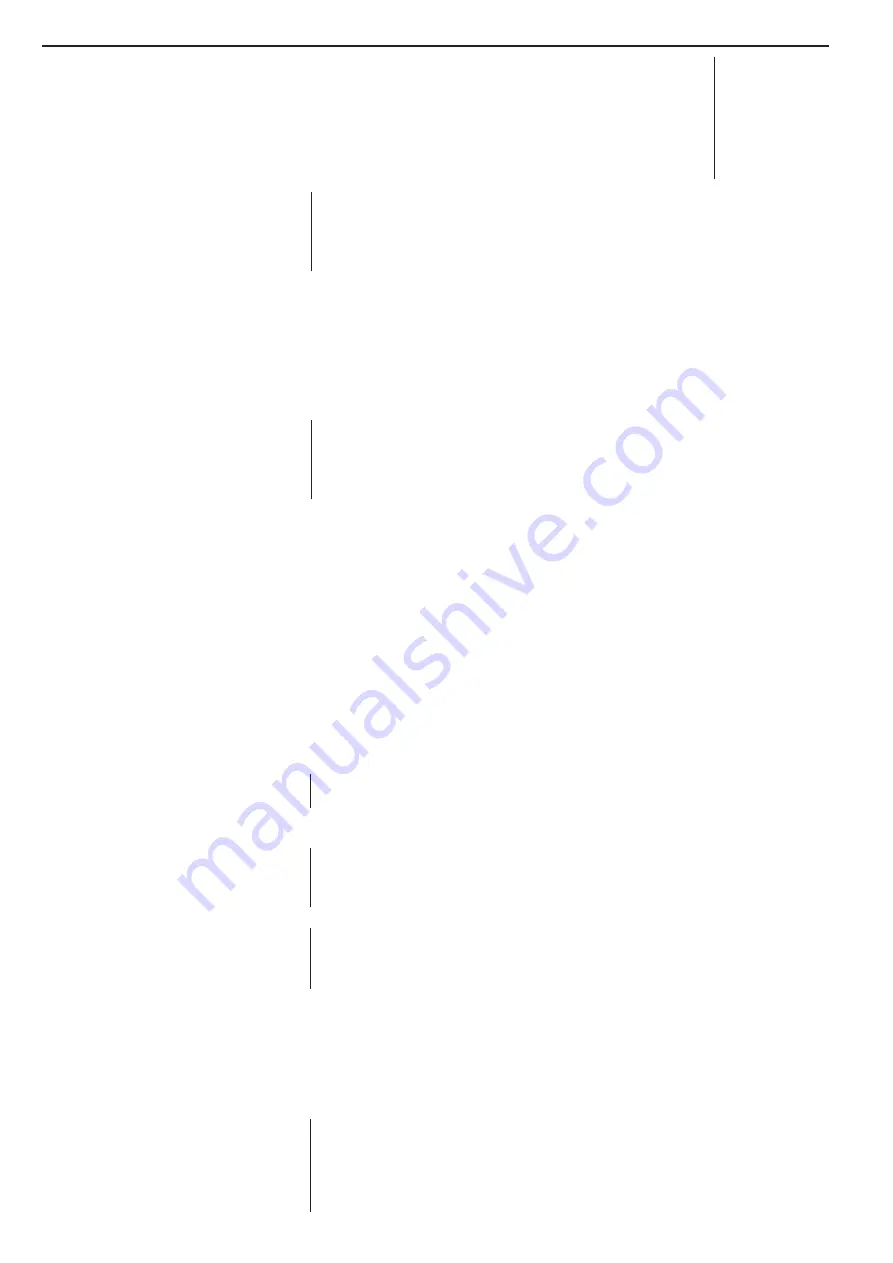
eng
eng
an intensive skin contact has to be avoided. An appropriate skin protector
has to be applied.
•
Do not allow undiluted cooling lubricant to get into drainage, water systems
or the soil. Remaining cooling lubricants have to be delivered to speciali-
zed waste disposal companies. Disposal identity number for mineral-based
cooling lubricants 54401, for synthetic 54109.
1.
Technical Data
ROLLER’S
ROLLER’S
King 1
1
/
4
King 2
1.1.
Article numbers
Drive unit
847309
850309
Support bracket
847310
850310
ROLLER’S Double
support bracket 543100
1.2.
Operating scope
ROLLER’S King 1
1
/
4
Thread-Ø
Die head type
R
1
/
8
–1
1
/
4
”
Central C 1
1
/
4
(Pic. 5)
R
3
/
8
–1
1
/
4
”
Rola Automatik (Pic. 6)
ROLLER’S King 2
Thread-Ø
Die head type
Adaptor
R
1
/
8
–2”
Central C 1
1
/
4
and C 2 (Pic. 5)
1
/
8
–1
1
/
4
”
R
3
/
8
–2”
Rola Automatik
(Pic. 6)
3
/
8
–1
1
/
4
”
Thread types:
Pipe thread ISO 7-1 DIN 2999
conical 1:16 (BSPT),
right and left hand thread.
