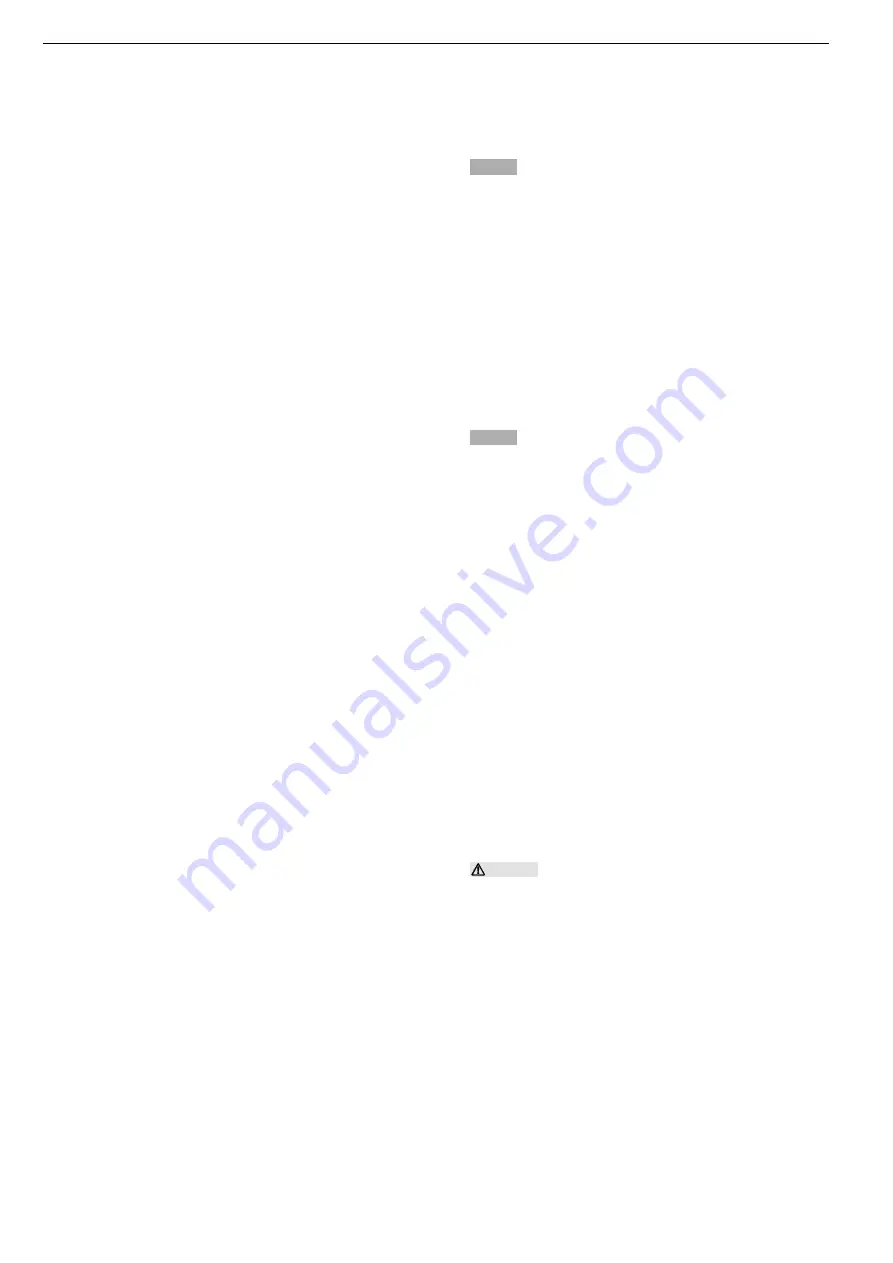
eng
eng
ROLLER’S Akku-Exparo Q & E,
ROLLER’S Multi-Press Mini ACC,
ROLLER’S Axial-Press 25 ACC and 25 L ACC
ROLLER’S Akku-Exparo Cu,
ROLLER’S Akku-Exparo P
14.4 V =; 1.3 Ah; 18 A
Rapid charger
Li-Ion/Ni-Cd (1h)
Input
230 V~; 50 – 60 Hz; 65 W
Output
10,8 – 18 V –
---
Voltage supply 230 V
Input
230 V~; 50 – 60 Hz
Output
14,4 V –
---; 6 A – 33 A
1.5. Dimensions
ROLLER’S Uni-Press E
430×110×85 mm (16.9”×4.3”×3.3”)
ROLLER’S Uni-Press,
ROLLER’S Uni-Press ACC
365×235×85 mm (14.4”×9.2”×3.3”)
ROLLER’S Multi-Press Mini ACC
288×260×80 mm (11.3”×10.2”×3.1”)
ROLLER’S Multi-Press,
ROLLER’S Multi-Press ACC
338×290×85 mm (13.3”×11.4”×3.3”)
ROLLER’S Axial-Press 15/40
330×320×85 mm (13”×12.6”×3.3”)
ROLLER’S Akku-Exparo Q & E
290×260×80 mm (11.4”×10.2”×3.1”)
ROLLER’S Axial-Press 25 ACC
295×260×80 mm (11.6”×10.2”×3.3”)
ROLLER’S Axial-Press 25 L ACC
325×260×80 mm (12.8”×10.2”×3.1”)
ROLLER’S Akku-Exparo Cu
265×260×80 mm (10.4”×10.2”×3.1”)
ROLLER’S Akku-Exparo P
275×260×80 mm (10.8”×10.2”×3.1”)
1.6. Weights
ROLLER’S Uni-Press E drive unit
4.4 kg
(9.6 lb)
ROLLER’S Uni-Press drive unit
4.6 kg (10.0 lb)
ROLLER’S Uni-Press ACC drive unit
4.6 kg (10.0 lb)
ROLLER’S Multi-Press Mini ACC drive unit without battery 2.1 kg
(4.5 lb)
ROLLER’S Multi-Press / Multi-Press ACC
drive unit without battery
3.8 kg
(8.3 lb)
ROLLER’S Axial-Press 15 drive unit without battery
4.6 kg (10.0 lb)
ROLLER’S Axial-Press 40 drive unit without battery
5.4 kg (11.8 lb)
ROLLER’S Akku-Exparo Q & E drive unit without battery 2.0 kg
(4.4 lb)
ROLLER’S Axial-Press 25 ACC drive unit without battery 2.6 kg
(5.6 lb)
ROLLER’S Axial-Press 25 L ACC drive unit without battery 2.8 kg
(6.1 lb)
ROLLER’S Akku-Exparo Cu drive unit without battery
2.3 kg
(5.0 lb)
ROLLER’S Akku-Exparo P drive unit without battery
2.0 kg
(4.3 lb)
ROLLER’S battery Li-Ion 14.4 V, 1.3 Ah
0.3 kg
(0.6 lb)
ROLLER’S battery Li-Ion 14.4 V, 2.2 Ah
0.5 kg
(1.1 lb)
