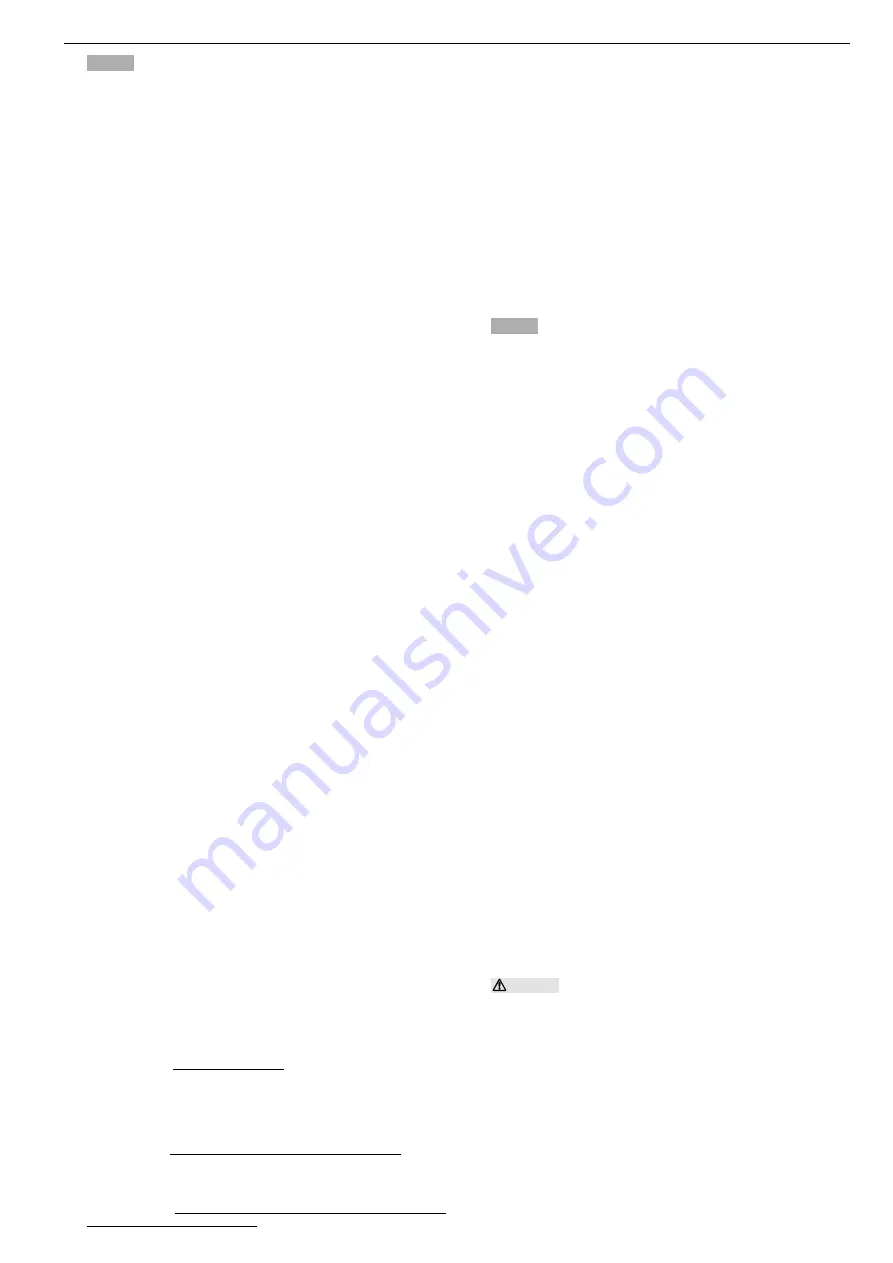
eng
eng
NOTICE
Ensure that the compression sleeve has sufficient clearance from
the expanding head during the expansion process, otherwise the expanding
jaws (17) might become bent or broken.
For pressing jobs in cramped places, the expander attachment can be removed.
2.5. Installing (changing) the expanding head (16) in ROLLER’S Akku-Exparo
Q & E (Fig. 8)
Pull out the mains plug or remove the battery. Only use genuine expanding
heads for Uponor Quick & Easy. Consult and comply with the instructions for
installation and fitting of the system’s manufacturer. Never use non-matching
expanding heads (system, size) for expansion work. The joint could be unserv-
iceable, and both the machine and the expanding heads might be damaged.
Grease the cone of the expanding mandrel (18) lightly. Screw the selected
expanding head as far as it will go onto the expander. Read and follow the
installation and assembly instructions of the system manufacturer. ROLLER
expanding heads P and Cu are not suitable for the Akku pipe expander
ROLLER’S Akku-Exparo Q & E and must therefore not be used.
