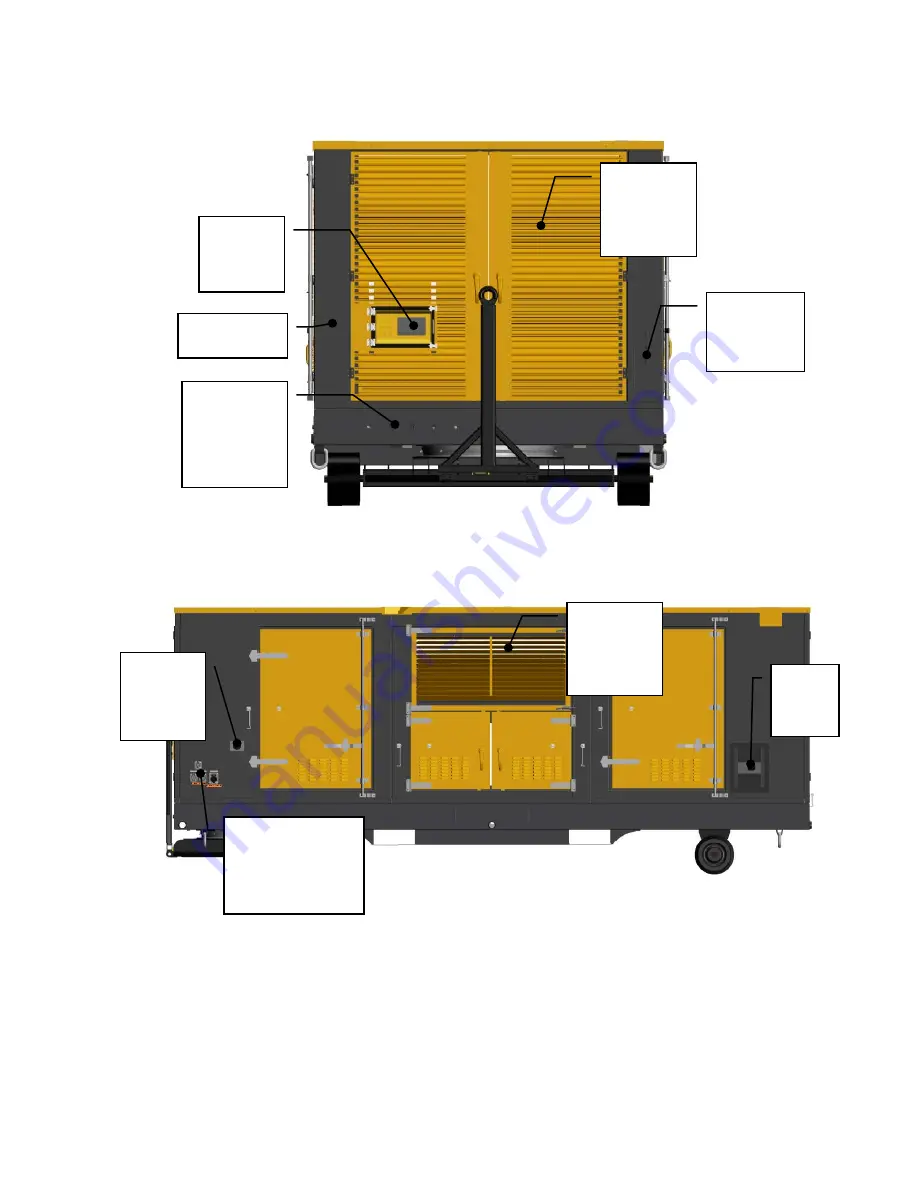
15
FRONT VIEW
SIDE VIEW
FIGURE 6B- COMPRESSOR EXTERIOR
Control
Panel /
Interface
(HMI)
Cooling Air
Louvers
(Leave
Doors
Closed)
Cooling Air
Louvers
(Leave
Doors
Closed)
Diesel
Exhaust
Fluid
(DEF)
Tank Fill
Diesel
Fuel
Tank
Fill
External
DEF and
Fuel Tank
Connections
120VAC Heat
Trace / Battery
Charger Ports/
400W Dryer Power
Outlet
Engine Oil,
Compressor
Oil, Engine
Coolant
Service Drain
Ports
Emergency
Stop
Содержание GPKD-1550-H
Страница 2: ...2 THIS PAGE LEFT BLANK...
Страница 22: ...22 Note The design of the oil pan is not the extended type as shown in the diagram FIGURE 10b ENGINE RIGHT SIDE...
Страница 47: ...47...
Страница 48: ...48 THIS PAGE LEFT BLANK...