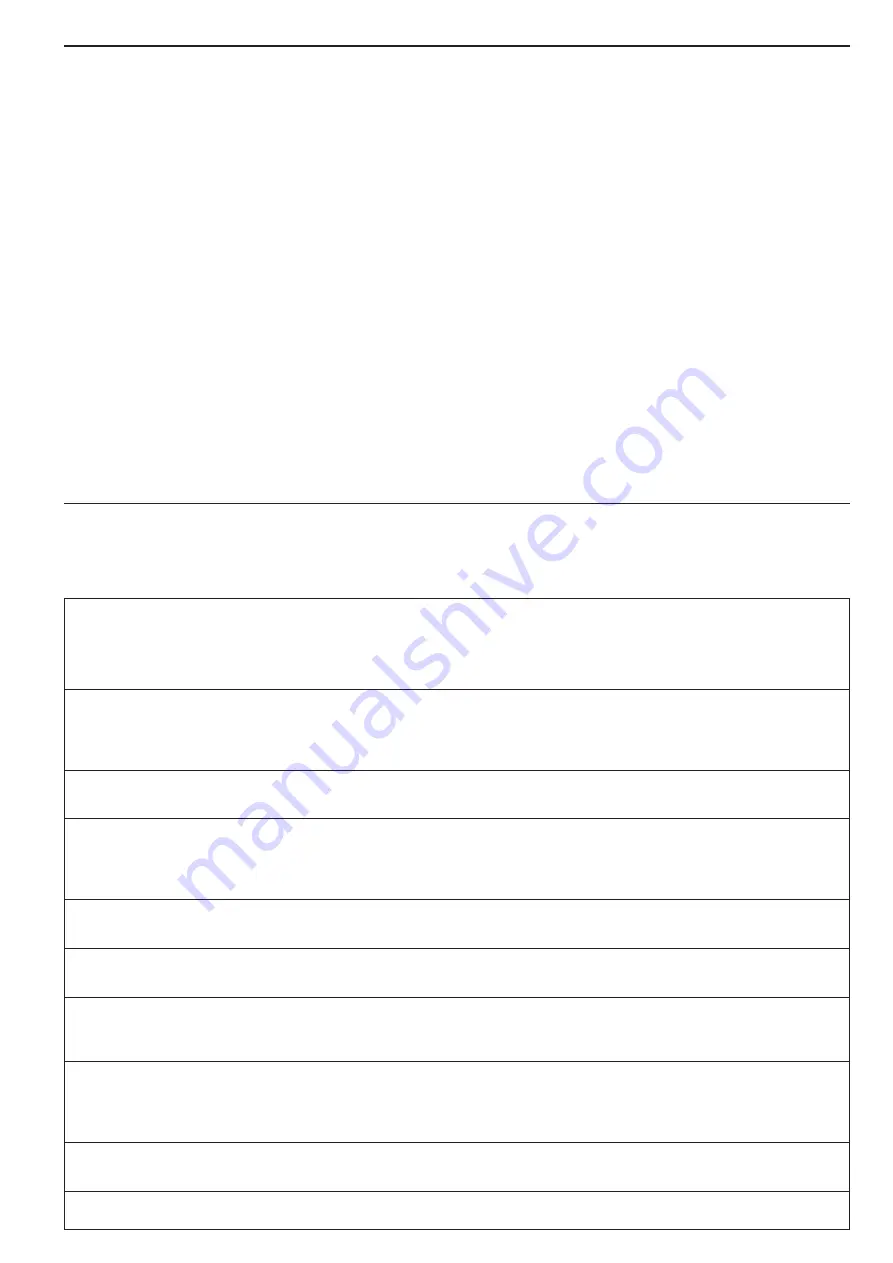
eng
eng
3.3.
Use of the ROLLER’S Nipparo nipple holder
3
/
8
–2”
In order to hold the piece of pipe with the nipple holder Nipparo, it is
necessary to spread the head of the nipple holder by turning the spindle
with and corresponding tool (screw driver...). This may only be made
with a pipe attached. Care has to be taken that the nipples ore not shor-
ter than provided by the standards (Pic. 3).
