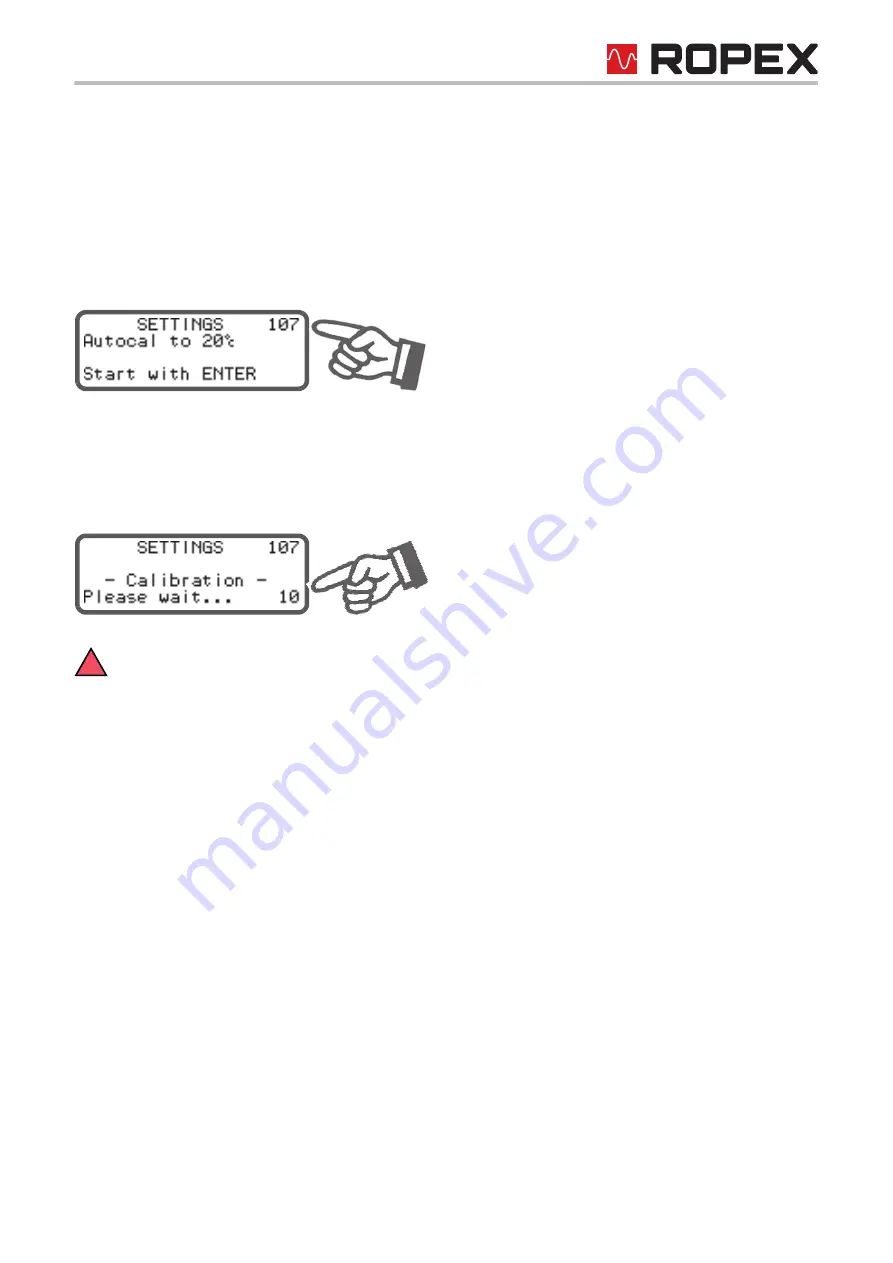
Controller functions
Version 1
RES-430
Page 47
10.8
Automatic zero calibration (AUTOCAL)
Owing to the automatic zero calibration (AUTOCAL) function, there is no need to adjust the zero point manually
on the controller. The "AUTOCAL" function matches the controller to the current and voltage signals that are
present in the system. You can activate this function by selecting step 107 in the Settings menu and then pressing
the "ENTER" key. The initial temperature (ambient temperature) of the heatsealing bar(s) which is currently valid
for calibration can be set beforehand in the 0…40°C range using the "UP" and "DOWN" keys.
The zero point is calibrated in the factory to 20°C.
The automatic calibration process takes around 10…15 seconds. The heatsealing band is not heated until the cali-
bration process has finished.
The message "- Calibration - Please wait..." appears on the display while the "AUTOCAL" function is executing
and a counter counts down from 14 to 0. The actual value output (terminals 10+11) is set to 0°C (corresponds to
0 VDC) for the duration of the calibration process.
You should always wait for the heatsealing band and the bar to cool down (to ambient temperature)
before activating the "AUTOCAL" function.
Reasons for locked AUTOCAL function:
1. The "AUTOCAL" function cannot be activated if the heatsealing band cools down at a rate of more than 0.1K/
second. This is additionally indicated with step 107 in the Settings menu by the message "Heatsealing band
still hot! Please wait...".
2. If the "START" signal (HEAT) is activated, the "AUTOCAL" function is not executed. This is additionally indi-
cated with step 107 in the Settings menu by the message "Autocal locked! (START sig. active)".
3. The AUTOCAL function cannot be activated if a fault with error code 101…103, 201…203, 8xx or 9xx occurs
(
section 10.21 "Error messages" on page 60).
!