts SG10A Manual www rottlermfg com 8 7...
Страница 95: ...Section 8 Machine Parts SG10A Manual www rottlermfg com 8 8...
Страница 96: ...Section 8 Machine Parts SG10A Manual www rottlermfg com 8 9 Spindle Assembly...
Страница 97: ...Section 8 Machine Parts SG10A Manual www rottlermfg com 8 10...
Страница 98: ...Section 8 Machine Parts SG10A Manual www rottlermfg com 8 11...
Страница 99: ...Section 8 Machine Parts SG10A Manual www rottlermfg com 8 12...
Страница 100: ...Section 8 Machine Parts SG10A Manual www rottlermfg com 8 13 Transmission Assembly...
Страница 101: ...Section 8 Machine Parts SG10A Manual www rottlermfg com 8 14...
Страница 102: ...Section 8 Machine Parts SG10A Manual www rottlermfg com 8 15...
Страница 103: ...Section 8 Machine Parts SG10A Manual www rottlermfg com 8 16 Head Support Assembly...
Страница 104: ...Section 8 Machine Parts SG10A Manual www rottlermfg com 8 17...
Страница 105: ...Section 8 Machine Parts SG10A Manual www rottlermfg com 8 18...
Страница 106: ...Section 8 Machine Parts SG10A Manual www rottlermfg com 8 19 Pneumatic Circuit Diagram...
Страница 107: ...Section 8 Machine Parts SG10A Manual www rottlermfg com 8 20 Electrical Components...
Страница 110: ...Section 9 Options SG10A Manual www rottlermfg com 9 2...
Страница 112: ...Section 10 Material Data Safety Sheets SG10A Manual www rottlermfg com 10 2...
Страница 113: ...Section 10 Material Data Safety Sheets SG10A Manual www rottlermfg com 10 3...
Страница 114: ...Section 10 Material Data Safety Sheets SG10A Manual www rottlermfg com 10 4...
Страница 115: ...Section 10 Material Data Safety Sheets SG10A Manual www rottlermfg com 10 5...
Страница 116: ...Section 10 Material Data Safety Sheets SG10A Manual www rottlermfg com 10 6...
Страница 117: ...Section 10 Material Data Safety Sheets SG10A Manual www rottlermfg com 10 7...
Страница 118: ...Section 10 Material Data Safety Sheets SG10A Manual www rottlermfg com 10 8...
Страница 119: ...Section 10 Material Data Safety Sheets SG10A Manual www rottlermfg com 10 9...
Страница 120: ...Section 10 Material Data Safety Sheets SG10A Manual www rottlermfg com 10 10...
Страница 121: ...Section 10 Material Data Safety Sheets SG10A Manual www rottlermfg com 10 11...
Страница 122: ...Section 10 Material Data Safety Sheets SG10A Manual www rottlermfg com 10 12...
Страница 123: ...Section 10 Material Data Safety Sheets SG10A Manual www rottlermfg com 10 13...
Страница 124: ...Section 10 Material Data Safety Sheets SG10A Manual www rottlermfg com 10 14...