4.
Maintentance
Disconnect from the power supply before service and repair. These jobs
should only be done by experts or authorised persons.
4.1.
Servicing
The electric threaders ROLLER’S King 1
1
/
4
and King 2 are maintenance
free. Because of a permanent grease lubrication the electric theaders
need no servicing.
4.2.
Changing of carbon brushes
The carbon brushes need to be checked for wear and replaced from
time to time. For this inspection loosen the 4 screws on the motor handle
(11) by approx. 3 mm, pull the handle towards the rear and take off the
two covers of the motor.
4.3.
Changing arresting lever (Pic. 2)
Screw out both of the slotted screws alongside the arresting lever. Re-
move arresting lever, spring and cylindrical pin. Remove burr from slot
if necessary. Re-assemble in reverse order. Check function!
4.4.
Changing dies of Central die heads
Hold die head vertically in a vice, loosen screws, remove cover, take
out dies. Knock new dies into slots vertically from above, die 1 in slot 1
etc., bevel downwards. The backs of the dies must be flush with the bo-
dy edge. Fit cover, tighten screws, at first only lightly. Knock dies with a
copper punch or a hardwood wedge until the die backs are in contact
with the cover edge.
Careful! Do not damage teeth! Now tighten screws!
4.5.
Changing dies of Rola and Rola automatik die heads
Hold die head vertically in a vice. Close tensioning stirrup, loosen
screws, lift off cover with adjusting ring and take out dies. Fit new dies,
die 1 in slot 1 and so on, die grooves upwards, bevels downwards. The
backs of the dies must be flush with she edge of the body. Fit cover with
adjusting ring. Make sure that the scale line on the edge of the cover
corresponds with the scale line on the body. Retighten screws. Check
function by opening and closing the die head a number of times.
Scale: Line on line indicates standard thread size. On the edge of the
body alongside the scale line are the marks + and –. If the cover is
turned slightly t the thread Ø becomes larger and towards –
smaller.
5.
Procedure by faults
Attention! All works marked with
l
are only to be carried out by electrical specialists. Pull out mains plug!
Fault
Possible cause
Remedy
Motor does not start
Cable broken
l
Check cable
Main fuse is burned out
Replace fuse
Carbon brushes have no contact
l
Check condition and position of carbon
brushes. Replace worn brushes
Change-over switch not to the limit (8)
Push change-over switch to the limit (8)
Motor accepts no load
Short in the cable connection
l
Seek short and rectify.
Overloading through blunt dies
Replace dies
Unsuitable cuffing oil
Use ROLLER thread cutting oil
Overload disengaged
Engage overload button (10)
Abnormal overheating of motor
Overloading through blunt dies
Replace dies
Insufficient cooling air
Clean air slots in motor
Sparking in motor
Very dirty collector surface
l
Send in for repair
Carbon brushes fit badly due to excessive wear
Replace worn carbon brushes Use only
original carbon brushes.
Unsuitable brushes
l
Use original brushes
Fire ribbon in motor
Dirt particles spring from brushes or segments
l
Send in for repair
and burn out
Die head does not cut
Blunt or broken dies
Fit new dies
Rotation objection false
Check position or change-over switch
Automatik die head does not open
Dirty die guide slots
Open die head, remove dies, wash guide slots
after cutting operation
and dies with cold cleaner or paraffin.
Grease before reassembly.
Torn thread
Dies blunt
Fit new set of dies
Dies not fitted in correct order
Fit dies in correct order
Poor quality material
Observe mark of quality when buying material
Unsuitable thread cutting oil
Use ROLLER thread cutting oil
Pipe turns in support
Fine scale and dirt on the gripping
Clean with wire brush
bracket during cutting operation
jaws
Die head jams during changing
Swarf on the arresting part of die head
Remove sworf with flat file