2.6. Mounting (changing) the expanding head (16) on the ROLLER’S Akku-
Exparo Cu (Fig. 12)
Remove the battery. Grease the cone of the expanding mandrel lightly. Screw
the selected expanding head onto the expanding device to the stop. The
expanding device must now be set so that the thrust of the drive machine is
taken up by the drive machine and not the expanding head at the end of the
expanding. Unscrew the expanding device complete with screwed on expanding
head from the drive machine for this. Let the feed piston run forward as far as
possible without the machine switching into reverse. In this position the expanding
device complete with screwed on expanding head must be screwed onto the
drive machine until the segments of the expanding head are fully open. The
expanding head must be secured with the locking nut in this position.
2.7. Mounting (changing) the expanding head (16) on the ROLLER’S Akku-
Exparo P (Fig. 11)
Remove the battery. Grease the cone of the expanding mandrel (18) lightly.
Screw the selected expanding head onto the expanding device to the stop.
Only use system-specific expanding heads. ROLLER’S expanding heads are
labelled with letters to identify the compression sleeve system and with a number
to identify the size. Read and follow the installation and assembly instructions
of the system manufacturer. Never expand with the wrong expanding heads
(compression sleeve system, size). The connection could be useless and the
machine and expanding heads could be damaged.
3. Operation
3.1. Radial presses (Figs. 1 to 6 and 16 to 19)
A test pressing with inserted press fitting must be made with the drive machine
and the respectively inserted pressing tong, pressing tong Mini or pressing ring
with adapter tong before every use. The pressing tong, pressing tong Mini (1),
pressing ring (20) or pressing segments (21) must close fully. Full closure of
the pressing jaws (10), pressing rings (20) or pressing formers (21) both at their
tips (Fig. 1, and Fig. 16 to 19 at "A") and on the opposite side (Fig. 1 and Fig.
16 to 19 at "B") can be observed after completing the pressing. Check the
tightness of the connection (observe national specifications, standards, regula-
tions, etc.)
The pressing tong, pressing tong Mini or pressing ring and adapter tong, and
especially the pressing contour (11 / 22) of both pressing jaws (10) or all 3
pressing segments must be checked for damage and wear before every use.
Damaged or worn pressing tongs, pressing tongs Mini or pressing rings may
no longer be used. There is otherwise a risk of incorrect pressing or accidents.
If during closing of the pressing tongs, pressing tongs Mini a marked ridge is
created on the compression sleeve, the pressing may be defective or not tight
(see 5. Trouble).
3.1.1. Working procedure
Press the pressing tongs, pressing tongs Mini (1) together manually until they
can be pushed over the press fitting. Always position the drive unit with the
pressing tongs on the press fitting at right angles to the pipe axis. Release the
pressing tongs so that they close around the press fitting. Hold the drive unit
by the housing grip (6) and the pistol grip (9).
Place the pressing ring (20) around the pressing fitting. Insert the pressing tong
(19) into the press and lock the tong retaining bolt. Press the pressing tong
(19) together with your hand so that the adapter tong can be placed on the
pressing ring. Release the adapter tong so that the adapter tong is tightly applied
to the pressing ring and the pressing ring to the pressfitting.
In the case of the ROLLER’S Uni-Press E, set the rotation direction lever (7)
to the right (advance) and press the inching switch (8). Keep the inching switch
(8) pressed until the pressing is finished and the pressing tong or pressing ring
is closed. Set the rotation direction lever (7) to the left (return) and press the
switch (8) until the press rollers have retracted and the slipping clutch responds.
Do not put unnecessary loads on the slipping clutch.
In the case of the ROLLER’S Uni-Press and ROLLER’S Multi-Press, keep the
inching switch (8) pressed until the pressing is finished and the pressing tong
or pressing ring is completely closed. This is indicated by an acoustic signal
(clicking). Press the reset button (13) until the press rollers (5) are fully retracted.
In the case of the ROLLER’S Multi-Press Mini ACC, ROLLER’S Multi-Press
ACC and ROLLER’S Uni-Press ACC, keep the inching switch (8) pressed until
the pressing is finished and the pressing tong or pressing ring is completely
closed. After completion of press ing, the drive unit switches automati cally to
return (forced return).
Press the pressing tongs together manually so that they can be removed from
the press fitting. Press the pressing tong together with your hand so that it can
be removed from the pressfitting. Press the adapter tong together with your
hand so that it can be removed from the pressing ring with the device. Open
the pressing ring by hand so that it can be pulled off the pressfitting.
3.1.2. Operating safety
In the case of the ROLLER’S Uni-Press E, the pressing operation is ended by
releasing the inching switch (8). For the mechanical safety of the drive units,
a torque-controlled safety slipping clutch is operative in both end positions of
the press rollers.