Pressing tongs (average)
1.8 kg
(3.9 lb)
Pressing tongs Mini (average)
1.2 kg
(2.6 lb)
Pressing heads (pair, average)
0.3 kg
(0.6 lb)
Expanding head (average)
0.2 kg
(0.4 lb)
Adapter tong Z2
2.0 kg
(4.8 lb)
Adapter tong Z4
3.6 kg
(7.8 lb)
Adapter tong Z5
3.8 kg
(8.2 lb)
Pressing ring M54
3.1 kg
(6.7 lb)
Pressing ring U75 (3S)
6.4 kg (13.8 lb)
Pressing ring U75 (3B)
2.7 kg
(5.9 lb)
1.7. Noise information
Emission at workplace
ROLLER’S Uni-Press E
L
pA
= 76 dB
L
WA
= 87 dB K = 3 dB
ROLLER’S Uni-Press /
ROLLER’S Uni-Press ACC
L
pA
= 81 dB
L
WA
= 92 dB K = 3 dB
ROLLER’S Multi-Press Mini ACC L
pA
= 73 dB
L
WA
= 84 dB K = 3 dB
ROLLER’S Multi-Press /
Multi-Press ACC
L
pA
= 74 dB
L
WA
= 85 dB K = 3 dB
ROLLER’S Axial-Press 15 / 40
L
pA
= 74 dB
L
WA
= 85 dB K = 3 dB
ROLLER’S Axial-Press 25 ACC /
25 L ACC
L
pA
= 73 dB
L
WA
= 84 dB K = 3 dB
ROLLER’S Akku-Exparo Q & E
L
pA
= 73 dB
L
WA
= 84 dB K = 3 dB
ROLLER’S Akku-Exparo Cu
L
pA
= 73 dB
L
WA
= 84 dB K = 3 dB
ROLLER’S Akku-Exparo P
L
pA
= 73 dB
L
WA
= 84 dB K = 3 dB
1.8. Vibrations
Weighted effective value of acceleration
< 2.5 m/s² K = 1.5 m/s²
The indicated weighted effective value of acceleration has been measured
against standard test procedures and can be used by way of comparison with
another device. The indicated weighted effective value of acceleration can also
be used as a preliminary evaluation of the exposure.
Attention:
The indicated weighted effective value of acceleration can differ
during operation from the indicated value, dependent on the manner in which
the device is used. Dependent upon the actual conditions of use (periodic duty)
it may be necessary to establish safety precautions for the protection of the
operator.
2. Preparations for Use
The respective latest sales literature applies for the use of ROLLER pressing
tongs, ROLLER pressing tongs Mini, ROLLER pressing rings, ROLLER adapter
tongs, ROLLER pressing heads and ROLLER expanding heads for the different
