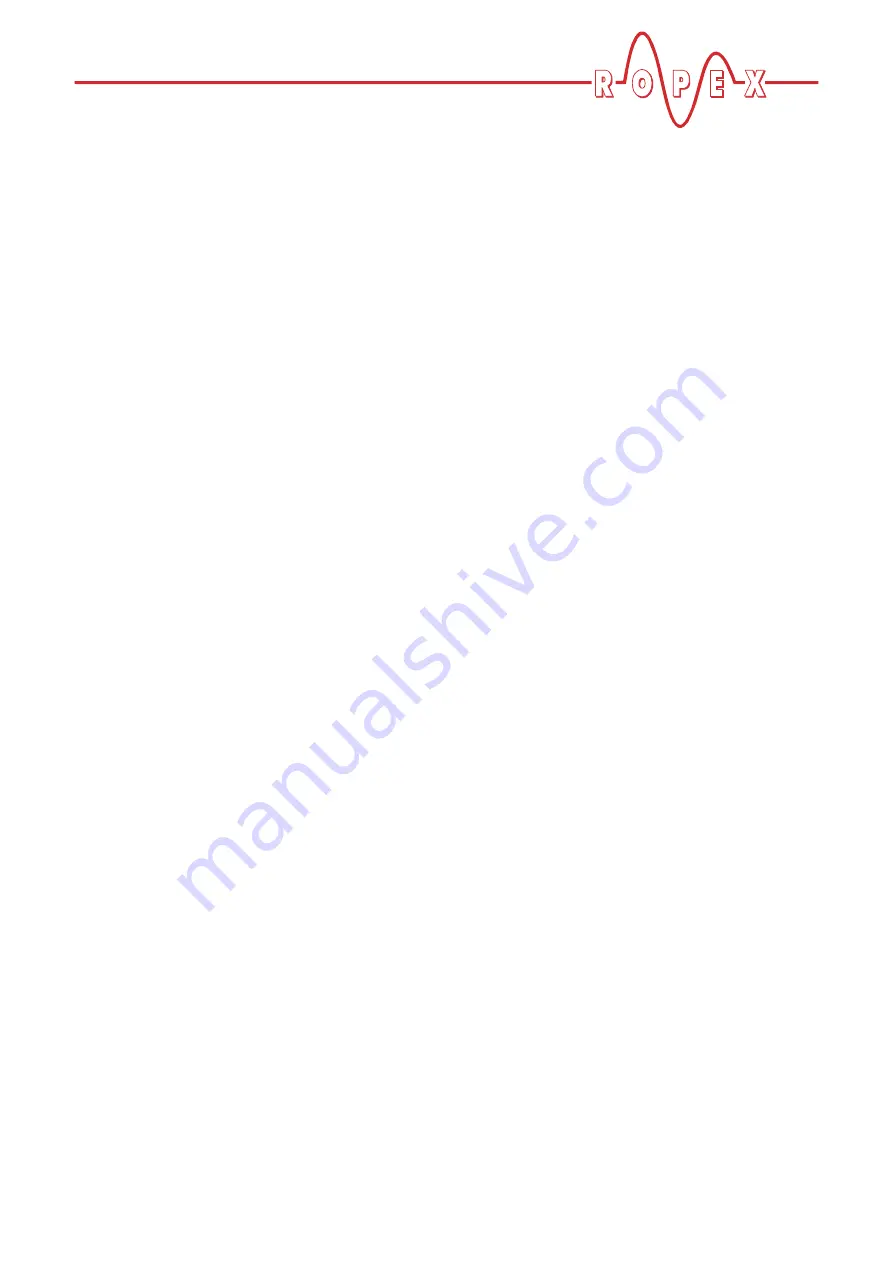
Basics of temperature control / measurement
RESM-5
Page 7
If the actual temperature of a heatsealing band in a
closed control loop deviates from the set point, the
following relationship is true:
(1)
(2)
In other words, the temperature error
depends on
the relative resistance change (due to the fault) and the
temperature coefficient (TCR) of the resistor material.
The temperature error
can be either positive or
negative depending on the sign of the fault (higher or
lower resistance)
.
The temperature error for the standard heatsealing
band alloy where
is thus as
follows:
(3)
This relationship is easily explained with the help of an
example:
If the heatsealing band is "shortened" 20% electrically
(
) (e.g. by inserting a conducting part), the
temperature error according to (3) is +200K.
In this case, the actual heatsealing band temperature
according to (2) is as follows:
It is clear from this example that a control system which
operates according to the resistance principle responds
extremely sensitively to heatsealing band resistance
faults or faults in the associated electromechanical
components.
The diagram on page 6 shows how the components A,
B, C, and D belonging to the power cable are potential
fault sources, for instance, because any change in the
contact resistances distorts the resistance measured
by the controller.
3.3
Fault causes
If all of the components belonging to the control loop
are analyzed with respect to possible faults that could
lead to dangerous overheating, several potential
causes can be identified, e.g.:
• Contact between two heatsealing bands wired in
series
• Ground fault
• Partial short-circuit
• Non-coppered heatsealing band ends
• Unsuitable heatsealing band alloy (
or too
low)
• Defect in the measuring circuit of the controller
electronics
• Defect in the power unit of the controller, e.g. triac
remains conductive without an ignition signal
• Short circuit in the external wiring such that the triac
is bypassed
• Defect in the current transformer
• Short circuit or break in the current or voltage
measurement cables (U
R
)
• Operator error
• etc.
Sudden resistance changes which are so large that the
measured resistance is outside of the operating range
(below zero or above 300°C / 500°C) can be detected
and indicated by the controller.
On the other hand, smaller resistance steps or gradual
changes cannot be detected as faults owing to the
operating principle of the unit, so that the above-
mentioned temperature deviations occur.
Some of the faults described here can be measured by
RESISTRON controllers with an alarm function.
Others are detected by the RESISTRON monitoring
device (RESM-5) and the MSW (refer to the separate
documentation).
Even these two monitoring units are still unable to
detect a few fault types (
Δ
T
Δ
R
R
--------
–
1
TCR
-------------
⋅
=
Δ
T
T
HL
T
Set
–
=
Δ
T
Δ
R
Δ
T
TCR
+10 10
4
–
K
1
–
⋅
=
Δ
T
1000
Δ
R
R
--------
–
K
[ ]
⋅
=
Δ
R
R
--------
0,2
–
=
T
HL
Set point 200K
+
=
TCR
0
=