The ROLLER’S Uni-Press and ROLLER’S Multi-Press ends the pressing
opera tion automatically, emitting an acoustic signal (clicking). The ROLLER’S
Multi-Press Mini ACC, ROLLER’S Multi-Press ACC and ROLLER’S Uni-Press
ACC ends the pressing operation automatically, emitting an acoustic signal
(clicking), and returns automatically (forced movement).
NOTICE
A perfect pressing is only produced with full closure of the
pressing tongs, mini pressing tongs or pressing ring. Full closure of the
pressing jaws (10), pressing rings (20) or pressing formers (21) both at
their tips (Fig. 1 and Fig. 16 to 19 at "A") and on the opposite side (Fig. 1
and Fig. 16 to 19 at "B") can be observed after completing the pressing.
If a visible burr is created on the pressing sleeve when closing the pressing
tong or pressing segment, the pressing may be faulty or leaking (see 5.
Trouble).
3.1.3. Working safety
To ensure safe working, the drive units are equipped with a safety inching
switch. This permits immediate switching off of the drive units at any time,
particularly if a potential hazard arises. The drive units can be switched to the
return function in any position.
3.2. Axial presses (Figs. 6, 7, 10)
3.2.1. Pressing with the ROLLER’S Axial-Press 15 and Axial-Press 40 (Fig. 6, 7)
Place the preassembled compression sleeve fitting inside the pressing heads
(14) and press them into the latter. Hold the drive unit by the housing grip (6)
and the pistol grip (9), and keep the inching switch (8) pressed until the compres-
sion sleeve is in contact with the collar of the compression sleeve fitting. This
is also indicated by an acoustic signal (clicking). Press the reset button (13)
until the pressing heads (14) are fully retracted.
Pressing with ROLLER’S Axial-Press 25 ACC, ROLLER’S Axial-Press 25 L
ACC (Fig. 10)
Hold the drive machine either with one hand on the switch handle (9) or two
hands on the housing handle (6) and the switch handle (9). Keep the inching
switch (8) pressed until the compression sleeve is touching the collar of the
compression sleeve connector. The drive machine then switches automatically
to return (forced return).
With the compression sleeve system IV, various pressing heads are needed
for one pipe size. Consult and comply with the instructions for installation and
fitting of the system’s manufacturer.
In the case of the compression sleeve system RV, preliminary and final pressing
is necessary, i.e. the pressing heads must first be inserted with a wide spacing
of the receptacles for the compression sleeve fitting. Before a second pressing
operation, the pressing heads are set to a narrow spacing of the receptacles
for the compression sleeve fitting by a 180° rotation. Consult and comply with
the instructions for installation and fitting of the system’s manufacturer.
The ROLLER’S Axial-Press 25 L ACC must be used for the BA/SP/UNI compres-
sion sleeve systems. Note that the compression heads must be inserted into
the pressing machine in such a way that the pressing can be done in one stroke
if possible. This is not possible in some cases and pre-pressing and finish
pressing is necessary. For this one compression head or both compression
heads must be inserted turned 180° before the second pressing process so
that they are closer together. Read and follow the installation and assembly
instructions of the system manufacturer.
CAUTION Danger of cru shing! Keep your hands away from the moving
pressing heads (14)!
3.2.2. Expansion with ROLLER’S Axial-Press 15 (Fig. 6)
Push the compression sleeve over the pipe, insert the expanding head as far
as it will go into the pipe, and press the expanding head/drive unit against the
pipe. Switch on the drive unit (8). Ensure that the compres sion sleeve has
during the expansion process sufficient clearance from the expanding head,
otherwise the expanding jaws (17) might become bent or broken. Hold down
the inching switch (8) until the pipe has been expanded. This is also indicated
by an acoustic signal (clicking). Press the reset button (13) until the expanding
head has closed again. If necessary repeat the expansion. Consult and comply
with the instructions for installation and fitting of the system’s manufacturer.
3.3. ROLLER’S Akku-Exparo Q & E (Fig. 8)
Consult and comply with the instructions for installation and fitting of the system’s
manufacturer. Slide a Q & E ring of appropriate size onto the pipe. Insert the
expansion head into the pipe and press the expanding head/drive unit against
the pipe. Switch on the drive unit (8). When the expanding head is opened, the
Содержание Akku-Exparo Cu
Страница 3: ...15 18 6 8 9 13 23 16 Fig 13 Fig 14 Fig 11 Fig 10 Fig 15 14 6 8 9 13 23 15 18 6 8 9 13 23 16 Fig 12 ...
Страница 4: ...Fig 16 4 G Fig 17 S A B A B Fig 18 PR 3S Fig 19 PR 3B B A 19 20 21 B A 19 20 ...
Страница 52: ...12 2010 570285 A Änderungen und Irrtümer vorbehalten Copyright 2010 by Albert Roller GmbH Co KG Waiblingen ...