pipe connection systems. If the system manufacturer alters components of pipe
connection systems or markets new ones, their current application status must
be enquired about at ROLLER (Fax +49 7151 17 27 - 87).
2.1. Electrical connection
Note the mains voltage! Before connecting the drive unit or the rapid charger,
check whether voltage on the rating plate matches the mains voltage. At work
sites, in damp surroundings, in the open or in the case of comparable types of
use, only operate the equipment off the mains using a 30 mA fault current
protected switch (FI breaker).
Rechargeable batteries
NOTICE
Always hold the battery upright when inserting it in the drive unit or
the rapid charger. If inserted at an angle it can cause damage to the contacts
and result in a short circuit which damages the battery.
The rechargeable battery supplied with ROLLER drive units and spare recharge-
able batteries are not charged. Charge the battery before use. Only use a
ROLLER rapid charger for charging. The rechargeable batteries only reach
their full capacity after being charged several times. Li-ion batteries should be
recharged regularly in order to avoid their total discharge. The rechargeable
battery will be damaged by exhaustive discharge. Non-rechargeable batteries
may not be charged.
Rapid charger Li-Ion/NiCd (Art. No. 571560)
The left control lamp lights up and remains green when the mains plug is
plugged in. If a battery is inserted in the rapid charger, the green control lamp
flashes to indicate that the battery is charging. The green light stops flashing
and remains on to signal that the battery is fully charged. If the red control lamp
flashes, the battery is defective. If the red control lamp comes on and remains
on, this indicates that the temperature of the rapid charger and / or the battery
is outside the permissible range of +5°C to +40°C.
NOTICE
The rapid chargers are not suitable for outdoor use.