Pipe thread NPT conical 1:16,
right hand thread.
Further threads on inquiry
(G, NPSM, Mx1.5 (IEC), Pg, M, etc.).
Thread length
Die length = thread length.
The die heads Rola Automatik
automatically cut the prescribed
standard thread length.
Making nipples
with nipple holder ROLLER’S
Nipparo R
3
/
8
–1
1
/
4
” or
3
/
8
–2”,
right and left hand thread. (Pic. 3)
1.3.
Revolutions
The revs are automatically
adjusted to thread sizes
35–27
1
/min
30–20
1
/min
1.4.
Performance data
230 V, 50–60 Hz
Nominal input
1200 W
1200 W
Nominal current
6 A
6 A
Fuse protection (Network) 10 A (B)
10 A (B)
Intermittent duty
S3 20%
S3 20%
110 V, 50–60 Hz
Nominal input
1200 W
1200 W
Nominal current
12 A
12 A
Fuse protection (Network) 20 A
20 A
Intermittent duty
S3 20%
S3 20%
Insulation according to VDE 0740 and CEE recommendation No. 20.
The nominal current con rise by 50 % for a short period, without effect
on the threader. The electric threaders ROLLER’S King 1
1
/
4
and ROL-
LER’S King2 are equipped with an overload protection, which switches
the motor off, when being overloaded. After a short time the green but-
ton (see 10) on she handle has to be reset.
1.5.
Dimensions
Electric threader
480×75×165 mm
492×78×196 mm
Support bracket
260×70×150 mm
415×105×175 mm
1.6.
Weight
Electric threader
4,50 kg
5,70 kg
Support bracket
1,10 kg
2,35 kg
1.7.
Noise data
ROLLER’S
ROLLER’S
King 1
1
/
4
King 2
Workplace-related
noise level
83 dB (A)
83 dB (A)
1.8.
Vibrations
Weighted effective value
of acceleration
2,5 m/s
2
2,5 m/s
2
2.
Operating
2.1.
Electrical connection
Before connecting, check that the mains voltage corresponds with the
data on the type plate. Extension cable must be at least 1,5 mm
2
cross
section.
2.2.
Thread cutting medium and oils
Use ROLLER thread cutting mediums and oils.
Never cut threads dry!
Choose the riqht lubrication according to material and use.
Use all thread-cutting medium and oils only undiluted!
2.2.1. Thread cutting medium Rubinol 2000: Red cutting oil free of mineral oil
(DVGW-Check-No. DW-0201AS2031). For all types of threads, espe-
cially for drinking water.
2.2.2. Thread cutting oil Smaragdol: Cutting oil with mineral oil concents.
Suitable for all types of thread and material. Observe regulations when
working on drinking water pipes.
3.
Operating
3.1.
Fitting the die head (1)
Insert Central or Rola Automatik die head in die head receiver or adaptor,
turn until arresting lever engages (see Pic. 2 and 4).
3.1.1. Functioning of die heads
The die heads Rola Automatik open automatically when the standard
lenght is reached.
The Central die heads have to be reversed.
Only operate change-over switch (8) when motor is stationary!
3.1.2. Functional check of the die head Rola Automatik
Check the function of the automatic die heads when die heads are new
or after long storage:
Operate tensioning stirrup a number of times, pull = open, push = close.
3.1.3. Support bracket. The support bracket (3) serves to support the die stock
against of torque in both directions of rotation, i. e. for advance and
reserve rotation of the die head, for right- and left hand threading. Support
bracket must always he used!
3.2.
Thread cutting
3.2.1. Fasten support bracket approx. 10 cm before end of pipe, by attaching
it, so that the pipe is centered in between the jaws (4) and spindle (5).
Locking handle has to be tensioned tightly. Before threading, pipe end
should be slightly oiled. Then the threader has to be attached to the pipe
with the bracket between handle (6) and motor housing (7). Adjust
change-over switch (8). After having checked the rotation (R – right
hand thread or reverse for left hand thread L – left hand thread or re-
verse for right hand thread), press on/off-switch (9) while simultaneously
gripping the handle (11) (Pic. 6).
3.2.2. Starting cutting
Press the electric threaders against the pipe until the die head starts to
cut. During cutting sufficient lubrication is necessary.
3.2.3. Reversing and removing the electric thread cutter
With the use of Central die heads, the thread is finished when the dies
are level with the end of the pipe. Release the rocker switch and set the
changeover switch to position L (operate the changeover switch only
when the machine is at a standstill). Now switch on the thread cutter
again. The die head will retract away from the thread. With the machine
at a standstill, set the changeover switch to position R. The retraction
process does not take place with Rola die heads.
Rola die heads open automatically when the standard lenght is
reached (Pic. 5).