2.2. Installing (changing) the pressing tong, pressing tong Mini (1), the pressing
ring with adapter tong (Fig. 18) in radial presses (Fig. 1, 16 and 17)
Pull out the mains plug or remove the battery. Only use pressing tongs, pressing
tongs Mini or pressing rings with system-specific pressing contour according
to the pressfitting system to be pressed. ROLLER pressing tongs, pressing
tongs Mini or pressing rings have letters on the pressing jaws or pressing
segments to identify the pressing contour and a number to identify the size.
Read and follow the installation and assembly instructions of the system
manufacturer. The ROLLER adapter tongs are also identified by a letter and a
number. This identification serves to assign them to the permissible ROLLER
pressing ring. Never use non-matching pressing tong and pressing ring and
adapter tong (pressing contour, size). The press joint could be rendered useless
and the machine and pressing tong, pressing tong Mini or pressing ring and
adapter tong could be damaged.
It is best to place the drive machine on a bench or on the floor. The pressing
tong, pressing tong Mini or adapter tong can only be installed (changed) when
the press rollers (5) are fully retracted. If necessary, in the case of the ROLLER’S
Uni-Press E, set the rotation direction lever (7) to the left and operate the inching
switch (8), and in the case of the ROLLER’S Uni-Press and ROLLER’S Multi-
Press press the reset button (13) until the press rollers (5) are fully retracted.
Open the tongs shank (2). To do so, press the locking pin (4), the tongs shank
(2) jumps out under spring loading. Insert the selected pressing tong, pressing
tong Mini (1) or adapter tong (19). Push forward the tong retaining bolt (2) until
the locking pin (4) snaps into place. Press down the pressure plate (3) directly
over the tong retaining bolt. Do not start radial presses without pressing tong,
pressing tong Mini or pressing ring with adapter tong inserted. Only start the
pressing process to make a press joint. Without pressing counterpressure by
the press fitting the drive machine or pressing tong, pressing tong Mini, pressing
ring and adapter ring will be exposed to unnecessarily high stress.
CAUTION Never operate press when the tongs shank (2) is not locked.
Risk of fracture!
2.3. Installing (changing) the pressing heads (14) in axial presses
(Figs. 6, 7, 10)
Remove the battery. Only use system-specific pressing heads. ROLLER press ing
heads have a letter to identify the compression sleeve system and a number
to identify the size. Consult and comply with the instructions for installation and
fitting of the system’s manufacturer. Never use non-matching pressing heads
(compression sleeve system, size) for pressing work. The press joint could be
unserviceable, and both the machine and the press ing heads might be damaged.
Push the selected pressing heads (14) right in, if necessary turning them until
they engage (ball catch). Keep the pressing heads and locating hole inside the
pressing device clean.
2.4. Installing (changing) the expanding head (16) in ROLLER’S Axial-Press
15 (Fig. 6)
Remove the battery. Fit the expander (15) (accessory) To do so, clean the
connecting surfaces, attach the expander, and tighten the two fillister-head
screws. Grease the cone of the expanding mandrel (18) lightly. Screw the
selected expanding head as far as it will go onto the expander. Only use
system-specific expanding heads. ROLLER expanding heads have a letter to
identify the compression sleeve system and a number to identify the size.
Consult and comply with the instructions for installation and fitting of the system’s
manu facturer. Never use non-matching expanding heads (compression sleeve
system, size) for expansion work. The press joint could be unserviceable, and
both the machine and the expanding heads might be damaged.
Содержание Akku-Exparo Cu
Страница 3: ...15 18 6 8 9 13 23 16 Fig 13 Fig 14 Fig 11 Fig 10 Fig 15 14 6 8 9 13 23 15 18 6 8 9 13 23 16 Fig 12 ...
Страница 4: ...Fig 16 4 G Fig 17 S A B A B Fig 18 PR 3S Fig 19 PR 3B B A 19 20 21 B A 19 20 ...
Страница 52: ...12 2010 570285 A Änderungen und Irrtümer vorbehalten Copyright 2010 by Albert Roller GmbH Co KG Waiblingen ...